Our Manufacturing Execution System FabEagle®MES, offers high-performance production control and comprehensive data acquisition for the photovoltaic (PV) and battery industries. In these sectors, every percentage of uptime and efficiency matters. With our MES, you improve quality while also reducing costs.
With over 20 years of industry experience, FabEagle®MES is designed to meet your exact needs. Closely aligned with production processes, our solution enables seamless traceability and reliable tracking rates, even in high-volume production. FabEagle®MES allows you to optimally control and monitor your production processes.
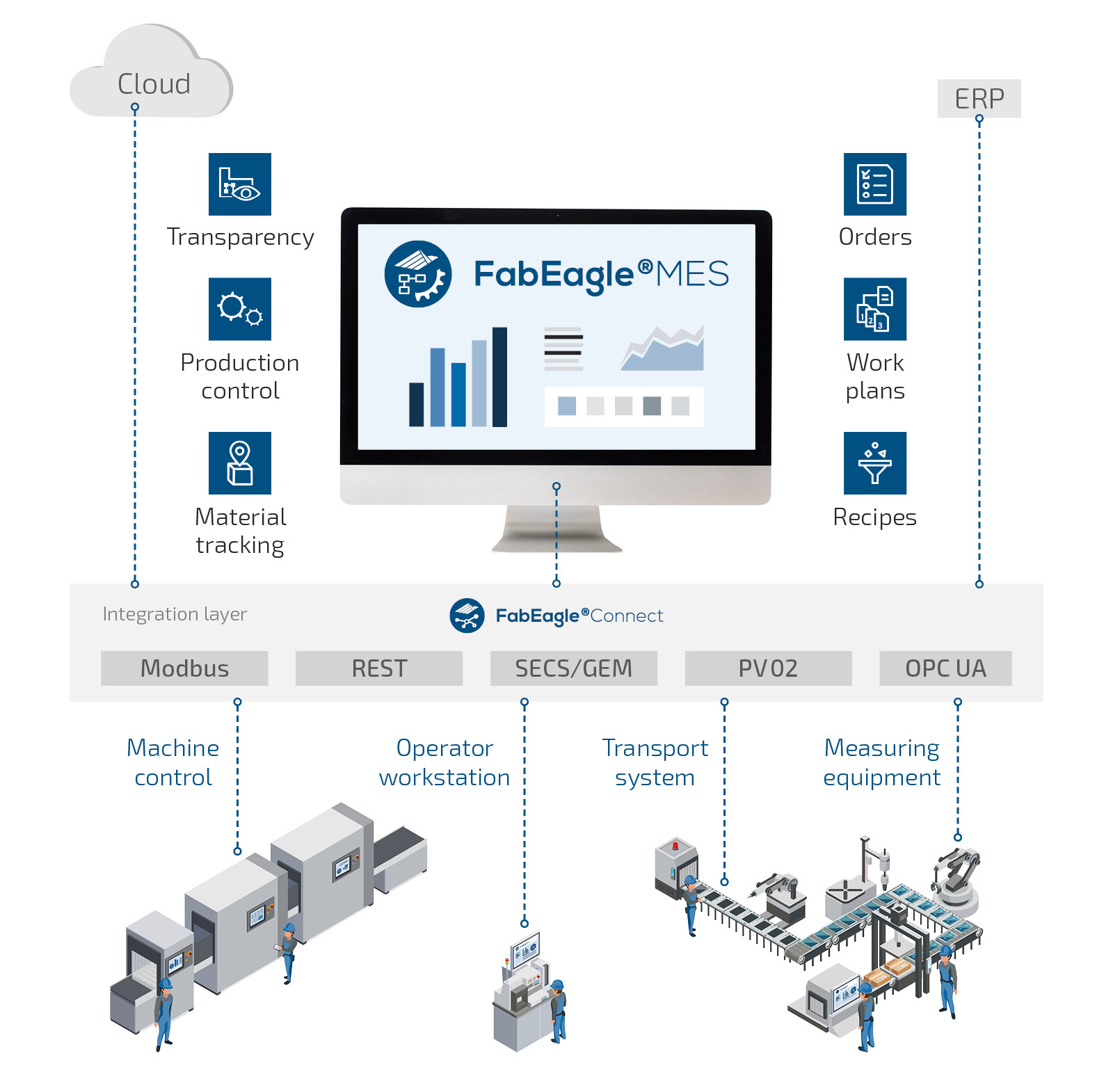
FabEagle®MES – Your benefits
-
- Stable production processes through software-controlled work flows
- Simplified production workflows and high on-time delivery with digital recipes, bill of materials and orders
- Faster production management with automatic recipe and machine parameter settings
- More efficient production processes through centralized transport control
-
- Enhanced quality management with comprehensive reporting and analysis features
- Reduced response times for maintenance with alarm and trend visualization
- Simplified tasks through automatic documentation and data acquisition
- Fewer bottlenecks and downtimes with real-time machine monitoring
-
- Gain insights into the impact of individual process steps on product parameters with full recording of material and product data
- Quality proof for manufactured products via automatic data archiving
- Complete traceability down to individual solar cells thanks to virtual wafer tracking
FabEagle®MES applications in PV and battery production
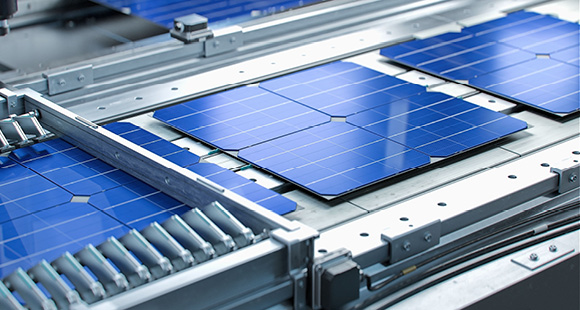
Solar cell production
To monitor and control the production of high-efficiency solar cells, FabEagle®MES offers single-wafer tracking that covers all process steps in photovoltaic cell production. This allows you to maintain an overview and ensure the quality of your solar cells.
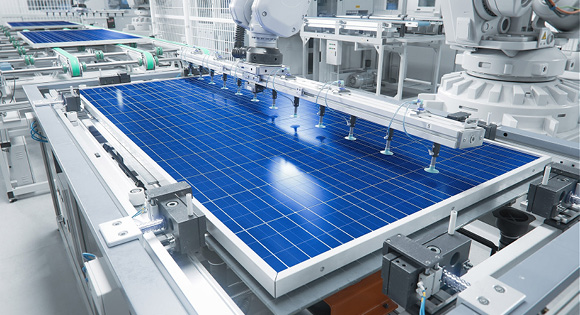
Solar module production
FabEagle®MES supports solar module production with easy-to-use graphical user interfaces. From module inspection and rework to configuring and monitoring automatic palletizing of finished modules, our Manufacturing Execution System optimizes your workflows and increases your production efficiency.
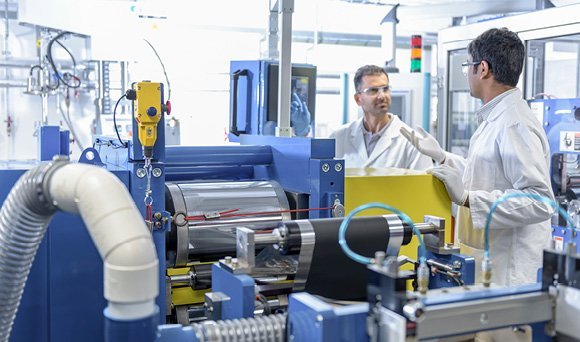
Battery cell manufacturing
The production of battery cells requires the coordination of many different processes and technologies. FabEagle®MES Serves as a central interface between your IT and production departments, facilitating seamless a seamless exchange of information. This means you can be confident that production orders are processed accurately, and production specifications are managed reliably – leaving you free to focus on your core business.
FabEagle®MES – A reliable Manufacturing Execution System for your needs
FabEagle®MES offers a proven and powerful set of features that our experts can customize and extend to meet your individual needs. This flexibility makes our MES a reliable basis for implementing even complex customer-specific requirements. We support multiple data interfaces and implement custom flow logic for process control.
Our team supports you throughout the entire project – from the specification phase to commissioning and ramp-up. Even after that, we are ready to help you: Our maintenance and support services ensure the safe and efficient operation of your MES system. We are your experienced partner for the safe and efficient digitalization of your production.
What makes us different as a partner:
- Close collaboration & direct support: We work closely with your project team from the beginning. During the specification phase, we document your individual requirements in detail and specify the solution. We also clarify the machine interfaces with the machine suppliers. You have direct contact to our team at all times for fast, reliable support when needed.
- Smooth commissioning: Our team is responsible for smooth on-site commissioning, including setting up complex data interfaces to machines and IT systems. After successful testing and individual training of your staff, we will support you in the ramp-up phase if required.
- Long-term support & 24/7 support: Even after the project has been successfully completed, we remain your reliable partner. To ensure the secure and smooth operation of your systems, we offer comprehensive maintenance and support contracts, including 24/7 on-call support.
Production control of individual lines
FabEagle®MES is the comprehensive solution for higher-level production control of all manufacturing processes in a factory – from the control of individual lines, manual workstations and transport systems to individually integrated measurement and process devices. But not every manufacturing environment requires a comprehensive MES. If you are looking for efficient and flexible control of individual production lines, our FabEagle®LC line controller is the right choice.
Your MES contact for production control
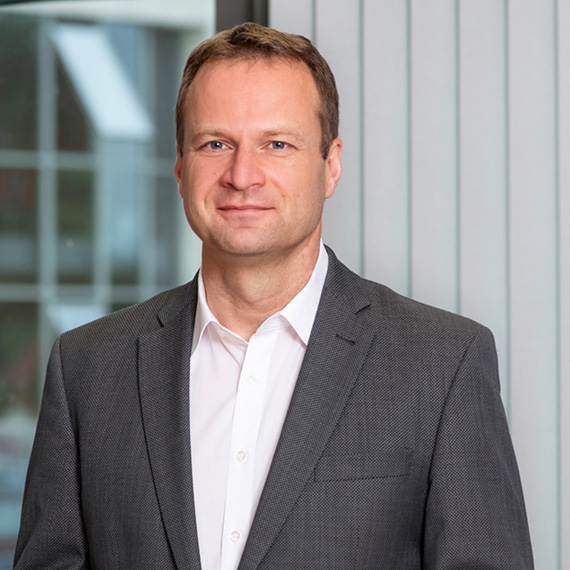
You may also be interested in
-
FabEagle®Connect
The low-code integration software for standardized interfaces in production
-
FabEagle®Monitoring
Factory-wide shop floor management for more transparency in production
-
Blog post LC vs. MES
David or Goliath? What is the difference between the introduction of a line controller and a factory-wide MES?
-
Blog post single wafer tracking
How single wafer tracking optimizes solar cell production