MES for circuit board production
Würth Elektronik GmbH & Co. KG uses FabEagle®MES software for production. The step of applying solder resist in the production of circuit boards was chosen as the pilot project for integrating the MES in which 7 process- and 15 material handling equipment were involved.
In a first step, machine data such as alarms and machine status was visualized. The findings enable Würth Elektronik to identify potential for optimization in production. Later on, KPIs for throughput, process values and material flow were added to the project. Following successful completion of the pilot project, FabEagle®MES was connected to the superordinate ERP level and the production areas throughhole-plating, lamination and mechanical processing were integrated in subsequent project phases.
“FabEagle® gives us a suitable and important stepping stone on the way to Industry 4.0 and thus to greater efficiency.”
Klaus Faller, Digital Office | Processes Würth Elektronik
- Visualize production in the web portal
- Identify and eliminate sources of errors
- Record throughput data
- Status information missing for some machines
- Retrofit missing interfaces by the machine manufacturer
- Insufficient labeling of materials
- Result Presentation and analysis of alarm, status and process data in the web portal
- Principal sources of faults can be identified
- Error frequency reduced by over 50 %
Steps to success
To start the project, only the alarm data collected in a database by the machines was displayed in a web interface. The equipment status could now be deduced from the alarm data gathered and added to the web presentation. The information gained proved extremely useful even at this early stage, which prompted Würth Elektronik to integrate the machines and handling systems via standardized interfaces so that correct status information could be obtained in addition to the alarms in order to trace the material flow and collect material data. All this information is displayed on a dashboard and can be filtered, arranged and combined according to various criteria.
The information shown can now be used to detect common faults and eliminate their causes. This has led to improved equipment availability. Product defects can now be analyzed more effectively and largely avoided in future by means of process improvements.
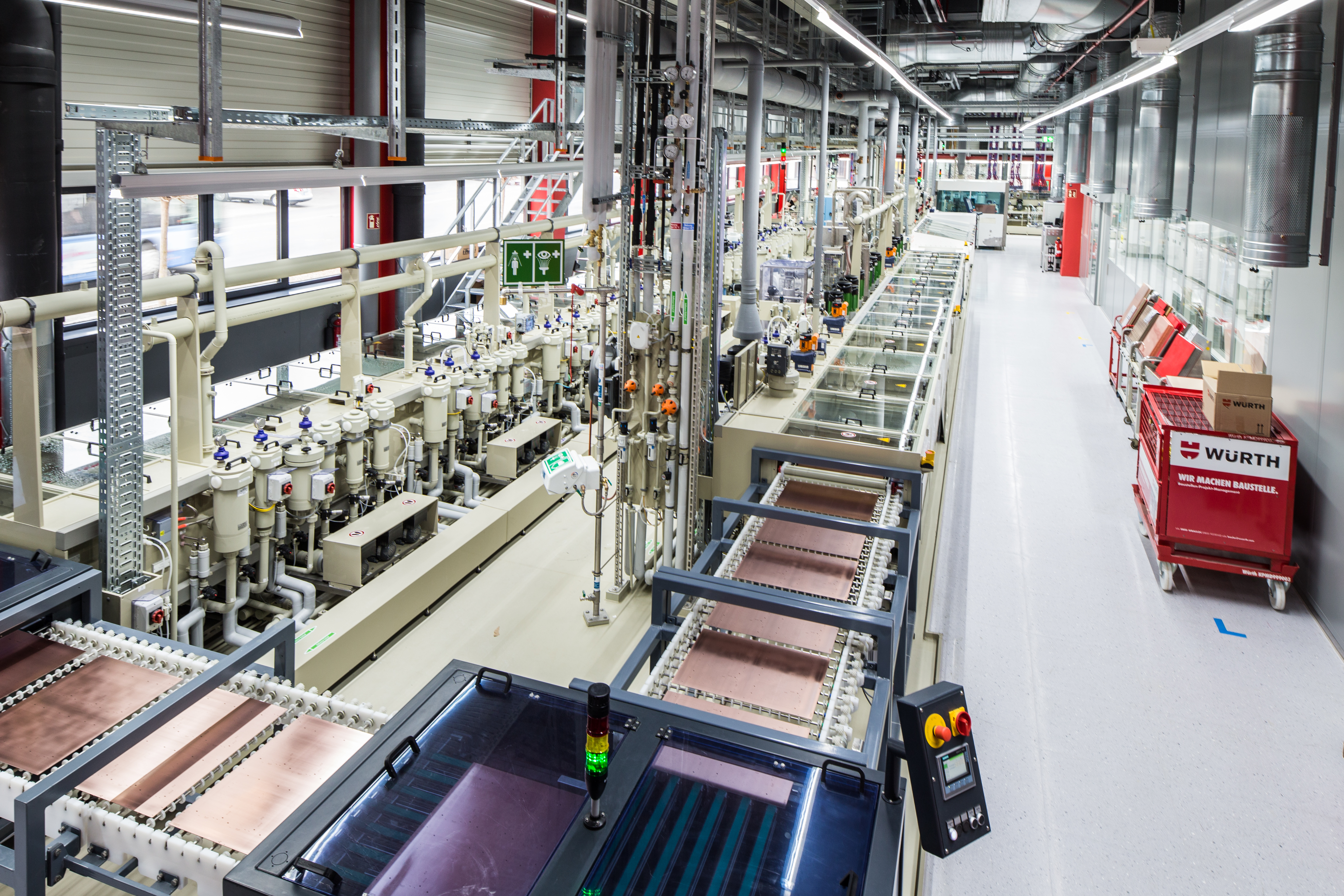
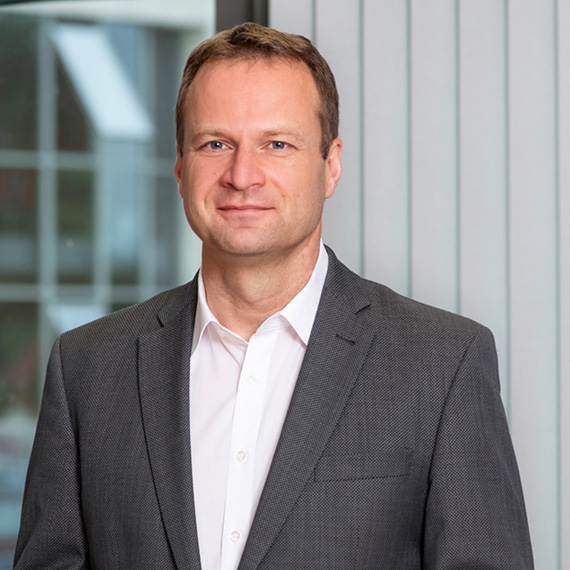