Are you familiar with the common challenges faced in service and after-sales within the equipment manufacturing sector? Information related to service, maintenance, and product lifecycle management is often fragmented, with maintenance typically being performed on a reactive basis. Our EquipmentCloud® customer portal centralizes all of your essential information in one place, opening up new data-driven business models along the way. Our flexible, interactive modules simplify the digitalization and scaling of your service offerings, while we ensure the security of your data-driven services. Your customers enjoy a first-class experience, and your after-sales service gains the recognition it deserves.
Proven added value for stakeholders in equipment manufacturing
- Proven digital transformation solution that allows you to get started right away
- Optimize the use of your skilled workers by reducing unnecessary travel and making work processes more efficient
- Increase competitiveness and revenue potential with data-based services
- Improved customer retention with services and touchpoints along the entire machine life cycle
- Continuous monitoring of your machines and components
- Integrated remote service solution for remote maintenance
- Expand your service business along the entire machine life cycle
- Information relevant to machines can be accessed on a mobile device at any time in the service and customer portal
- Early notification of downtimes and upcoming maintenance
- Always keep an eye on machine figures and react immediately
Application scenarios with EquipmentCloud®
-
The EquipmentCloud® service and customer portal is your central hub. As a unified platform, it connects operators and machine manufacturers to simplify service and collaboration through machine lifecycle records and open item lists.
-
EquipmentCloud® puts you in control of your machines. Monitor your equipment fleets worldwide and quickly and easily conduct performance analyses.
-
Complex commissioning processes are clearly structured and easily executed with EquipmentCloud®. Recurring workflows are efficiently planned and seamlessly implemented.
-
Predictive maintenance is easier than ever with EquipmentCloud® – from planning to execution and documentation.
-
Securely manage your global fleet of IoT devices with EquipmentCloud®. Perform over-the-air firmware and software updates reliably and securely.
Configurable modules to efficiently scale your use case
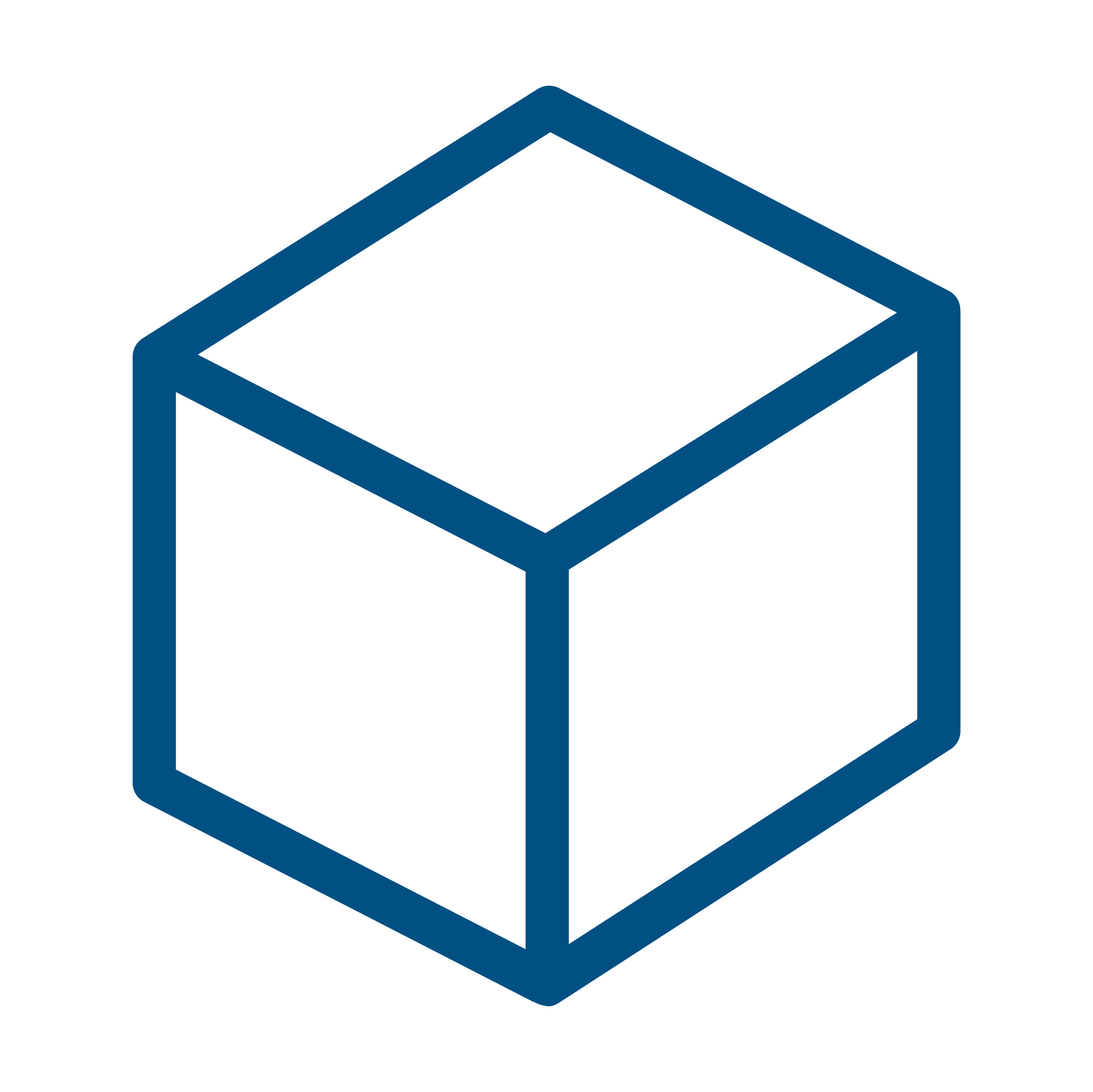
- Components
- Conditional and interactive master data
- Contact management
- Journal with templates
Your added value
- Guided configuration
- Working efficiently
- Data synchronization with third-party systems
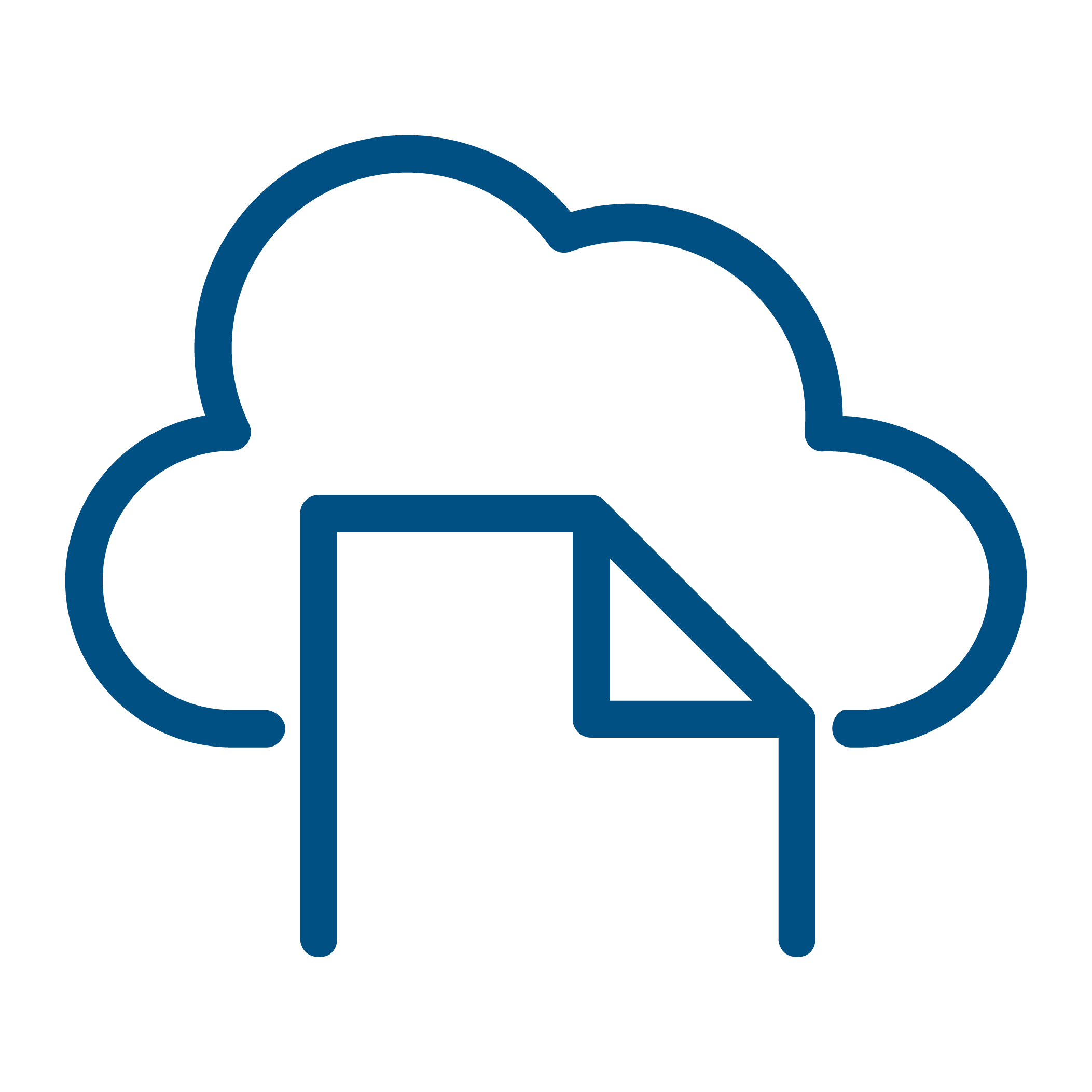
- Support for various file formats
- Global sharing and assignment to machines, types, and hierarchies
- Quick access and download of files
Your added value
- User-specific access to documents
- Minimal maintenance
- Multi-user capable
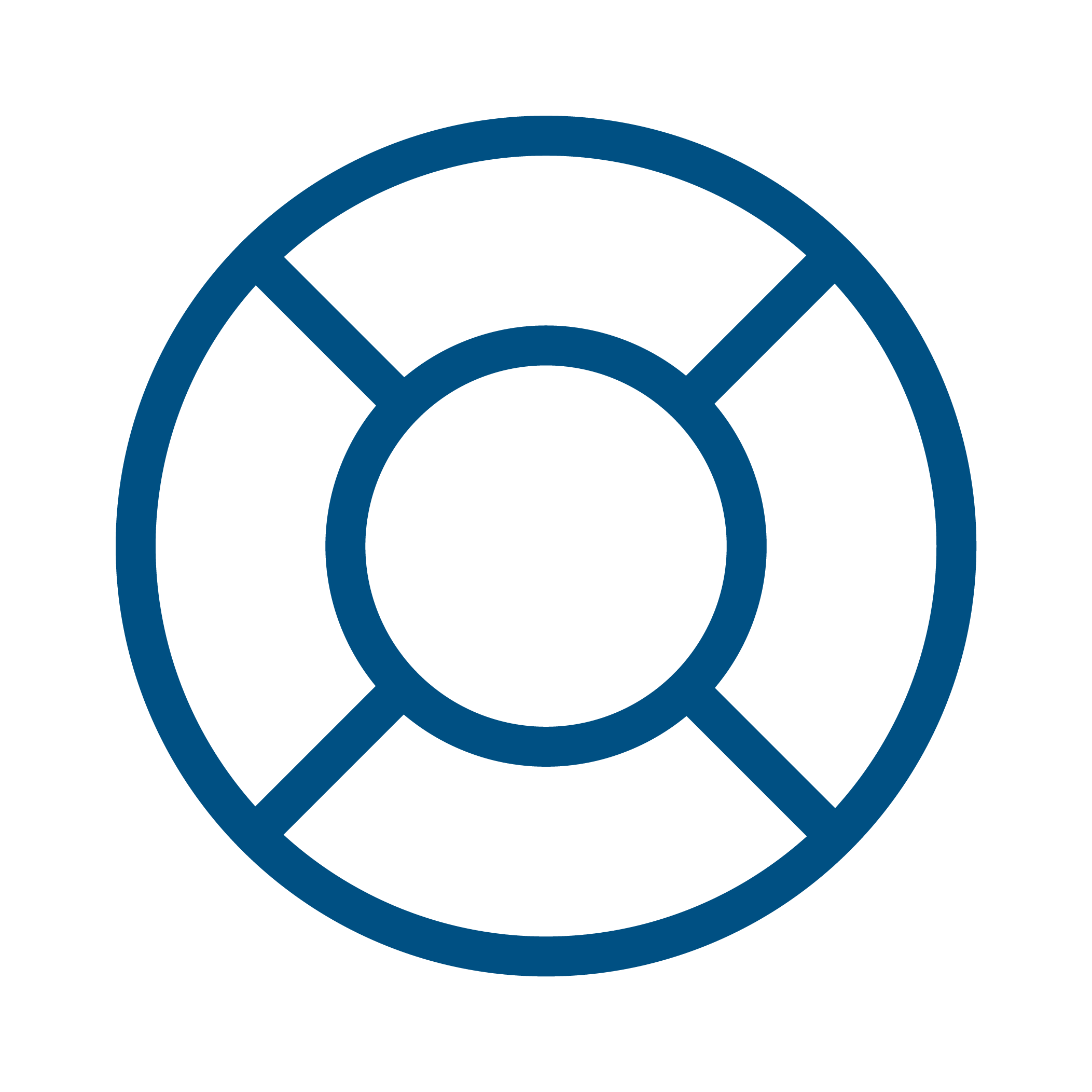
- Support for various file formats
- Global sharing and assignment to machines, types, and hierarchies
- Quick access and download of files
Your added value
- User-specific access to documents
- Minimal maintenance
- Multi-user capable
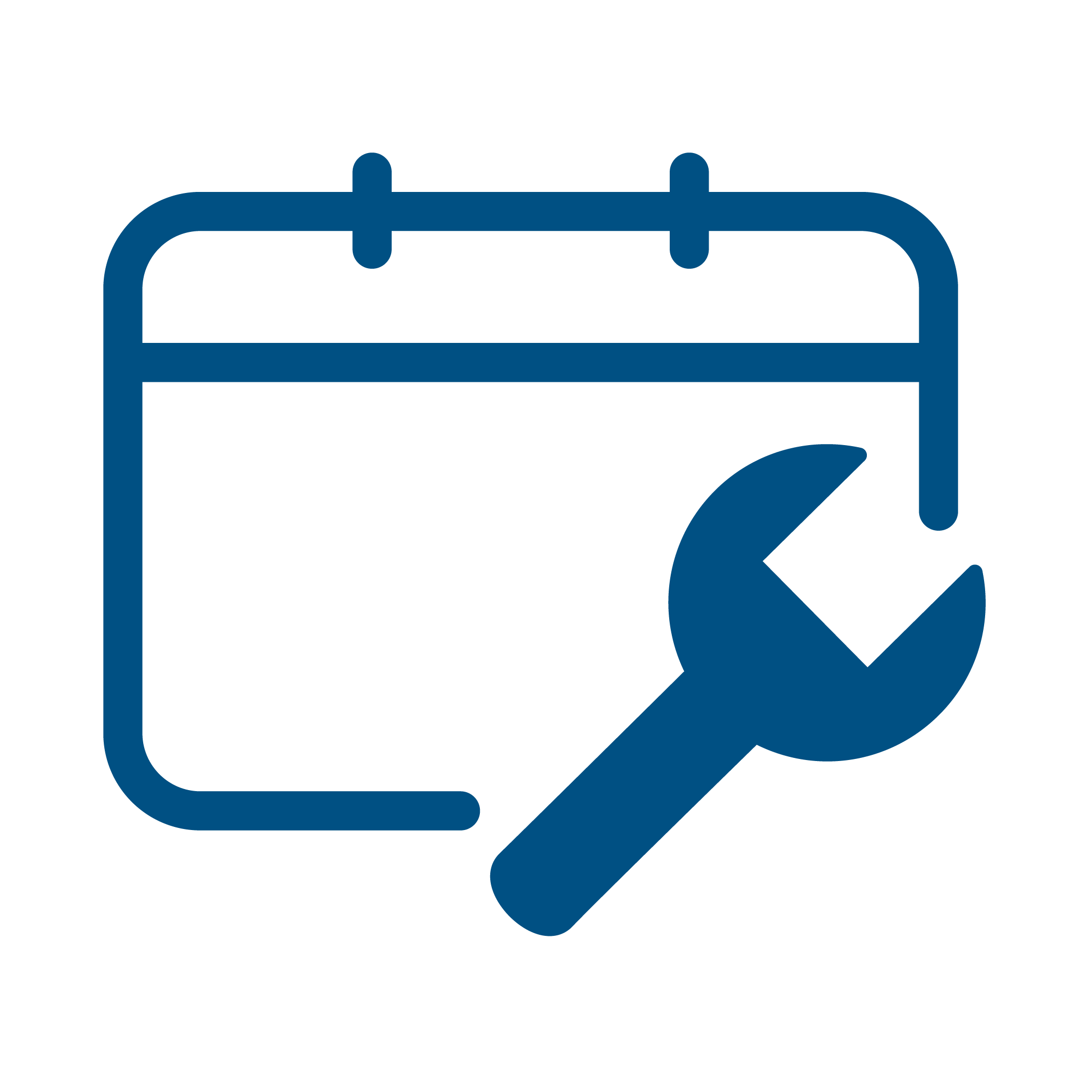
- Preventive and predictive maintenance and repair based on machine data
- Preparation of maintenance schedules based on checklists
- Carrying out planned maintenance and ad hoc repairs
- Illustrated instructions
- Subscription feature
Your added value
- Comply with maintenance contracts
- Highlight service portfolio
- Save time and resources
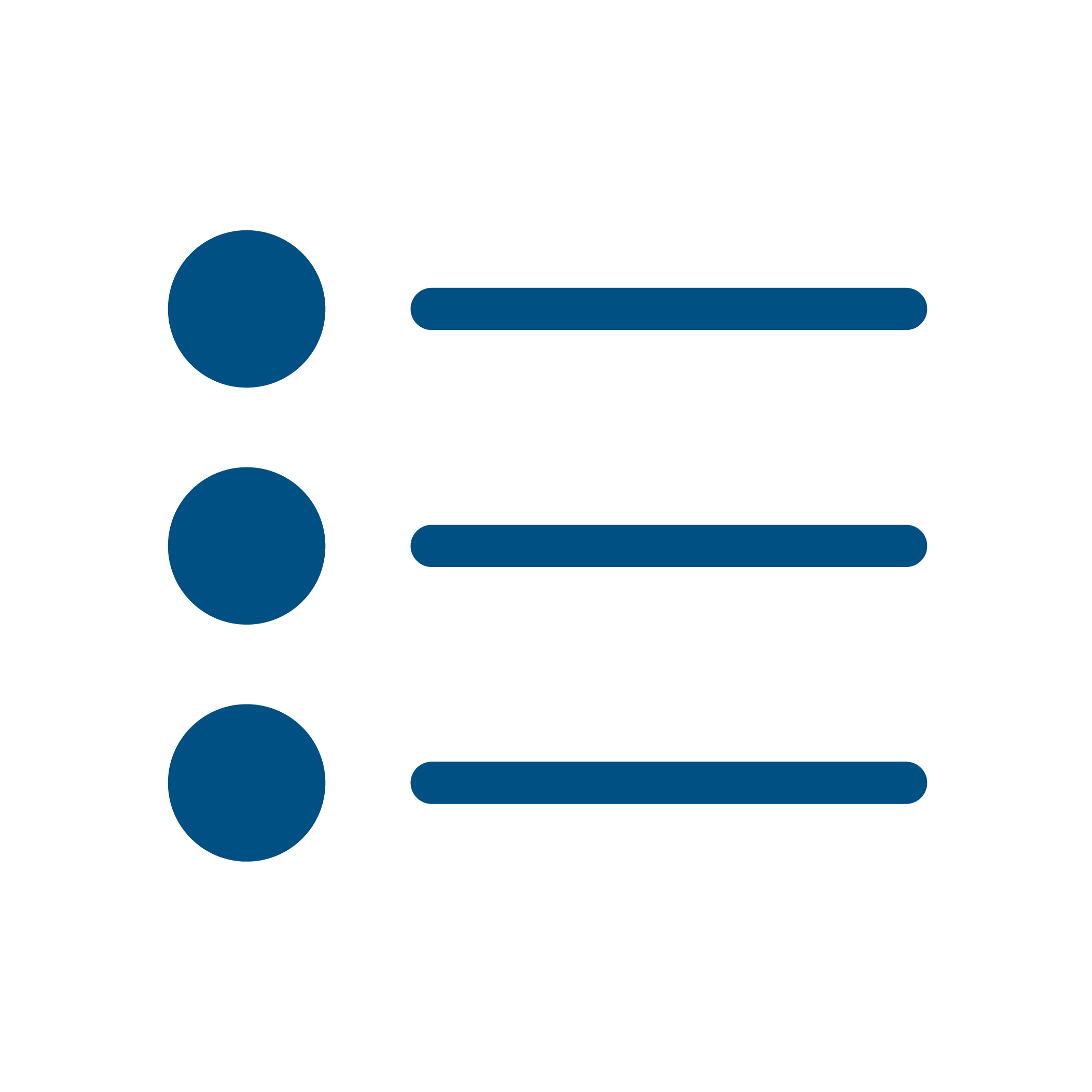
- Modern task board design
- Representation of parallel and multiple processes
- Preparation of checklists with predefined parameters
- Subscription feature
- Assignment of responsibilities
Your added value
- Standardized and auditable processes
- Ensuring punctuality
- Increasing commissioning efficiency
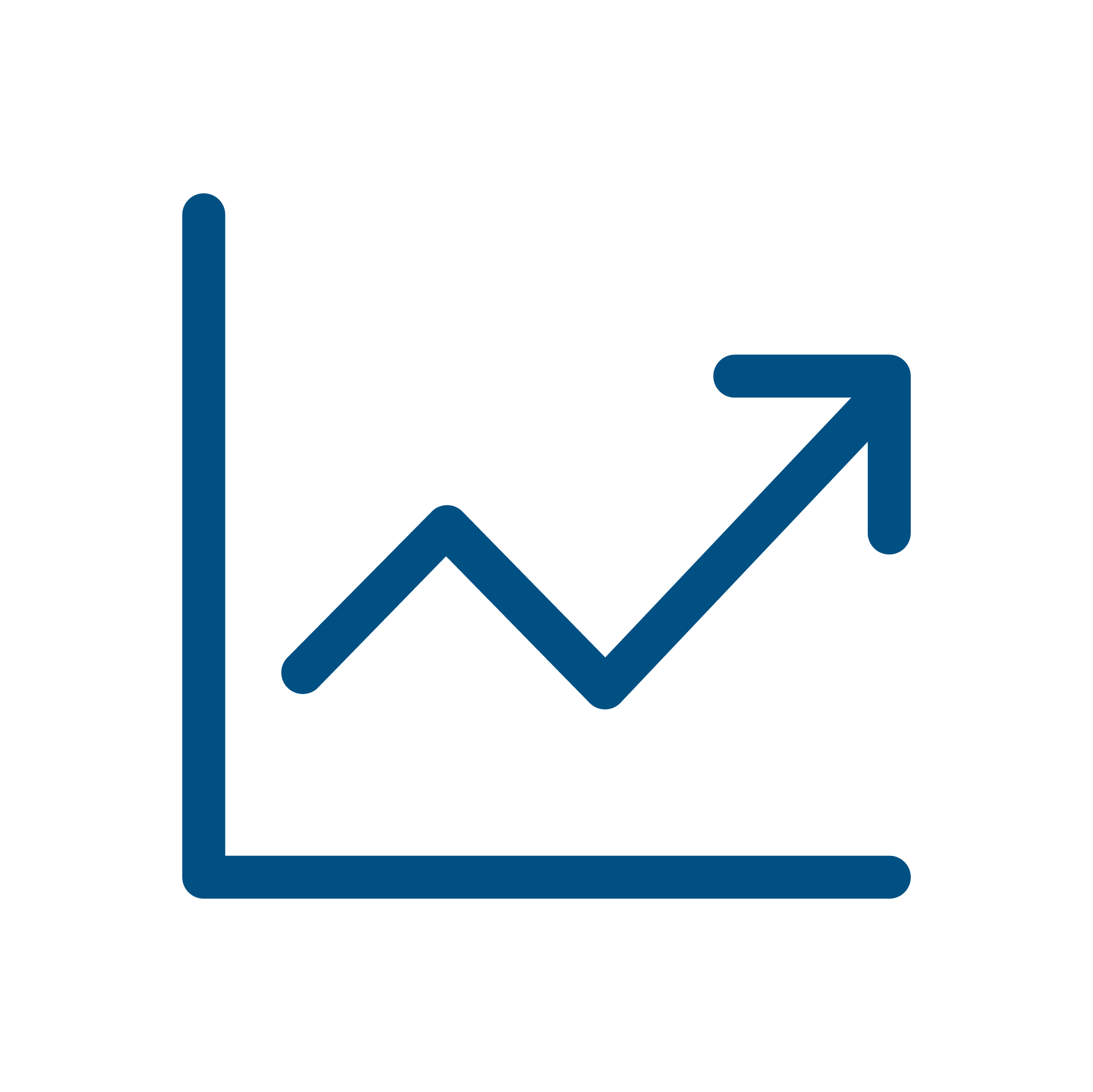
- Systematic evaluation of alarms, status, process values and throughput
- Determination of production relevant key figures according to individual KPI models
- Extensive reporting and filtering functions
- Basis for preventive and predictive maintenance
Your added value
- Easy troubleshooting and identification
- Comparabiity of machine performance
- Increased productivity
- Automated alerting

- Overview of installed software versions
- Preparation and approval of software packages
- Automatically distribute and update software
- Global approval and allocation of software
- Direct download
Your added value
- Correlation of errors and problems with software
- Save time and resources
- Transparent software documentation
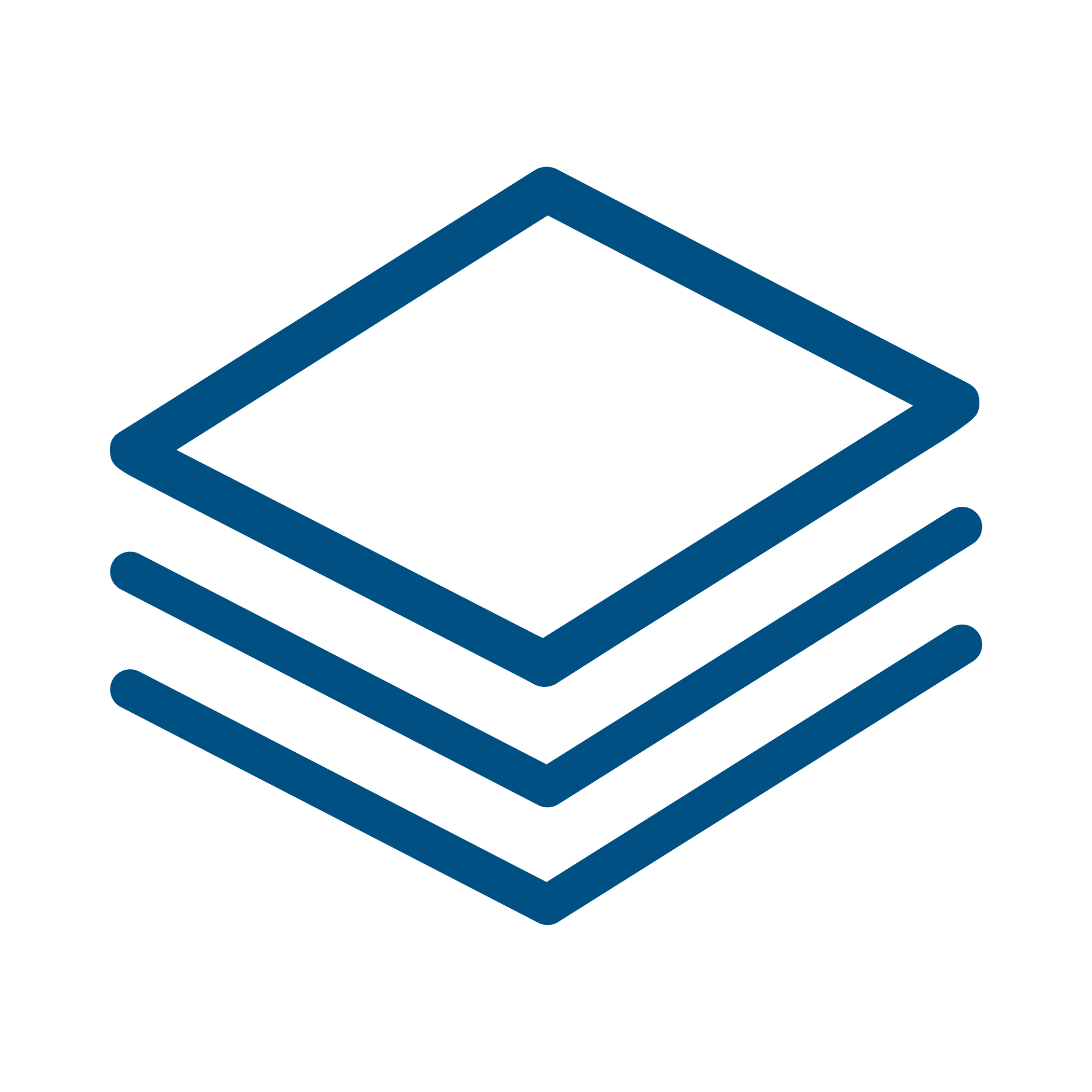
- Spare parts management with integrated parts catalog
- Shopping cart function and order tracking
- Quick overview of order history
- Subscription feature
- Interface for connecting external 3D spare parts catalogs
Your added value
- Proactive spare parts service
- Transparent ordering process
- Machine-specific spare parts catalog
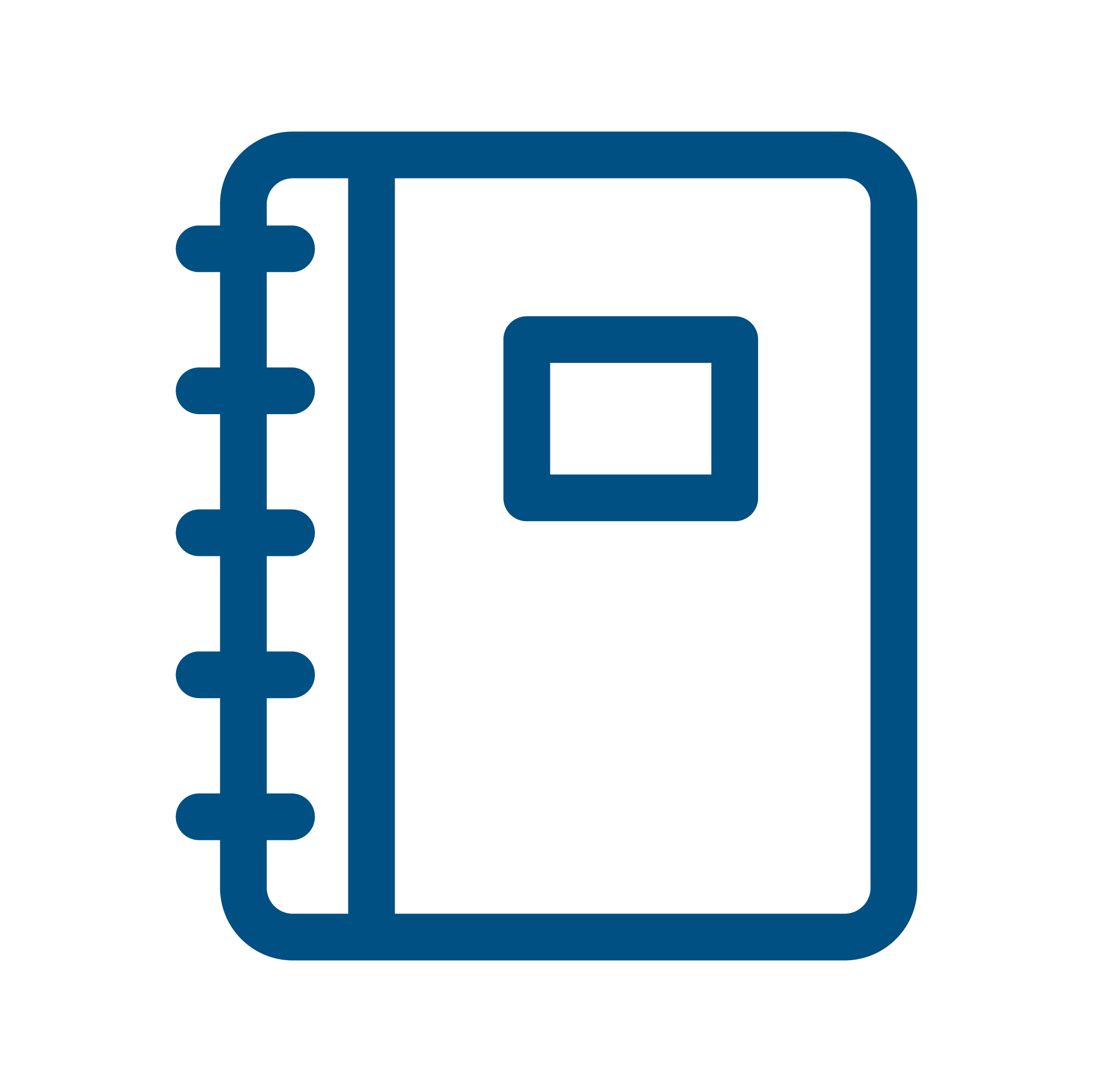
- Documentation of user-related solutions to common problems
- Indexed search function
- Rating and comment function
- Publishing mechanism
Your added value
- Implementation of a continuous improvement process (CIP)
- Sustainable knowledge transfer
- Establishing a self-service or sharing mindset
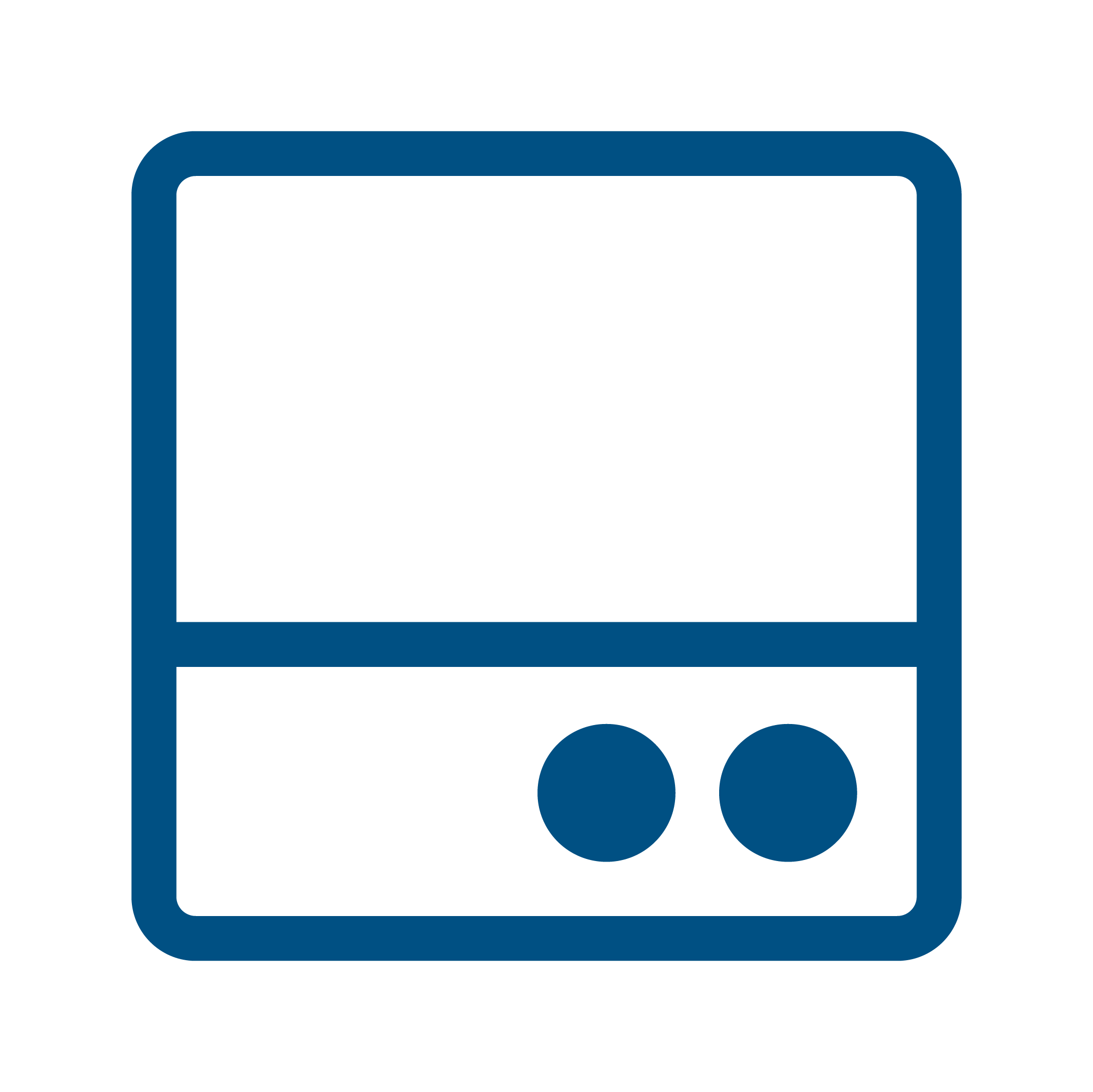
- Centralized management of individual devices and device groups
- Fleet management: carry out mass updates using templates
- Encapsulate customer applications in Docker containers
- Secure and hardened operating system
- Establishing temporary VPN connections
Your added value
- Save time
- Minimize complexity
- Efficient fault diagnostics
- Reduced installation and service costs
- End-to-end encryption
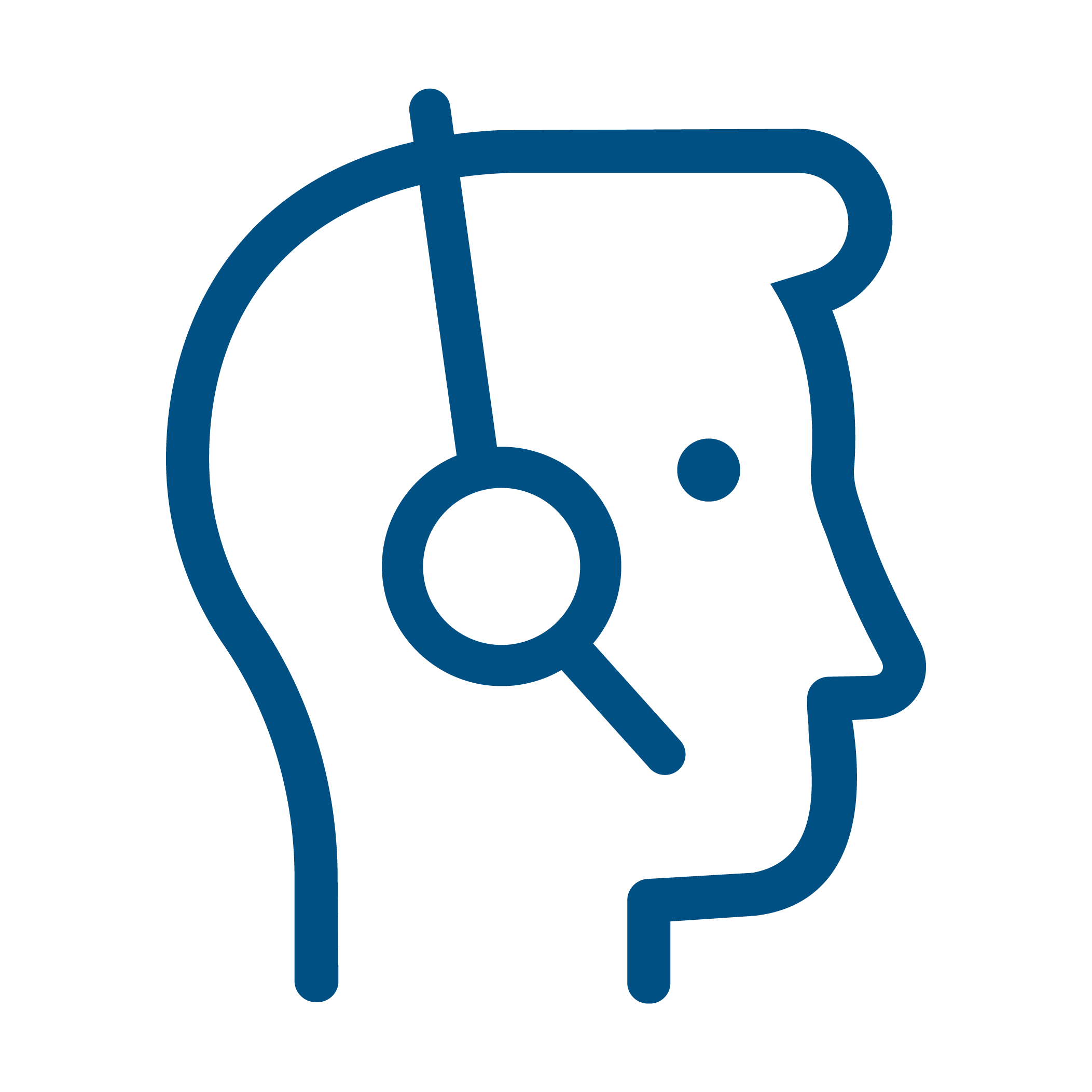
- Audio and video communication via smartphone, tablet or smart glasses
- Starting and ending service calls
- Call history including shared files and chats
- Service inquiries
Your added value
- Reduce costs
- Quick response time
- Immediate support 24/7 from any location
Your contact person
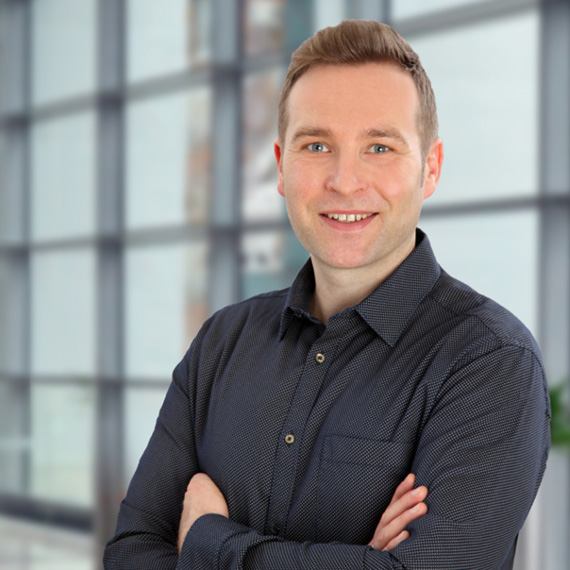