Proactive service with customer-specific mobile app
For more than 25 years, InnoLas Solutions has been providing customer-specific laser systems for micro material processing for high-precision applications in the electrical engineering, photovoltaic and semiconductor industries. InnoLas Solutions has spent years consistently investing in a modular digital portfolio in addition to their established business model and to expand customer experience and digital after-sales.
A modern and easily configurable connectivity solution is just as important as global digital customer service. As part of this digital service portfolio, mobile app-assisted proactive machine service is to be brought to market. A futureproof solution with intuitive operation on mobile devices together with holistic integration and industry expertise were decisive in the selection of the product and cooperation partner.
By delivering proactive machine service in the InnoLas Solutions customer app, Kontron AIS has created a customer-specific mobile app that allows InnoLas Solutions to interact with customers 24/7 and provide data-based service.
„With the mobile customer app, we are moving closer to our customers and digitalizing service and after-sales at the same time.” Niels Krauch, CTO, InnoLas Solutions GmbH
- Customer-specific app design and development of the EquipmentCloud®mobile on a functional basis
- Proactive service concept
- Seamless customer service desk integration
- Digital machine service as a mobile app for Android and iOS
- Push notifications
- JIRA interface for service tickets
- 24/7 customer support app
- Reduced machine downtime
- Faster response times by the service team
- Increased machine productivity (> 5 %)
Provide proactive service and support end-customer digitalization
For InnoLas Solutions, both the motivation and challenge were to take the development of their own after-sales service to the next level, significantly speeding up and proactively aligning the previous reactive customer interaction via telephone, contact form and email. Service requests are to be better channeled internally and the necessary information on all machines delivered to customers is to be made centrally accessible to the entire service team anytime and from anywhere. The extended service is to enable customers to digitalize their own processes, and make internal communication and work processes as barrier-free as possible without high initial costs.
To implement proactive machine service, InnoLas Solutions chose the digital transformation solution EquipmentCloud®, including the development of a customer-specific native app for Android and iOS from longstanding partner Kontron AIS. Thanks to the already available connectivity of the machines using the SECS/GEM interface-compliant FabLink® integration solution as well as the configurable and low-code solution FabEagle® Connect, which allows manufacturing data to be transferred flexibly via REST without extra programming, it was easy to set up the service concept on an established data interface.
Machine service as extended service directly from the app
When developing the customer app, it was important to InnoLas Solutions to seamlessly integrate the existing customer service desk solution and to make news about the company and products also available via the mobile app in order to enable cross-platform customer contact. Important machine information such as master data, documents, key figures, alarms and throughput are to always be available and up-to-date for technicians setting up the machines, shift managers and project managers. In addition, every new laser system is to be delivered with machine-specific but standardized maintenance schedules in the mobile app in order to make service assignments predictable and replicable.
To implement the customer-specific app, a separate REST API had to be developed, test environments set up in Android and iOS, roll-out procedures defined and an ergonomic user interface created to reflect the InnoLas Solutions corporate design. Brand recognition and loyalty are essential for a continuous customer experience. The customer-specific design was further developed with the help of continuous feedback from InnoLas Solutions and was interactively tested in the showroom with employees as well as customers.
Kontron AIS also implemented the integration of a JIRA interface for interacting with the customer service desk using the mobile app, so that service requests ranging from maintenance to upgrades, and technical support to spare parts deliveries, can be made via the app. Another important milestone was the implementation of configurable push notifications so that app users can be informed early on about upcoming maintenance, the current machine status and any alarms that occur. The final step involved publishing the app in the two most important app stores with detailed content, images and mockups. Routine support, technical updates and the development of further features will continue to be carried out by Kontron AIS.
The app is divided into three main areas: One area for the latest company news from InnoLas Solutions, the second provides access to machine data for carrying out the machine service, and the third accesses the customer service desk. Within the machine service area, the overview page with its individually configurable widgets summarizes key machine information for the operator at a glance.
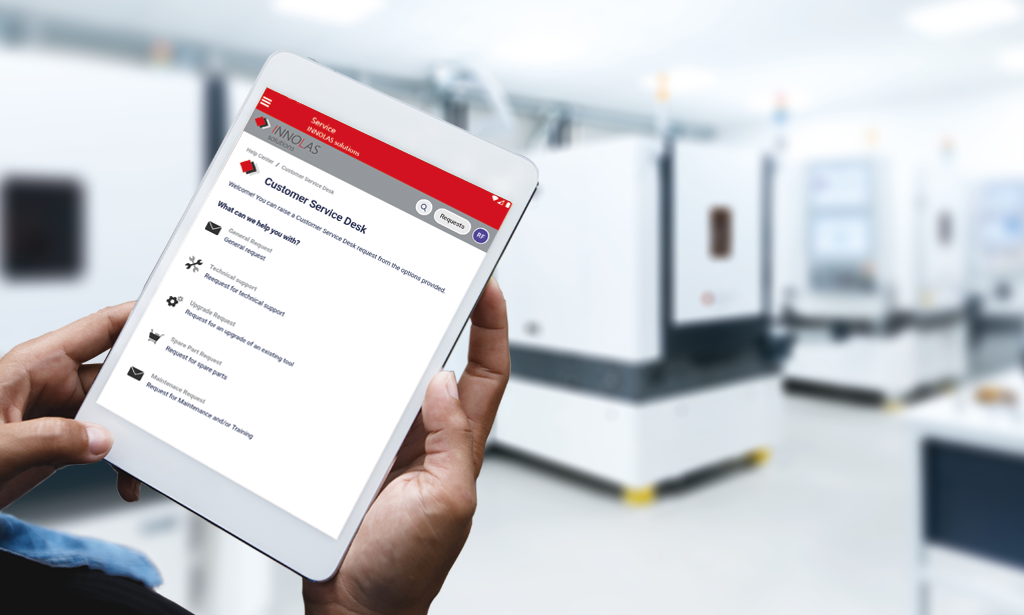
The machine service function enables InnoLas Solutions to manage machine data at different customers using one and the same app. The integrated equipment filter supports the search for machine types and specific machines using product names, an intuitive navigation menu and a QR code scanner.
Machine availability, utilization and productivity are essential for high-cost applications such as the production of solar cells and ceramic substrates, laser depaneling of rigid and flexible circuit boards, the selective removal of thin-film layers on large-format glass or the cutting, structuring and formation of cavities in circuit boards. By monitoring faults, alarm messages and machine status in real time, the InnoLas Solutions service team and the customer can react quickly and prevent prolonged production downtimes. In addition, an overview of the current processing status of tickets and maintenance ensures greater transparency in customer communication and better coordination of responsibilities within the service team.
For Niels Krauch, CTO at InnoLas Solutions, the customer app was created as a sustainable mobile application that speeds up the response time for service cases and significantly improves customer satisfaction by expanding the ways the company can be contacted.
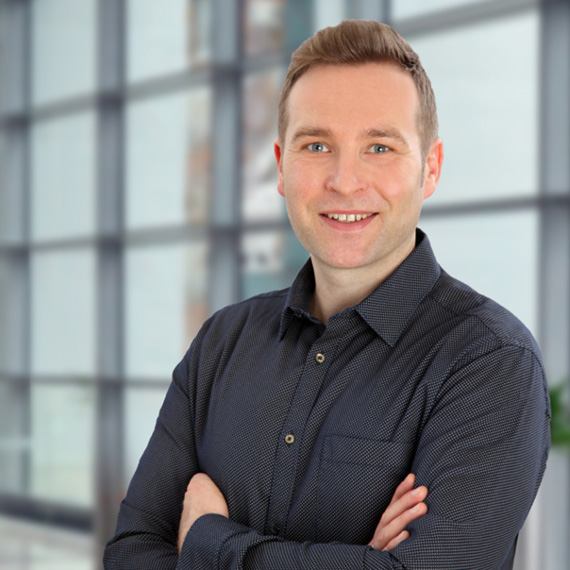