Introduction of a line controller solution connected to ERP and MES
White goods, consumer electronics, personal care products – we are surrounded by consumer goods. Their production involves highly complex manufacturing processes on assembly lines that can include more than one hundred individual process stations. For a line of this scale, an intelligent, reliable control system is essential.
Our customer is a global manufacturer of electronic products in the consumer sector. Two identical lines for the production of electronic personal care products were to be built – one in Germany, the other in China. Following a comparison study of line controllers, our customer chose the scalable Kontron AIS line controller FabEagle®LC.
Two assembly lines were built within 18 months: a pilot line in Germany – consisting of 17 modules, 130 process stations and 46 robots – and a follow-up line in China.
„Our solution is a reliable, proven line controller that can handle the demands of the highly complex production process and the high quality requirements!”
Randy Förster, Expert Software Developer, Kontron AIS GmbH
- Very high number of variants with very fast type change concept and short cycle times
- Buffer management for bridging downtime
- Order processing together with ERP and MES
- Line controller for 17 modules with over 130 process stations
- Track & Trace from the first station to the final inspection
- Interfaces to MES and ERP
- Delivery of a reliable control system suitable for the customer’s system structure
- Development of an expandable, sustainable concept
- Ensuring the punctual start of series production on both projects
High technical requirement vs. tight timetable
The technical requirements were clearly formulated by the customer: a line control system was needed that could meet complex production requirements and be entrusted with series production 24/7. The system should cover the level between ERP/MES and machines – regardless of the choice of machine manufacturer – and be adaptable to specific customer requirements.
The organizational framework were also strictly predefined: both projects are to be coordinated internationally and completed within 18 months from the start of the project to the start of series production in Germany. The almost identical project in China ran in parallel with a team based there and started operation six months later. Thanks to continuous communication, exchange visits and shared development, the Kontron AIS teams were able to ensure knowledge transfer and a uniform solution.
Innovative concept to minimize downtime
The classic functions of a line controller such as order and recipe management, product tracking and recording of machine data were taken as given. The special technical aspect of the project was the requirement to minimize downtimes. That was why the German and Chinese project partners implemented an intelligent buffer concept so that the downstream stations can still be supplied with parts even if one line comes to a standstill. The change between product variants had to take place within the shortest possible time with as few dry runs as possible, including type-relevant consumables. New type variants had to be able to be introduced with minimal configuration effort by the customer.
In the approx. 1,000 m² production area it was essential to use decentralized solutions to alert the operators using online data and to enable mobile inputs. Web-based views are displayed to show status information of the line, current malfunctions or any quality problems. Radio scanners with their own displays are available for the mobile registration of consumables
The result: efficiency, transparency and high machine availability
The line controller systems were successfully commissioned following an intensive concept and development phase. The line controller communicates with the machine control systems, the ERP and the MES, enabling highly automated end-to-end production.
Continuous series production is also ensured by a worldwide 24/7 service contract after the project has been handed over to the Kontron AIS support department.
Advantages for the customer
- Time savings thanks to higher-level order management with automatic transfer, processing and feedback of ERP orders
- Transparency: The online overview of machine status, current work progress and machine utilization shows directly the state of production
- Evaluation: The collected data can be analyzed promptly using web-based tools, to determine the material balance, machine availability or product defect statistics, for example
- High availability: Machine downtimes are temporarily bridged by the buffer concept in conjunction with the line controller.
Your contact person
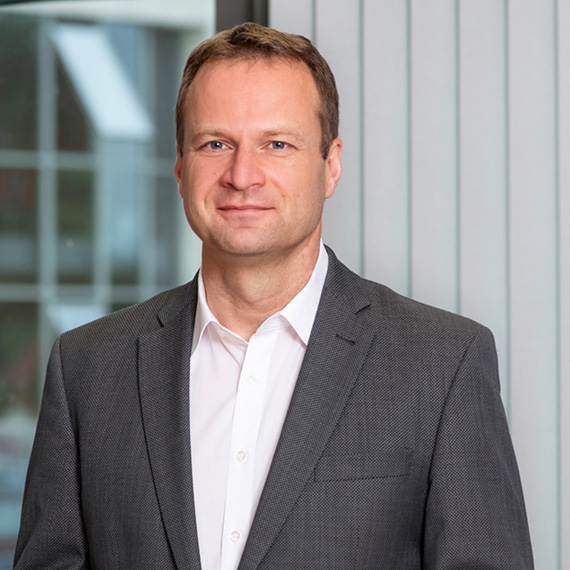