Digital system monitoring and management with cloud-based customer portal
Kontron AIS GmbH has developed a software platform based on ToolCommander® to control three different newly developed wafer handling robots (WHR) from Adenso Industrial Services GmbH. This was seen as an opportunity to establish digital system monitoring and management: the cloud-based customer platform Adenso.ToolCloud, based on the digital transformation solution EquipmentCloud®, was implemented. This software is based on an Oracle Cloud Infrastructure.
Kontron AIS was responsible for the introduction, project execution via the OpenIssues module, as well as for service and support by the local development team.
“EquipmentCloud® helps us not only to be regarded as a progressive company and to be sought after by customers and business partners for our experience, but we can also free our valuable capacities from the burden of routine tasks.” Uwe Beier, Managing Director, Adenso GmbH
- Data integration of almost 70 identical systems
- Data maintenance of specific parameters
- Introduction of EquipmentCloud®
- Setting up and maintenance of an online library for the systems
- Establishing a project-related data exchange server
- Central communication platform
- Increased evaluation accuracy
- Saves up to 30 % in time and costs during commissioning
- Improved communication with customers and project partners
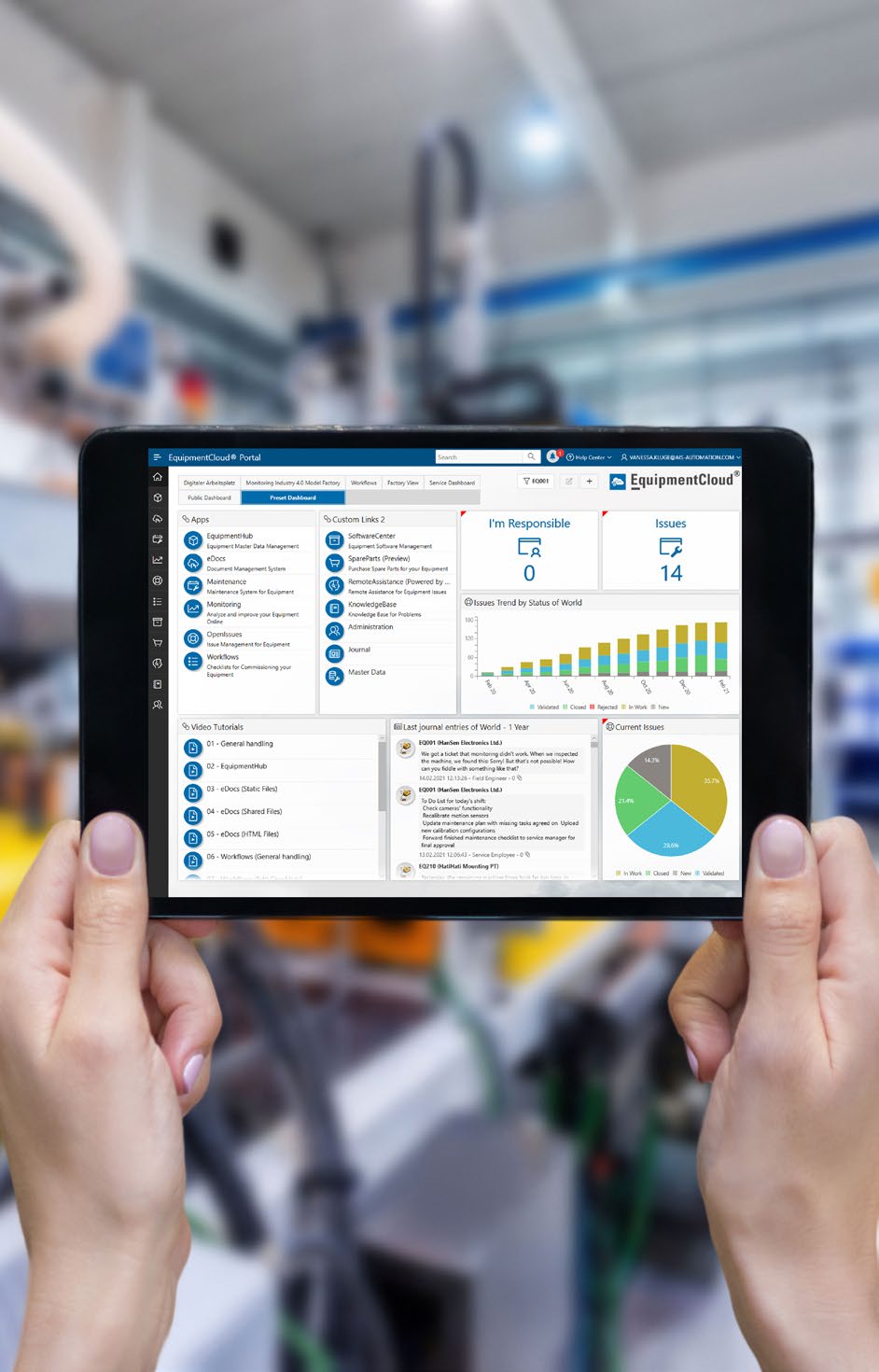
Goals
Adenso has a broad portfolio of roll-to-roll (R2R), ultra-thin glass (UTG), wafer handling robots (WHR) and automation systems for special machine construction and the semiconductor industry, as well as specialised employees with know-how in these areas. The Adenso.ToolCloud is used to set up and maintain an online library for software and hardware configuration and for digital documentation of the systems. In addition, the focus is on the monitoring and evaluation of performance-relevant system parameters such as reliability, error frequency and capacity utilisation.
The Adenso.ToolCloud serves as a data exchange server from the start of the project to the final acceptance of the systems and enables current software revisions, to-do lists, work statuses and necessary documents to be viewed, downloaded and updated at any time. A positive side effect is accelerated project execution. With the introduction of a modern cloud solution, Adenso is not only expanding its digital service package but also enabling a central and direct communication platform for all project participants in order to strengthen long term customer loyalty.
Solution
The EquipmentCloud® from Kontron AIS is used to achieve the specified goals. This transformation solution enables the documentation, management and evaluation of relevant system data from a cluster/implanter, sorter and WHR through the freely selectable modules. The eDocs module is used for the documentation. Entire folder structures or individual manuals, CAD drawings and data sheets can be stored there and assigned to the respective systems. Installed software versions and sets can be managed via integrated SoftwareCenter so that, with a single click, the user can determine the available software version and whether an update is required for the systems in the field.
Adenso and its end customers can always keep an eye on important key figures, process values, alarms and events relating to the systems with the help of the monitoring module. If deviations occur, traceability and troubleshooting is simplified considerably due to consistent logging. Experience has shown that this results in accelerated project execution and guaranteed success together with the OpenIssues module, in which open issues are documented, categorised and prioritised, responsibilities assigned and deadlines set.
Benefits and results
After an 8-hour introductory workshop by Kontron AIS, Adenso was able to independently create around 70 systems and gradually maintain the Adenso.ToolCloud with relevant data. Thanks to the continuous and constructive feedback sessions with the EquipmentCloud® development team, data integration and data maintenance could be considerably simplified using the copy function and freely configurable master data parameters.
Access to process parameters has especially improved the accuracy of evaluation and acceptance in the commissioning process for the end customer. The bundling of all relevant information in one location ensured direct communication and the inclusion of all project partners – customers, suppliers and employees.
Openness and transparency about processes and open tasks have had a positive influence on the course of the project, as time and cost savings of approx. 30 % were achieved.
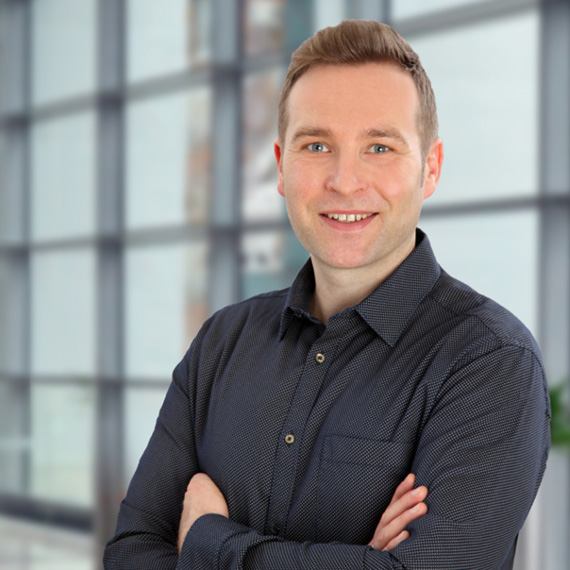