One of the first questions production managers are facing when digitalizing their manufacturing processes, is which control architecture or control system category is best suited to their needs. At the production management level of discrete manufacturing, two concepts in particular are used for production control: line control using individual line controllers or central control of the entire factory or production using a Manufacturing Execution System (MES). Which system production operators should give preference to is like a battle between David and Goliath. But what exactly does the competition look like and who emerges as the possible winner? This blog article helps you to assess the impact of duration, tasks and costs of implementing these systems.
Duration and milestones of launching a production control system
The implementation period, including the delivery time, of a production control system results from individual work packages from specification to commissioning and is different for line controller and MES solutions.
1. Specification stage
The successful introduction of a production control system starts with the preparation of a specification document. This should not only define the requirements for the new control system, but also the concept for the initial focus in terms of data collection and system control. The time required to create the specification depends, among other things, on the size of the department that will be digitalized and ranges from a few weeks for an individual line controller to several months for complete factory control systems. Based on the requirements in
- the specification document,
- the machine specification,
- possible workshop discussions and
- the application of their product standard,
the system supplier develops the specification of the project and the solution. The time required for this depends on the number of departments involved, the machines and the technological complexity (process sequence logic). Since the number of systems with various interfaces and processes to be connected to an MES is many times higher, the specifications, considering all data interfaces and process dependencies, take significantly longer than the specifications for a line controller which focuses on a single production line.
2. Implementation and product enhancement
Depending on how much the MES or the line controller deviates from the specific machine requirements, the software solution is adapted and expanded during this phase. The delivery time is significantly affected by the number of processes, data sources and specific flow logics which need to be implemented. If line controllers have been used before, this phase can be shortened by reusing some of the previous system’s features. Interfaces, process logic and extensions used in running systems that have already been implemented can be used again here.
3. Commissioning
The start-up phase is always a collaboration between different departments and suppliers. The biggest task is to set up and test all data interfaces. This includes interfaces to machine controls, measuring devices and IT systems such as ERP. This requires configuration not only on the control system side, but also on the respective target or source system. The biggest factor in terms of start-up time lies in the number of interfaces to be integrated and cooperation between the software supplier and the responsible machine manufacturer when setting them up and testing them. While a line controller only involves one production area, an MES involves a number of departments during commissioning.
4. Launch and ramp-up
After successful start-up, machine operators and process engineers are required to work with the new system. This means training for all users regarding inputting recipes, parts lists and process parameters. In this respect, ramp-up means not only the test run for the system itself, but also for all operators who have received new work processes with the new system. An MES solution therefore means everything is new for all production participants at the same time, whereas the launch of several line controllers can be carried out in separate stages.
What are the differences in the costs of production control systems
The launch of a production control system is not only time-consuming, but also involves costs. Although these pay off very quickly regardless of the software solution used, there are differences in cost effectiveness between MES and line controller solutions. In both solutions, the items are divided into internal costs through personnel deployment and external costs, such as those of the solution itself.
1. The cost of a line controller
A line controller is particularly characterized by its technical and commercial scaling. If you start with just a part of production, a smaller software solution is required. The calculation across several production lines can be very interesting. The gradual introduction of several line controllers may seem more complex at first glance, but pays off when there is a high repetitive character and improvements can be applied directly to following lines.
2. Costs of an MES solution
The initial costs of an MES solution are significantly higher than those of a line controller, but represent a fundamental change in the way the entire production process works. An MES may not be able to take advantage of repeatability, but it is better able to connect different areas with each other and to control deviations from the classic line design. Internal and external costs are only incurred once, but can be amortized all the more quickly thanks to the newly gained efficiency in production automation.
David versus Goliath – is there a winner?
When introducing a production control system, there are significant differences in terms of duration, tasks and costs. While an MES enables across the board integration of all departments, a line controller solution focuses on individual production lines. It requires careful setup of interfaces and implementation time for adjustments and extensions, and the repetitive nature of the line controller is an advantage. The costs can vary, as can the costs of an MES, which offers efficiency and automation advantages for a value-adding new way of working over the entire production process. The comparison between David and Goliath does indeed apply when it comes to flexibility and speed, but when all aspects are considered there is no clear winner between the MES and line controller. In the end, the duel arena is deciding which system performs better, because both systems aim to do the same thing: enable companies to work faster and more effectively through improved networking and control. No matter which system you choose – the investment in a modern production control system pays off in a very short time and will drive the success of your company forward.
I am here to help you choose the right system for the digitalization of your production.
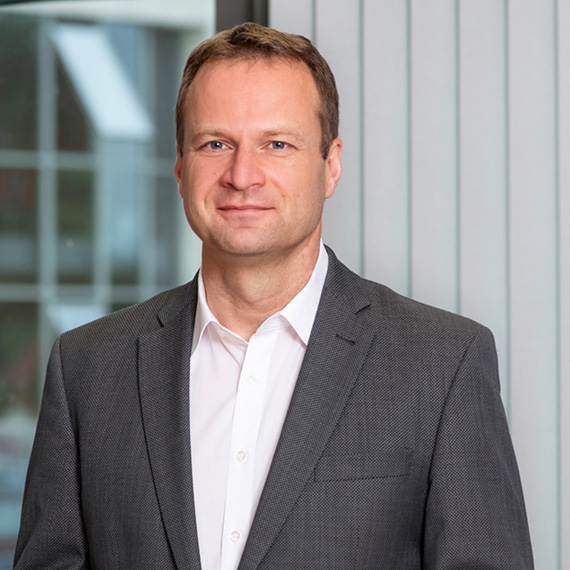