Production control for HJT solar cell factory with single wafer tracking and equipment performance
EcoSolifer and Kontron AIS completed the installation of an MES (Manufacturing Execution System) for heterojunction technology (HJT) solar cell production delivered for an established supplier of turn key PV factories. FabEagle ®MES is used for this factory in Csorna, Hungary with a capacity of 100 MW. It is one of the first HJT production lines to go live within a short time period.
The application includes all functionalities of the standardized FabEagle®MES to provide transparency and control for the production process to secure quality, improve processes and save costs. Most of the relevant information are based on a 100 % integrated shopfloor transferring data on a single material basis.
"Using FabEagle®MES for high-volume PV manufacturing really makes the difference to accomplish ambitious goals in a competitive market.”
Zoltán Ádám, Project Leader, EcoSolifer AG
- Long running ramp-up phase of production
- Continuous on-site upgrades of the equipment for recent process improvements
- Consistent virtual single wafer tracking
- FabEagle®MES with dedicated functionalities for PV
- Long term support of the ramp-up by an experienced project team
- Continuous project management
- Full process control and production visibility
- Complete monitoring of equipment availability, throughput and quality data
- Build-in flexibility for future technology improvements
Roll-out of FabEagle®MES and equipment integration
The FabEagle®MES with single wafer tracking capability is part of the turnkey factory delivered to EcoSolifer. The initial software installation was finished in record time while the integration of the factory equipment was progressing according to the agreed ramp-up schedule.
During the project some challenges were overcome for legacy equipment which needed an upgrade of the interface software to comply with current PV standards. Additionally, technological upgrades and software improvements were installed to adapt to the changes in the production process.
Kontron AIS engineers supported the process with equipment interface tests and provided valuable advice to the equipment vendors. The ongoing support by Kontron AIS combined with the established FabEagle®MES product and an efficient cooperation with EcoSolifer and the equipment vendors ensured the successful completion of the project.
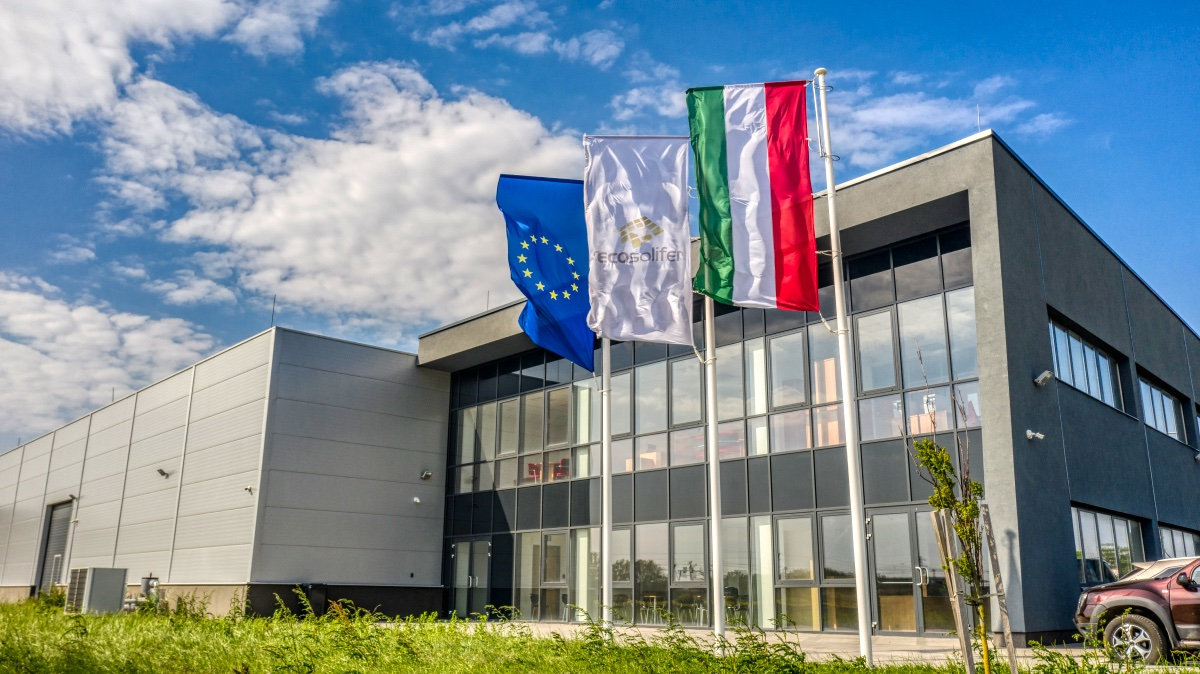
Which functions have been delivered?
FabEagle®MES is controlling production and is collecting material and process related data from the production equipment automatically. A selection of manually acquired data is added to the system on a regular basis. All material is virtually tracked through the production line allowing for data correlations over several process steps and enabling the engineers to recognize process dependencies. Material loss and failure reasons are tracked with sophisticated error reports. Typical defects can be identified and eliminated much faster leading to increased production yield.
With all these features FabEagle®MES grants good process quality and as a result ensures a high product quality. It also supports the engineers in their efforts for further process improvements.
Ready for the future
The factory is already prepared to be extended for an annual capacity of 350 MW. In a first step, production is to be expanded to this capacity, and an expansion to 2 GW capacity is planned for the future. To ensure on-going process stability and further process improvements FabEagle®MES will be a reliable data source providing valuable insights for equipment and process adjustments.
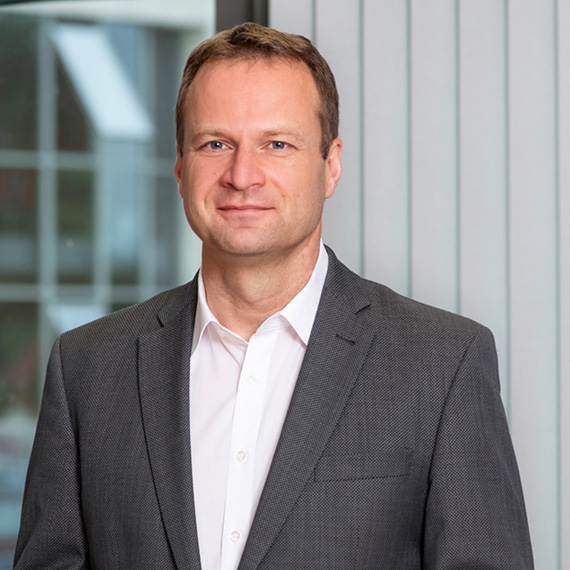