Digitization of the commissioning process for mobile handling systems
Automating material flows and handling processes require solutions that are tailored to the customer‘s processes down to the smallest detail. The transport and handling systems must fit exactly into the entire process. The documentation for these kinds of projects is complex and predestined for loss of information, which makes the commissioning of the systems correspondingly complex.
Fabmatics GmbH, a specialist in automation and robotics of material flows and handling processes in the semiconductor industry, solved these challenges using the Kontron AIS digital transformation solution EquipmentCloud®.
Fabmatics has now been organizing the commissioning of its HERO® Fab mobile systems digitally for several months, increasing process speed by 30 % and creating a central machine database. The autonomous transport robots are used in semiconductor factories around the world.
“Since we started using EquipmentCloud®, we‘ve been able to accelerate the commissioning of our robotic systems by 30 % and set up our services digitally.” Peter Seydel, Department Manager Customer Service, Fabmatics GmbH
- No standardized and up-to-date data structures
- Lengthy commissioning process
- Service technicians need comprehensive specialist knowledge at all times
- Create a complete machine database
- Standardize work processes using digital checklists
- Automate master data upload via integrated interface (API)
- Full transparency into the team‘s work progress
- Reduction of in-house commissioning and final acceptance by 50 %
- Acceleration of the commissioning process by 30 %
Set a framework for automating the process
Fabmatics‘ special solutions require service employees to be equipped with expertise for their work at all times and throughout the entire life cycle of each machine. With standard tools such as e- mail, Microsoft Office and data storage on file servers, they kept on reaching their limits. Consequently, the job instructions and documentation available during service calls were not up to date and it took time to search for the required documents.
Since commissioning is usually carried by teams in rotation, the work progress of the individual teams was difficult to track. This involved timeconsuming coordination and unnecessary additional effort. In addition, overlapping areas of functionality made it difficult to prepare data efficiently due to inconsistent, compulsory and standardized data structures.
The Kontron AIS digital transformation solution EquipmentCloud®, which is based on the Oracle Cloud Infrastructure as software-as-a-service, was implemented to achieve these goals.
Phase 1: Map all the variants
A comprehensive systems file had to be created as the basis for implementation. The first step in this was to map the product portfolio and then organize the master data. The wide range of variants of the HERO® Fab mobile robots required a well thought-out structure. A total of 82 types of equipment could then be organized in a multi-level equipment and type hierarchy. Basic master data and extended master data were sorted and defined according to product-specific categories.
Phase 2: Implement the commissioning process in EquipmentCloud®
Launching EquipmentCloud® meant rethinking the commissioning processes. The Fabmatics service technicians as well as application and development engineers took this task and developed new standardized procedures. The development department provided documentation and instructions for this purpose. The service department was responsible for creating and maintaining work processes and detailed checklists in the Workflows module.
All the necessary tasks including detailed work instructions (e.g. inputting values for calibrating cameras on the mobile robot‘s chassis, uploading log files as well as visual component confirmations) could be stored and simply checked off in the checklists. The additional documentation of skills ensured that each user met the necessary requirements for implementation.
The workflows are modular and presented as a task board. This means that the processing of tasks can be interrupted at any time and resumed later on. Following the implementation phase, the workflows for commissioning new mobile robots were tested in practice by senior service technicians and the existing Excel lists were replaced step by step.
One year after the launch, Fabmatics manages the commissioning of the HERO® Fab product group to 100 % using the workflow checklists in the EquipmentCloud ® and can ensure end-to-end tracking and historical reporting using the software.
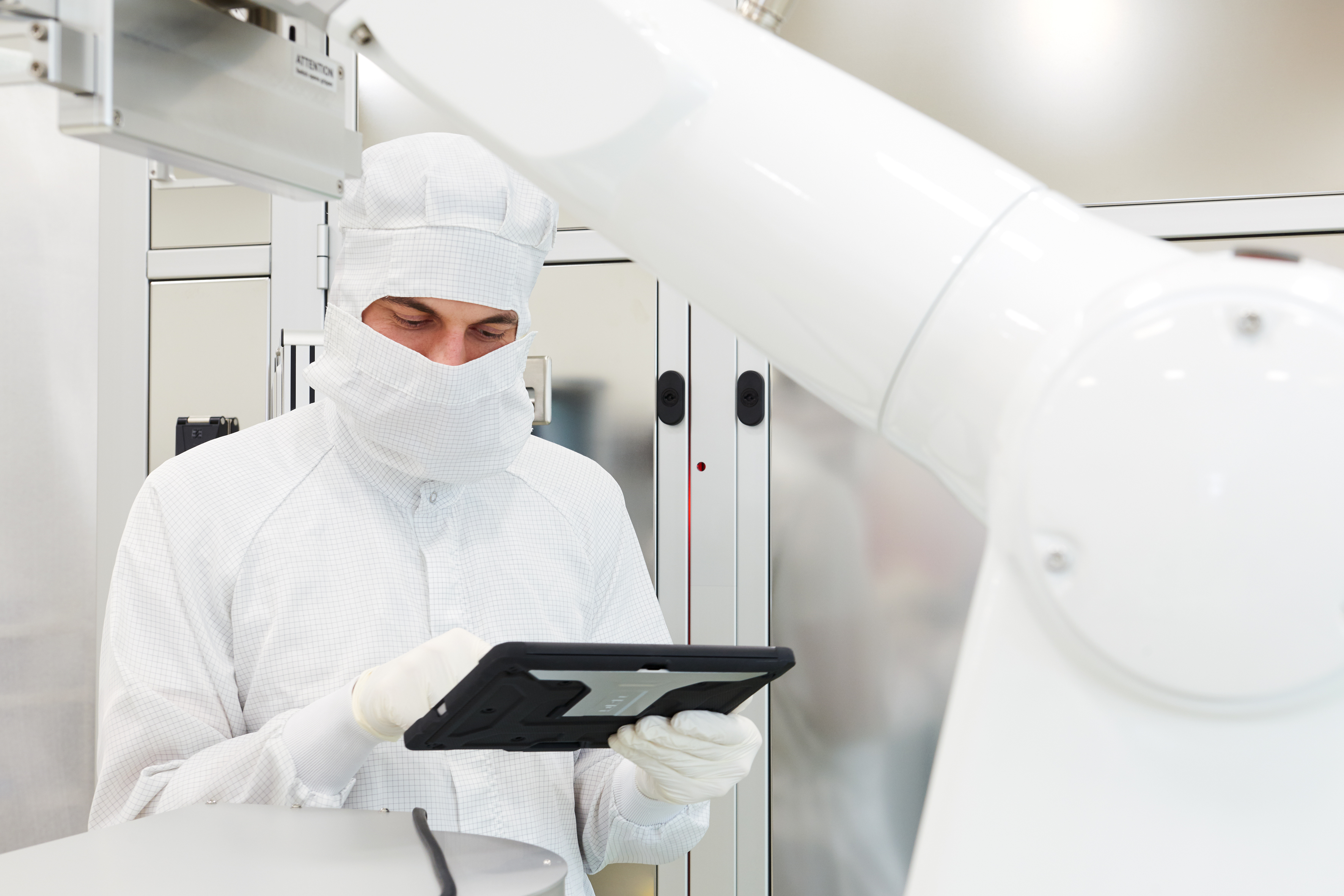
Higher commissioning efficiency during factory acceptance test (FAT)
Since the launch of EquipmentCloud® at Fabmatics, two major successes have been achieved: Commissioning costs have been reduced by 50 % and processing speed has been increased by 30 %. This has been achieved primarily due to the documentation of commissioning and the development of a comprehensive plant history, which makes it easier to process service cases.
The development of functioning use cases and processes resulted in a high level of acceptance and commitment from colleagues in different departments. The complete transparency of processes and the efficiency gained through automation create trust among customers and motivate them to drive digitization forward.
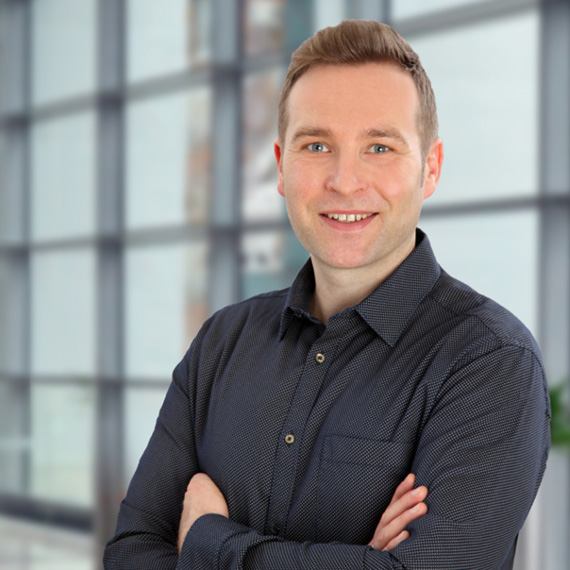