Implementing line controller software for an automated transport system, optimizing PLC programs
“Kontron AIS helped us to achieve our challenging production goals.”
Sebastian Grassow, Plant Manager, Textron Motors
- Replace the existing line controller software
- Optimization of existing S7 PLC programs
- Enhance throughput and support continuous high volume production
- Rollout of the new software for line controller and PLC
- Implementation of a complex iDocs based SAP interface
- 60 % reduction of downtime
- 70 % enhancement of production output
- Reduction of complexity in SAP configuration
Goals
Textron Specialized Vehicles acquired an assembly line for 2-cylinder engines from Weber Motors. The line consists of semi-automated manual work stations with PLC-controlled tools e. g. for screw tighening and oiling. Additionaly, two KUKA robots are handling the engines through several automated assembly and quality control stations. All stations are connected by an automated transport system which is controlled by Kontron AIS line controller software.
Kontron AIS was asked to replace the existing line controller software to make Textron independent from the support of the former line controller supplier, enhance throughput and support a continuous high yield for the production. In addition, the FabEagle®LC line controller was supposed to provide a higher degree of configuration flexibility to make process flow changes easier. An interface to SAP’s ERP system was required to exchange work plans with attached bill of materials (BOMs) and post consumption of parts and output of final products to SAP.
After review of the existing concepts and implementations, it was decided to also rework and enhance the tool automation software to gather more robust communication, faster transport and higher maintainability.
Solution
The introduced line controller FabEagle®LC automatically collects reliable process, performance and material related data online from the production tools without additional work load for the line operators. It provides an easily accessible data archive and management reporting to managers as well as process engineers.
The process flow is fully integrated and controlled by FabEagle®LC. All work steps for automatic and manual workstation are freely configurable. The customer can create complex work steps and help operators with work instruction and animations. Manual process steps are supported to track feeding parts by scanning and manual data input.
Transport planning was previously done by the line controller which resulted in unnecessary communication and unexpected transport behavior. The logic was transferred into the PLCs, the line controller transport logic could be simplified to macro commands. The exchange of single transport section states between PLC and line controller became obsolete. As a result the transport runs now smoothly and reliably.
Production progress messages automatically update SAP with consumed parts and assembled products. This results in a fully automated and vertically integrated production IT environment with full transparency and flexibility.
All FabEagle®LC software features were thoroughly tested in a sophisticated simulation prior to rollout to support a quick changeover and migration with a minimum of production interference and downtime.
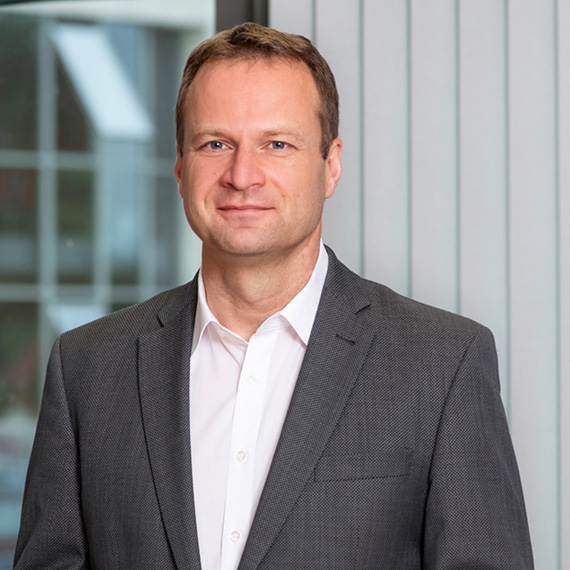