FabEagle®LC is the scalable line controller for your production control with full traceability. Whether for individual machines or a fully connected production line, our line controller is flexible enough to adapt to your specific needs, giving you full control over your production processes in production and a competitive edge.
Like an MES (Manufacturing Execution System), the line controller provides all the essential features for production control: data collection, process control and visualization. At the same time, you benefit from the line controller’s high adaptability and short project timelines when implementing your production control system. This makes your production more transparent and efficient.
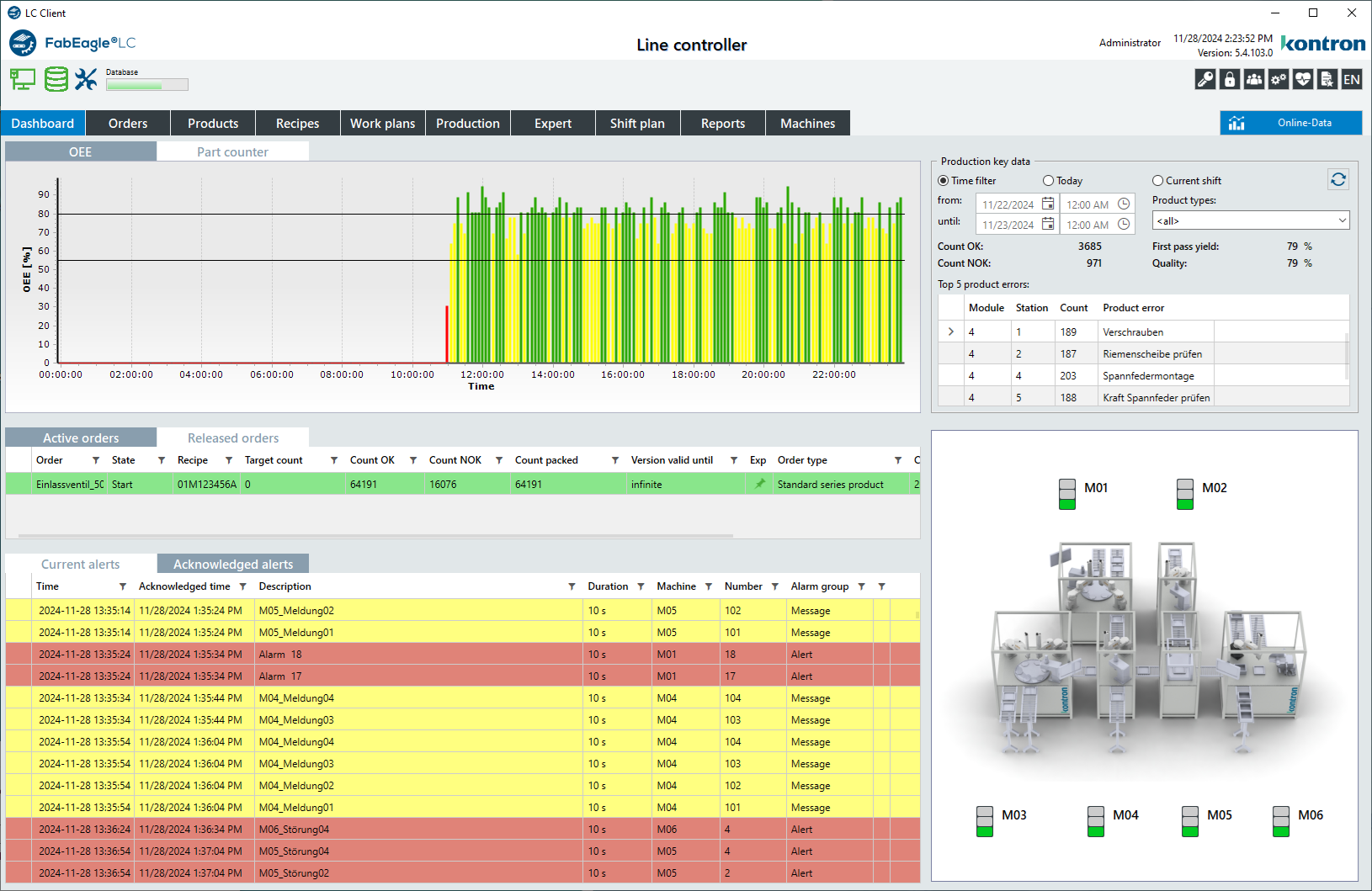
Line controller FabEagle®LC – Your benefits
- Software-controlled workflows ensure secure and stable processes
- Digital recipes, bill of materials and orders simplify production processes and ensure on-time delivery
- Automatic specification of recipe and machine parameters saves time for process management
- Central transport control increases production efficiency
- Reporting and analysis features improve quality management
- Visualization of alarms and trends reduces reaction times for maintenance
- Automatic documentation and data acquisition simplifies work tasks
- Machine monitoring helps identify and minimize bottlenecks and downtimes early on
- Comprehensive recording of material batch and product data provides valuable insights into the impact of each process step on manufacturing and product parameters
- Automatic data archiving serves as a quality proof for manufactured products
- Seamless material batch traceability minimizes production risks and increases product safety
The perfect line controller to control your production
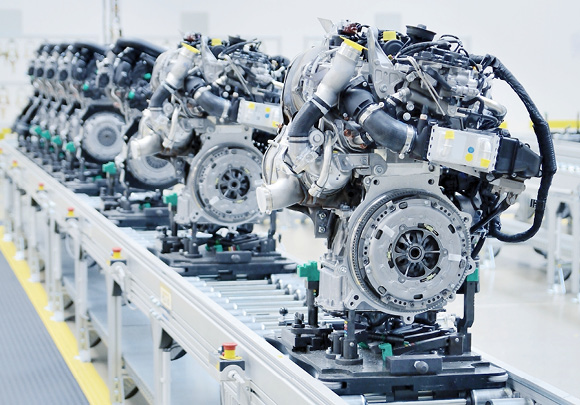
With the FabEagle®LC line controller, you can efficiently control your production line, avoid bottlenecks or delays in production. This ensures smooth integration of all processes and components in automotive manufacturing. Process-driven production control enables you to optimize material flows and simplify production processes to ensure that your deadlines are met.
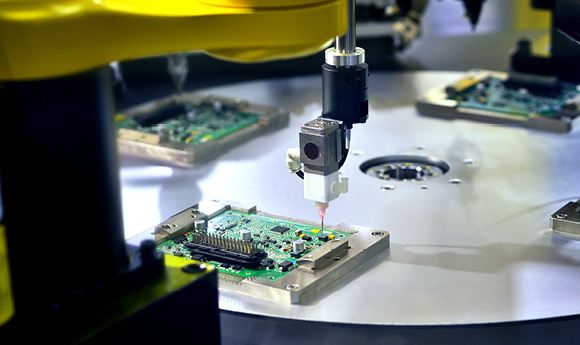
In electronics assembly, short cycle times and high product variety are standard. The FabEagle®LC line controller provides process-oriented control of your lines and workflows, giving you the transparency you need for efficient production. You can track and analyze production data in real time. This eliminates bottlenecks, optimizes equipment utilization, and ensures smooth throughput of each product variant.
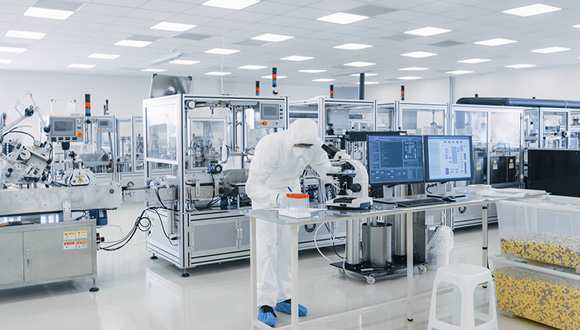
Quality assurance and traceability are top priorities in pharmaceutical and medical technology production. With the FabEagle®LC line controller, you ensure GMP-compliant production control and management. You get complete batch tracking, and automatic data archiving serves as proof of the quality of your manufactured products in accordance with regulatory requirements.
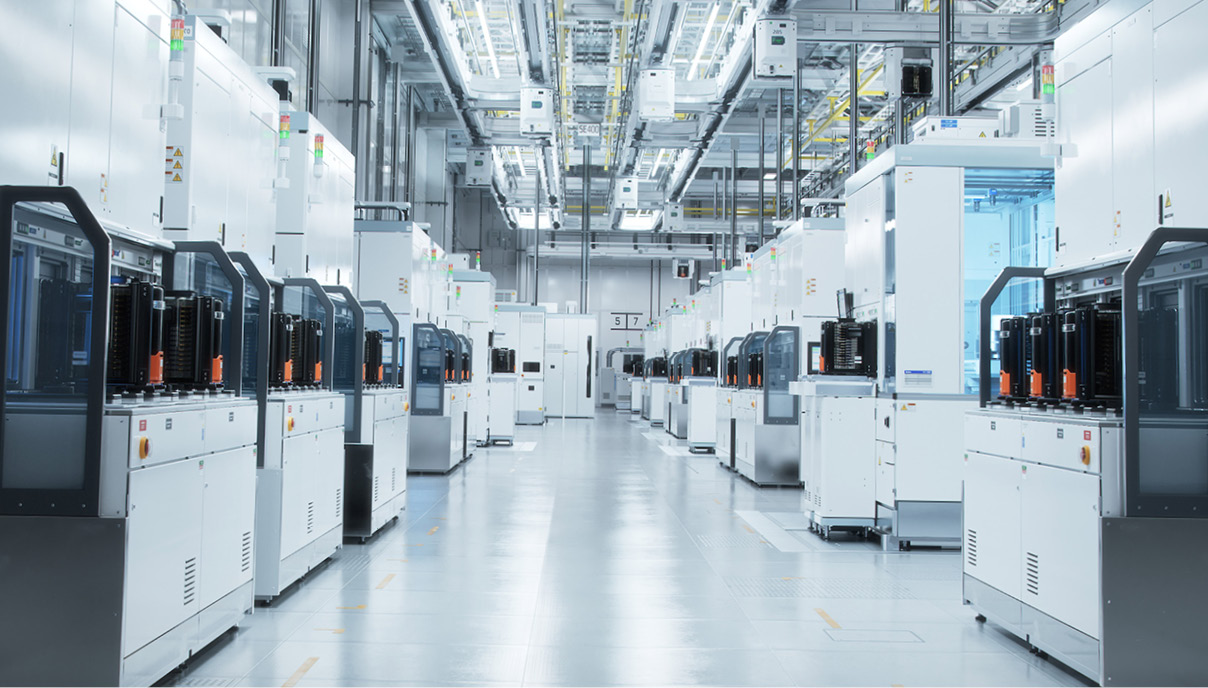
Precision and efficiency are essential in the highly complex semiconductor backend. The FabEagle®LC line controller provides production control of all back-end processes for production lines and cluster systems – from loading and separation to bonding and packaging. This gives you full control over all process steps and creates optimal production conditions for the highest quality.
Overview of the feature range of the line controller for production control
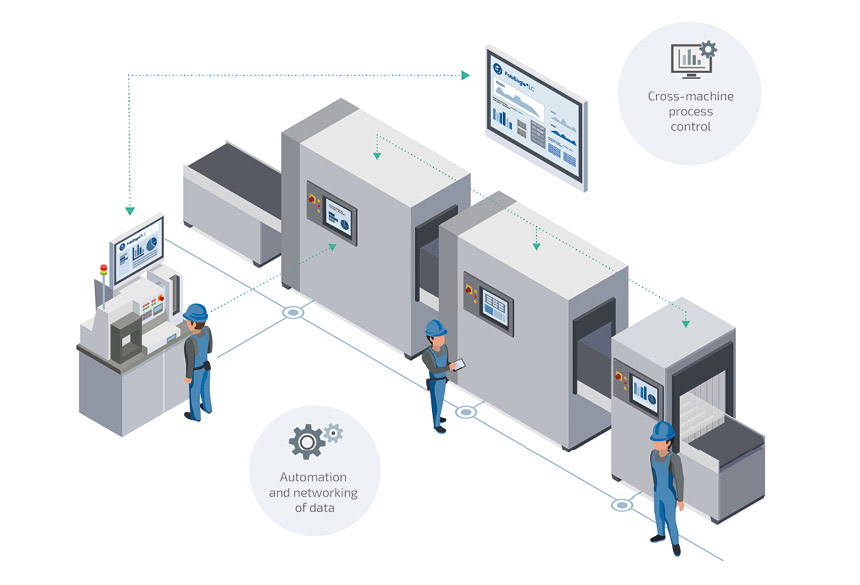
Your contact for scalable line controller
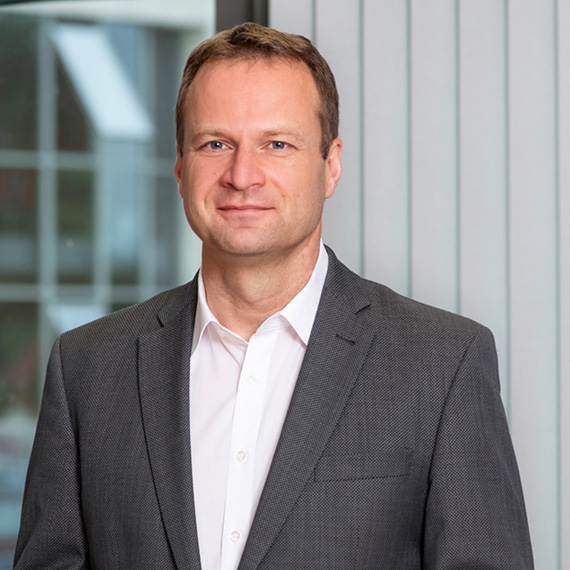
You may also be interested in
FabEagle®Connect
The low-code integration software for standardized interfaces in production
FabEagle®Monitoring
Factory-wide shop floor management for more transparency in production
Blogbeitrag LC vs. MES
David or Goliath? What is the difference between the introduction of a line controller and a factory-wide MES?
FabEagle®LC line controller FAQs
A line controller is a central software solution that controls and monitors individual machines or an entire production line in real time. As the link between the machine PLC and the higher-level IT system, it ensures efficient, transparent and traceable production. Terms such as control system, manufacturing execution system, process control system or production control system are often used interchangeably.
All relevant machine data and the process values of sensors and actuators are collected in a line controller. This real-time data is used to actively control production processes and to clearly visualize all processes. This allows bottlenecks or errors to be detected at an early stage and acted upon immediately.
Line controller are particularly useful in industries with high demands on quality and process reliability, such as the automotive, electronics, semiconductor and pharmaceutical industries. They also support reliable compliance with regulatory requirements, for example through seamless traceability using track & trace.
A line controller controls and monitors individual machines or a connected production line. An MES, on the other hand, controls and monitors a company's entire production across all production units and processes. In principle, both software solutions offer similar core functions. The difference lies in the focus: a line controller operates close to the production section, while an MES takes an enterprise-wide perspective.
If you want to digitalize, monitor and optimize a specific production line, a line controller is a particularly fast and flexible solution. On the other hand, if you are looking for comprehensive transparency and control over all production processes – including cross-departmental planning and KPI analysis – an MES like FabEagle®MES is the right choice.
In large, complex manufacturing facilities, line controller and the MES complement each other perfectly. The line controller provides accurate, real-time data from the individual production units, while the MES uses this data for higher-level management tasks and materials management.
To learn more about the differences and benefits in terms of scalability, flexibility, implementation time, and operational complexity, read our technical article: Smaller, faster, lighter: How line controllers compete with MES solutions.
A line controller performs many tasks to ensure that your production is efficient, stable, and transparent. These include
- Managing production specifications, work schedules, orders, and recipes
- Line and process visualization
- Worker guidance, reporting and alarm statistics
- Complete material and product traceability
- Real-time machine and process data acquisition
- Product data archiving
Specifically, a line controller acts as a central hub that continuously collects data from machines, sensors and actuators. This process data is captured and provides the data source for identifying production metrics and bottlenecks. It also visualizes key figures and production statistics in a clear and understandable way, so that you can always keep an eye on the current status of your manufacturing.
Another important task is complete traceability, also known as track & trace. The line controller documents and records all production steps and material movements. This data is then available for batch reports, quality control and audits. This feature is especially important in highly regulated industries such as automotive, electronics, semiconductors, and pharmaceuticals to ensure that high quality standards are met.
A line controller ensures that your production processes and product data are always documented and traceable. By recording all relevant information in real time – from machine status and process parameters to material movements – it enables reliable and seamless track & trace in your production.
Each product and component is given a unique identifier, which the line controller uses to log the entire production process. This includes information about when and on which machine the product was processed, what materials were used, and what process parameters were applied. This data is stored centrally and can be archived if required.
By using this detailed information, you can quickly identify the cause of quality problems, limit scrap, and organize targeted recalls if needed. You also benefit from the high level of transparency and traceability of your processes during audits.
In industries such as automotive, electronics, semiconductors, and pharmaceuticals, where quality control and compliance are critical, a line controller gives you the peace of mind that comes with regulatory compliance and maximum control over your production processes.
A line controller brings transparency, control, and efficiency to production. It helps you with process-oriented production control, reliable traceability of material and product data, and real-time data acquisition for comprehensive reporting. The result: fewer errors, better quality, and more stable production.
- Ensure quality: By continuously recording and monitoring all process and machine data, all specifications are precisely met and documented.
- Eliminate production errors: The line controller monitors process values and immediately reports deviations from recipe specifications. This reduces scrap and prevents entire batches from being produced incorrectly or recalled.
- Implement track and trace: Every production step, material and component is fully documented. This means you always know what was produced, when, where and how – an important basis for audits and regulatory requirements.
- Reduce production costs: With complete transparency into machine status, material batches and production data, you can analyze and optimize processes. As a result, you can reduce downtime, increase efficiency, and sustainably lower your production costs.
A line controller is flexibly and individually adapted to the existing interface landscape of IT systems and machines. Standard industrial protocols and machine interfaces such as OPC UA, MQTT, TCP/IP, and SECS/GEM are supported, as well as connections to databases, higher-level ERP or MES solutions, and process-specific traceability systems such as barcode and QR code readers.
FAQs about production control with the FabEagle®LC line controller
Production control encompasses all activities to plan, monitor, and control production processes in real time – from the first insert of materials to the finished product. The goal is to make production efficient, on time, and of high quality.
In practice, this means that orders are planned, machines and equipment are controlled according to recipe specifications, materials are requested as needed, and process parameters are monitored according to the recipes. The result is a stable process that can respond flexibly to disruptions, order changes, or recipe modifications.
Modern production control systems rely on software solutions such as line controllers or MES to centrally record and evaluate all relevant data and use it specifically for process control. This shortens throughput times, minimizes downtime, and significantly increases transparency throughout the entire production process.
Production control performs all the operational tasks necessary to make manufacturing processes efficient, on time, and of consistent quality. It ensures that all elements of a production system work together optimally, for example, by processing the right order at the right time with the right recipe parameters – with as little disruption and much transparency as possible. Key tasks include:
- Order management
- Recipe management
- User management
- Shift plan definition
- Line control
- Line and process visualization
- Alarm statistics and reporting
- Worker guidance
- Material tracking
- Machine and process data collection
- Archiving
A line controller can help by automating, visualizing and controlling these tasks in real time.
Production planning calculates the optimal processing of production orders, taking into account setup times, tool availability, system configuration and utilization. While production planning calculates the ideal processes in advance, production control ensures that they are efficiently executed in practice.
Production planning: Determines what will be produced, when and where. It considers factors such as capacity, material availability, delivery dates, and economic goals. Complex production planning solutions are also referred to as detailed planning.
Production control: Executes production orders according to resource and time schedules. It monitors ongoing processes, compares target and actual data, and responds to variances.
Both solutions work together and are essential for efficient and flexible production, especially when it comes to responding quickly to changes in production or the order situation.
Key production indicators (KPIs) provide a clear, data-driven view of production. They show where production is efficient and where there is room for improvement. Overall equipment effectiveness (OEE), cycle time and yield are particularly important. They not only support monitoring, but also provide the basis for informed decisions and targeted improvements.
- OEE: Overall Equipment Effectiveness combines availability, performance and quality into a single metric. It shows how efficiently equipment is actually operating.
- Cycle time: Indicates how much time elapses between the start of a process step and its completion. Cycle time is very important in the interlinking of production machines and the resulting production flow.
- Yield: Shows the percentage of defect-free products in relation to the total throughput as adjusted throughput. This KPI is a direct indicator of rework.
You can learn more about these three production KPIs and how to calculate them in our blog post: KPIs in manufacturing: Your guide to optimization and increased efficiency.
Efficient production control is key for improving Overall Equipment Effectiveness (OEE). OEE is a very broad metric that is primarily used as a target. When OEE drops, people can take action and look more closely at the causes in the following three factors
- Availability: The production control system immediately records faults and downtime and notifies machine operators. Availability indicates how long machines are available for production.
- Performance: Targeted control of production orders, shifts and resources optimizes the utilization of your equipment. Bottlenecks can be minimized and changeover times reduced, increasing actual output relative to planned output.
- Quality: Integrated inspection mechanisms, worker guidance, and complete traceability help identify and eliminate quality defects early. This reduces the scrap rate and more products leave the line in perfect condition.
A production control based on a line controller provides the necessary data and control intelligence to measurably improve your OEE.
Real-time process and production data collection is automated through interfaces to machines, sensors, actuators, and control systems. The line controller continuously collects this data directly from the production line and makes it available for control, analysis and documentation.
- Machine Data Acquisition (MDA): Machine data such as process values, states, quantities, cycle times and downtimes are automatically collected at the line controller via standardized interfaces such as OPC UA, MQTT or PLC
- Process data acquisition: Capture all quality-relevant parameters such as temperature, pressure or torque. This data is crucial for complete process monitoring and subsequent traceability.
All collected data is immediately available on the line controller for visualization, dashboards, checks or reports – enabling immediate intervention in the event of deviations.