System monitoring for wire bonders, calibration systems and assembly lines
First Sensor Mobility GmbH, a wholly owned subsidiary of First Sensor AG and part of TE Connectivity, specializes in the development and production of innovative sensors for the automotive industry. Real-time analysis of machine availability and product throughput while operating a 24/7 shift system is essential for a trouble-free and efficient production process. Since the machines consist of both wire bonders and automated assembly lines, the level of technology and the type of interfaces available vary depending on the manufacturer and age of the machines. A two-stage flexible interface implemented by Kontron AIS was used to connect the machines to the monitoring module of the EquipmentCloud® digital transformation solution
„By integrating our machines into EquipmentCloud®, we have succeeded in increasing throughput and making machine problems visible.” Martin Schaarschmidt, Manager Manufacturing Engineering, First Sensor AG
- Missing machine park connectivity
- Visualization of machine states in real time
- Connectivity using IoT gateways, Node-Red, and touch panels
- Real-time data acquisition using REST-link
- Factory visualization
- Raise throughput by up to 10%
- Increase machine availability
- Comprehensive analytics and push notifications during 24/7 shifts
Equipment and data integration in the cloud
The first step toward real-time analysis of systems is the generation and bundling of machine data. This requires that the systems have suitable interfaces, which may not be a given depending on the equipment and age of the machine. This was exactly the situation at First Sensor Mobility GmbH. In addition, some interfaces were already being used by other systems or did not provide the required data.
In order to still be able to determine data for evaluating machine availability, throughput and disruptions (duration and frequency), each of the five systems has been fitted with a 10” touch display. The HMI displays were used by the operator to manually record the status of the machine, the disruptions identified and the process values measured. The touch panels are directly connected to the Kontron AIS IoT gateways, which transferred the values to the cloud-based digital transformation solution EquipmentCloud® for final evaluation. The required throughput was recorded via connected machine sensors and also transmitted in bundled form via the IoT gateways. Predefined machine states are set in order to be able to precisely determine downtime and productive time. For example, after a unit has been produced and no new product has been detected by the sensor within the defined downtime, the status of the machine equipment was automatically set to standby in EquipmentCloud®.
The IoT gateways were connected to EquipmentCloud® using Node-Red‘s graphical interface and the monitoring node developed by Kontron AIS. In addition, the employees at First Sensor Mobility GmbH have been trained so that they could independently integrate further calibration systems and assembly lines directly via a REST interface.
How is the system used on a day-to-day basis?
By fully connecting the various machines, First Sensor Mobility GmbH was able to comprehensively evaluate and optimize production processes while operating a 24/7 shift system. In order to give the production manager a quick and clear overview of the current state of production, all connected machines were visualized in a factory overview using SVG files. The current system status is highlighted in color in real time. Details of each machine can be displayed via a tooltip. Colleagues are informed via push notification on their smartphone or by e-mail if there are serious deviations from normal production conditions. Statistical evaluations help to obtain reliable data regarding set-up times, production time and unplanned downtimes across all shifts so it is possible to deduce clues on the optimization potential of production processes.
EquipmentCloud® gave shift supervisors the opportunity for the first time to easily carry out long-term analyses of alarms in terms of frequency and duration across all shifts and, depending on the alarm class, to initiate appropriate measures for the alarms with the highest frequency and/or longest duration. Troubleshooting within the team was significantly accelerated as a result. In addition, production quality could be reliably determined at product level according to good parts (OK) and bad parts (NOK) and the throughput achieved. This significantly optimized cycle times and increased throughput by up to 10%.
What’s more, key performance indicators such as machine availability, overall equipment effectiveness (OEE), yield and process performance for reporting are now provided, which previously could only be determined approximately, and with a great deal of effort.
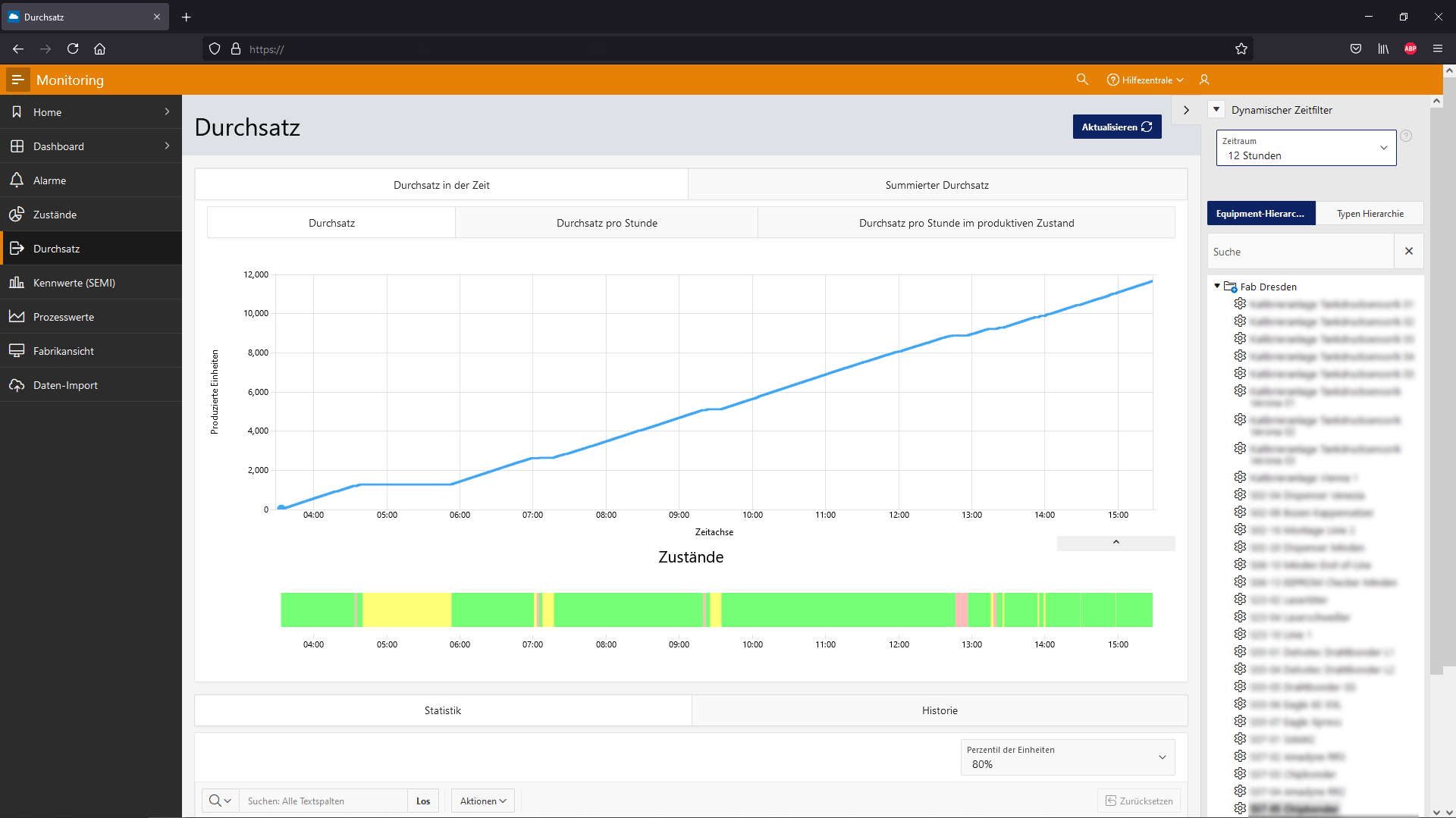
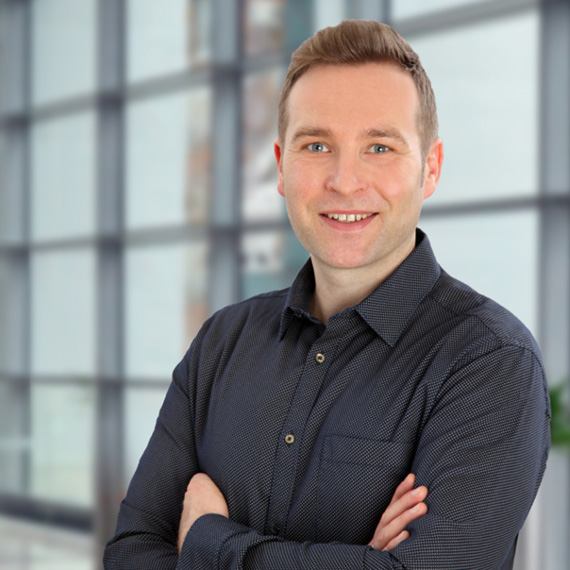