The reliable line controller for process control and traceability on production lines and cluster
Highly complex semiconductor backend processes require the optimization of the process steps leading up to the completion of the final component. A powerful line controller as a process control system is essential here. It reliably controls processes from loaders to separation and bonding to packaging. That is how the process-specific line controller enables efficient process control and also offers MES functionalities such as data acquisition and recipe management. These functions can be flexibly scaled to production lines and production clusters. Ultimately, this helps users and quality managers to create optimized production conditions.
Diverse challenges in backend process control
Process control in backend production presents companies with a number of challenges. Complex production requires specialized know-how, reliable IT solutions and precise coordination to ensure a smooth and consistent process. Facing international competition and high quality requirements, it is crucial to optimize costs and overcome the following challenges:
- Machine suppliers must meet complex interface standards such as SECS/GEM and GEM300. Their implementation requires a great deal of expertise and a suitable integration solution.
- The ACM (Automation Capabilities Management) process ensures that new systems meet the requirements for a standardized data interface. This includes the specification and testing of the data interface together with the machine supplier. Ideally, the interface test is carried out by independent IT experts before the system is delivered to the customer to ensure rapid commissioning. Monitoring the ACM process reduces complexity for the machine manufacturer and enables the factory operator to handle it efficiently.
- For a high level of reliability, solutions are required that minimize risks such as hardware failure. Functions such as warm standby and archiving play an important role in securing valuable data.
- Carrier handling and tracking depend on the perfect interplay of the PLC and line controller. Precisely defined processes for data exchange and process control enable reliable and high-performance implementation of loading and unloading processes.
Efficient process control with the FabEagle®LC line controller
From specification to integration, loader handling, production management, process control and data acquisition to test control, our FabEagle®LC line controller supports you in controlling backend production systems. This enables you to achieve the highest quality standards and reliably control complex processes.
The key to successful project implementation is the individual specification and documentation of the requirements. Our experienced teams can handle complex specification phases and are closely acquainted with industry-specific documentation procedures. As an integrator, we also coordinate the efficient matching and implementation of data interfaces with machine suppliers for you.
An important part of the specification phase is preparing for the integration and implementation of data interfaces. In particular, the implementation of interface standards such as SECS/GEM (E5, E30, E37, PV2) and OPC UA as well as the transfer of parameters and control mechanisms needs to be taken into consideration. This also includes the definition of state models such as the port state model or the upload and download of wafer maps and recipes. To ensure secure integration, we carry out ACM tests for existing machines before the data connections are finally implemented.
As part of production management, line controllers offer a wide range of functions:
- Order management: Create and manage production orders and connect ERP systems for automated production control
- Recipe management: Specify process and test parameters from a central system as well as parts lists (bill of material, BoM) for supply materials to all equipment
- Job management: Define the sequence of work steps and automatic execution of rework plans in the event of a malfunction
- Carrier Management: Map and track carriers and their current location, states and content
- Reporting: Automatically calculate and visualize KPIs and production line statistics
- Materials management: Register, approve and track materials and tools
The line controller is the central system in which all data and production requests from PLC systems converge, similar to a process-specific MES. It controls the process flow based on specifications from work plans, recipes and parts lists. Data from carrier movements, process data and feedback from APC (Advanced Process Control) and SPC (Statistical Process Control) systems flow into process control during production.
FabEagle®LC supports the following process steps:
- Wafer separation and die picking
- Packaging (assembly, bolting, gluing)
- Die-bonding and wire-bonding
- Solder bumping (flip chip installation)
- Molding (compression molding, transfer molding, injection molding)
- Curing oven
- Wafer handling
- Welding (ultrasonic welding, laser welding)
- Labeling and (laser) marking
The line controller in the semiconductor backend process receives all the necessary specifications for the process parameters from the recipe management. This allows test results to be automatically compared with the specified values. In the event of deviations, errors are automatically documented and, if configured, a rework plan is also initiated. Typical testing stations include chip testers, x-ray inspection, and final testing.
FabEagle®LC supports the following process steps:
- Electrical testing (static, dynamic, hot test, cold test)
- Optical testing
- X-ray inspection
- Mask test and wobble circle test
Your contact person
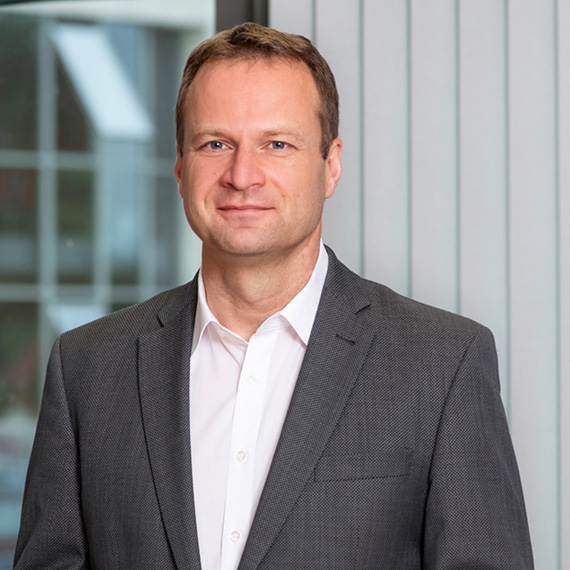