Your easy machine integration and secure data transmission thanks to industrial interface standards
Reliable data interfaces such as OPC UA, REST and TCP/IP play a decisive role in today's production landscape. As a producer or machine manufacturer, using these interfaces is the key to seamless integration into the IT/OT system landscape or to a secure connection to the cloud. Choosing the right software for interface integration is therefore a decisive factor for your application. You need to be able to rely on high scalability, first-class support and regular updates for secure operation over the long term.
Diverse challenges
Modern manufacturing industries have seen data interfaces become an essential part of the smooth exchange of data for automating, monitoring and optimizing production processes. Integrating them offers numerous benefits, while they also present challenges:
Machine and system interfaces can be extremely complex, particularly when it comes to integrating different systems with different functions, protocols and data formats into one production scenario. It requires a deep understanding of how the corresponding interface protocols work and the machine manufacturer's specification of the data structures within the machine interface to ensure seamless data exchange.
Machine and system interfaces must be reliable to avoid faults and failures. It is important to define clear specifications for data structures, error handling, and buffering to ensure that communication is error-free and fail-safe.
Software for interface integration must be scalable in order to meet the performance and flexibility requirements of the production in the future. With larger production lines, the integration software must be able to handle increasing data loads and enable the parallelization of data connections.
Security is a major challenge when specifying machine and system interfaces. Secure data interface types must be used to protect the confidentiality, integrity and availability of the data transmitted and to prevent unauthorized access or manipulation.
FabEagle®Connect: The integration solution for interface protocols
The FabEagle®Connect low-code interface integration software offers you easy and reliable integration of a wide range of data interfaces.
OPC UA
OPC UA (Open Platform Communications Unified Architecture) is a widely used standard for secure and reliable communication in industry. It relies on a service-oriented architecture and a well-structured information model. Due to its increasing distribution and versatile application, OPC UA is regarded as the most future-proof interface and is therefore part of the standard for FabEagle®Connect.
MQTT
MQTT (Message Queuing Telemetry Transport) is a protocol that is optimized for the loss-free transmission of messages in distributed IoT systems. By buffering data, it minimizes losses due to connection interruptions, making it particularly suitable for networks with low bandwidth, such as those found in mobile networks. This is achieved using a client/broker architecture, in which the client subscribes to the broker's topics. In the event of a connection failure, the broker buffers the data until the client can be reached again.
REST client
Representational State Transfer (REST) is a further development of the HTTP object model and was developed specifically for distributed web services. The client-server architecture is combined with various features to focus on the uniformity of the interfaces. The HTTP user layer makes REST compatible with almost all online services and web clients.
Databases
A database interface enables communication between applications and a database. The integration solution connects to the database, sends SQL statements for queries, inserts, updates, or deletions, and receives results in the form of datasets.
TCP/IP
TCP/IP is one of the most well-known network protocols that forms the basis for many application protocols and more complex interfaces. TCP/IP shapes the reference model by dividing it into functional layers (application, transport, Internet and network access layer).
Modbus
Modbus is a bus system that enables communication between client and servers. As a common industry standard, Modbus is often used by PLCs and automation technology.
ActiveMQ
MQ in ActiveMQ stands for Message Queue and converts synchronous communication into asynchronous communication. ActiveMQ is a free message broker and was developed by the Apache Software Foundation. Asynchronous communication offers a high potential for optimization in the transmission of data and supports various clients (REST, AMQP, MQTT).
Our experts support you during your integration projects
With the increasing use of protocols for machine connection such as OPC UA, which is a versatile but complex standard, the range of different options is increasing for companies to implement integration tasks themselves to connect machines and systems and to provide interfaces. In addition to the classic mechanisms that have existed for reading and writing since OPC DA, for example, there are now numerous UA companion specifications available for specific industries and applications.
In addition to a basic understanding of the interface protocol, questions regarding IT infrastructure and data architecture are also relevant. All of these requirements can make it difficult to introduce new solutions during operation or integrate them into existing software. That is why, in addition to the FabEagle®Connect low-code interface integration software, we also support you with experienced teams with expert knowledge in the areas of interface integration and data architecture for your integration projects. This allows you to focus on your core business while we take care of the technical integration for you.
Testing and coordinating in the ACM process
The SECS/GEM standard used in the semiconductor industry is extremely precise, and also highly complex. The high requirements of the industry have also brought about the ACM (Automation Capabilities Management) process, which ensures that new equipment meets the specified data interface requirements. In this area, we support machine manufacturers and factory operators in testing and coordinating the ACM process as well as in the technical implementation of the SECS/GEM interfaces.
Work steps in the ACM process:
- Preparing a project specification to integrate the equipment interface
- Preparations for carrying out the test, including creating test documentation
- Implementing equipment integration with FabEagle®Connect
- Carrying out the integration test on site at the factory
- Performing extensive tracking and stability tests in production
Workshop to define integration layer architecture
In addition to the use of interface standards, there are various strategies for data and integration architecture. As soon as a project consists of more than a single machine that has to be connected to the IT system, the architecture of an integration level needs to be planned. The following questions have to be clarified:
- Number of data sources: How many data sources are to be connected using an integration solution?
- Choice of platform: On which platform should the integration solution be installed, e.g. IoT box or server VM?
- Scalability: How does the integration solution handle adding more data sources and sinks?
- Data transfer: Which data is transferred and with which mechanism (e.g. push/pull, sending during update, fixed cycle)?
- Data structure: How is the interface and the data to be transferred structured (e.g. table or tree)?
- Interface protocol: Which interface protocol meets the specified requirements?
During the workshop, our experts are available to discuss and answer these questions and any other queries relating to the definition of an integration level. If requested, we can support you from the specification of requirements through to implementation using our FabEagle®Connect integration software. That is how we ensure that your integration projects are implemented efficiently to meet your specifications.
Your contact person
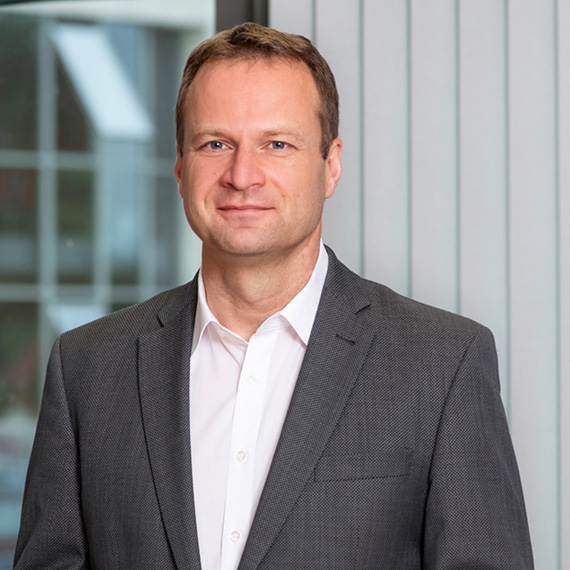