Anlagenmonitoring für Drahtbonder, Kalibrieranlagen und Montagelinien
Die First Sensor Mobility GmbH, eine 100 %ige Tochter der First Sensor AG und Teil von TE Connectivity, hat sich auf die Entwicklung und Produktion von innovativer Sensorik für den Automotive-Bereich spezialisiert. Die Echtzeitanalyse von Maschinenverfügbarkeiten und Produktdurchsätzen im 24/7-Schichtbetrieb sind für einen störungsfreien und effizienten Produktionsprozess unerlässlich. Da der Maschinenpark sowohl aus Drahtbondern als auch automatisierten Montagelinien besteht, variieren Technologie und Schnittstellen je nach Hersteller und Alter der Anlagen. Für die Maschinenanbindung an das Monitoringmodul der Digitalisierungslösung EquipmentCloud® wurde daher eine zweiteilige, aber zugleich flexible Schnittstellenlösung von der Kontron AIS implementiert.
„Durch die Integration unserer Anlagen in die EquipmentCloud® ist es uns gelungen, den Anlagendurchsatz zu erhöhen und die Anlagenprobleme sichtbar zu machen.” Martin Schaarschmidt, Manager Manufacturing Engineering, First Sensor AG
- Fehlende Konnektivität des Maschinenparks
- Visualisierung der Maschinenzustände in Echtzeit
- Anbindung mittels IoT-Gateways, Node-Red und Touch-Panel
- Echtzeitdatenerfassung mittels REST-Kopplung
- Fabrikvisualisierung
- Steigerung des Durchsatzes um bis zu 10 %
- Erhöhung der Anlagenverfügbarkeit
- Umfassende Auswertungen und Push-Notifikationen im 24/7-Schichtbetrieb
Equipment- und Datenintegration in die Cloud
Der erste Schritt in Richtung Echtzeitauswertungen von Anlagen ist die Generierung und Bündelung von Maschinendaten. Dies setzt voraus, dass die Anlagen über entsprechende Schnittstellen verfügen, je nach Ausstattung und Alter der Anlagen ist das nicht zwangsläufig gegeben. Dies war bei der First Sensor Mobility GmbH genau der Fall. Hinzu kam, dass einige Schnittstellen bereits durch andere Systeme genutzt wurden oder nicht die gewünschten Daten lieferten.
Um Daten für die Auswertung von Anlagenverfügbarkeit, Durchsatz und Störungen (Dauer und Häufigkeit) trotzdem ermitteln zu können, wurde jede der fünf Anlagen mit einem 10” Touch-Display ausgerüstet. Die HMI-Displays dienten dem Operator zur manuellen Erfassung des Status der Anlage, der aufgetretenen Störungen und der gemessenen Prozesswerte. Die Touch-Panels sind direkt mit den eingesetzten IoT-Gateways der Kontron AIS verbunden, die die Werte an die cloudbasierte Digitalisierungslösung EquipmentCloud® zur abschließenden Auswertung übertrugen. Der gewünschte Durchsatz wurde über angeschlossene Sensorik der Anlagen erfasst und ebenfalls über die eingesetzten IoT-Gateways gebündelt übermittelt. Um die Stillstandzeiten und Produktivzeiten exakt ermitteln zu können, erfolgt die Festlegung vordefinierter Maschinenzustände. So wurde beispielsweise nach einer produzierten Einheit und einer definierten Stillstandzeit kein neues Produkt vom Sensor erfasst, sondern der Status der Anlage in der EquipmentCloud® automatisch auf Standby gesetzt.
Die angesprochene Kopplung der IoT-Gateways mit der EquipmentCloud® erfolgte mittels grafischer Oberfläche von Node-Red und dem von Kontron AIS entwickelten Monitoring-Knoten. Darüber hinaus wurden die Mitarbeiter* innen der First Sensor Mobility GmbH soweit geschult, dass sie selbstständig weitere Kalibrieranlagen und Montagelinien direkt per REST-Schnittstelle integrieren konnten.
Wie wird das System genutzt und gelebt?
Durch die vollständige Anbindung der verschiedenen Anlagen war es für First Sensor Mobility GmbH möglich, die Produktionsprozesse im 24/7-Schichtbetrieb umfassend auszuwerten und zu optimieren. Um dem Produktionsleiter einen schnellen und anschaulichen Überblick über den aktuellen Zustand der Produktion zu geben, wurden alle gekoppelten Anlagen in einer Fabrikübersicht mittels SVG-Dateien visualisiert. Der aktuelle Anlagenzustand wird dabei farblich in Echtzeit hervorgehoben. Details zur Anlage können per Tooltip angezeigt werden. Bei gravierenden Abweichungen vom Produktionsbetrieb werden Kollegen*innen per Push-Notifikation auf das Smartphone oder per E-Mail informiert. Statistische Auswertungen helfen, über den gesamten Schichtbetrieb hinweg belastbare Daten hinsichtlich Rüstzeiten, Produktionszeit und ungeplanter Stillstände zu erhalten und so Anhaltspunkte für das Optimierungspotential der Produktionsabläufe abzuleiten.
Für Schichtleiter*innen ergab sich durch den Einsatz der EquipmentCloud® erstmals die Gelegenheit, Langzeitanalysen hinsichtlich auftretender Alarme nach Häufigkeit und Dauer über den gesamten Schichtbetrieb mit wenig Aufwand durchzuführen und je nach Alarmklasse passende Maßnahmen für Top-Alarme (hohe Häufigkeit und/ oder lange Dauer) einzuleiten. Die Fehlersuche im Team konnte dadurch deutlich beschleunigt werden. Zudem konnte die Produktionsqualität auf Produktebene nach Gutteilen (IO) und Schlechtteilen (NIO) und der erzielten Durchsätze verlässlich ermittelt werden. Dies optimierte die Taktzeiten deutlich und sorgte für eine Steigerung der Durchsätze um bis zu 10 %.
Darüber hinaus konnten wichtige Kennzahlen wie die Anlagenverfügbarkeit, Gesamtanlageneffektivität (OEE), der Ausschuss (Yield) oder auch die Prozessperformance für das Reporting geliefert werden, die bis dato nur annähernd und mit viel Aufwand ermittelt werden konnten.
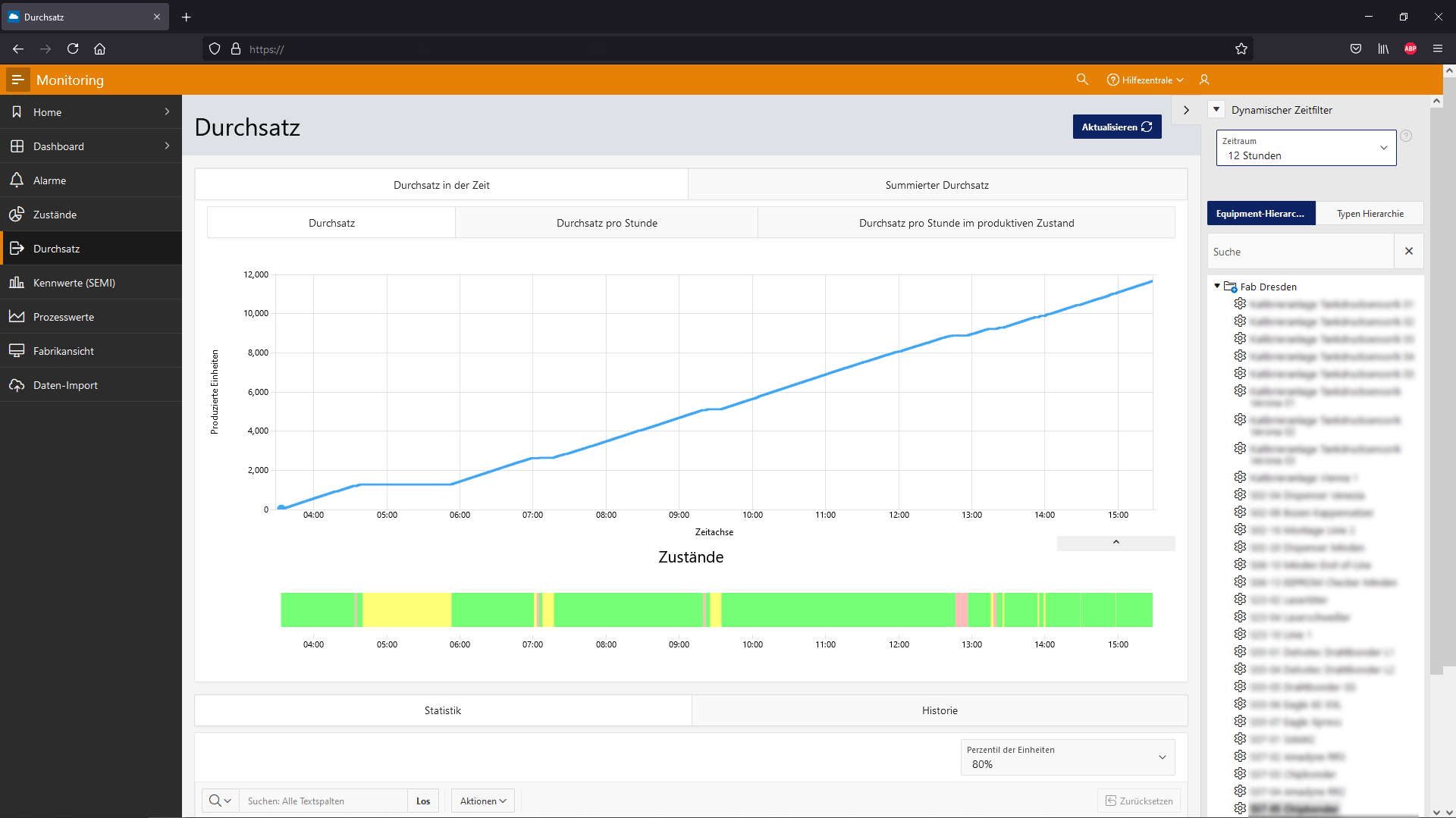
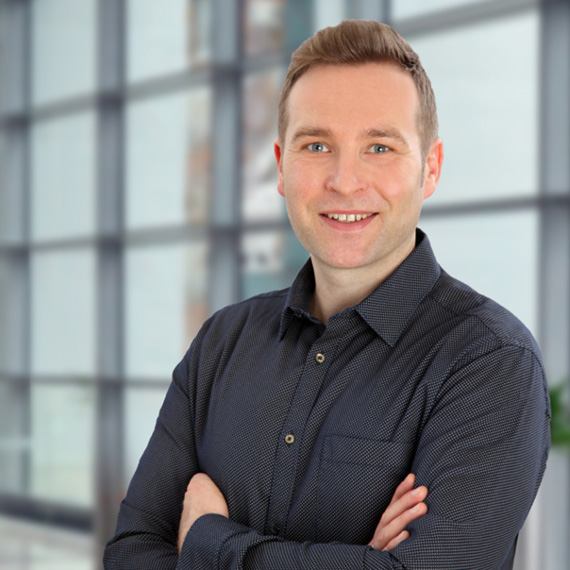