MES für die Leiterplattenproduktion
Die Würth Elektronik GmbH & Co. KG setzt für die Fertigung die Software FabEagle®MES ein. Für die Integration des MES wurde als Pilotprojekt der Prozessschritt zum Auftragen des Lötstopplacks in der Leiterplattenproduktion gewählt, bei dem 7 Prozess- sowie 15 Materialtransportanlagen angebunden wurden.
In einem ersten Schritt wurden zunächst Maschinendaten wie Alarme und Anlagenzustände visualisiert. Mit diesen Ergebnissen ist es Würth Elektronik nun möglich, Optimierungspotenziale innerhalb der Produktion zu identifizieren. Später kamen im Projekt KPIs für Stückzahlen sowie Prozesswerte und Materialfluss hinzu. In den weiteren Phasen nach dem erfolgreichen Abschluss des Pilotprojektes erfolgte die Anbindung von FabEagle®MES an die übergeordnete ERP-Ebene sowie die Integration der Bereiche Durchkontaktierung, Lamination und mechanische Bearbeitung.
„Mit FabEagle® haben wir einen passenden, wichtigen Baustein auf dem Weg zur Industrie 4.0 und damit zu höherer Effizienz.”
Klaus Faller, Digital Office | Prozesse Würth Elektronik
- Visualisieren der Produktion im Webportal
- Identifizieren und Beseitigen von Fehlerquellen
- Erfassen von Stückzahlen und Durchsatz
- Teilweise fehlende Statusinformationen von Anlagen
- Nachrüsten fehlender Schnittstellen durch den Anlagenhersteller
- Fehlende Kennzeichnung der Materialien
- Darstellung und Analyse von Alarm-, Zustands- und Prozessdaten im Webportal
- Hauptstörungsquellen sind identifizierbar
- Fehlerhäufigkeit konnte um über 50 % reduziert werden
Schrittweise zum Erfolg
Zu Beginn des Projektes wurden zunächst nur die von den Anlagen in einer Datenbank gesammelten Alarmdaten in einer Weboberfläche dargestellt. Aus den gesammelten Alarmdaten konnte nun der Anlagenstatus abgeleitet und in der Webdarstellung ergänzt werden. Die daraus gewonnenen Informationen haben sich bereits in diesem frühen Stadium als sehr wertvoll herausgestellt, sodass Würth Elektronik sich entschlossen hat, die Anlagen und Handlingsysteme über standardisierte Schnittstellen einzubinden. Damit sollten nun zusätzlich zu den Alarmen, die korrekten Statusinformationen erhalten werden, um den Materialfluss zu verfolgen und Materialdaten zu sammeln. All diese Informationen werden in einem Dashboard dargstellt und können nach verschiedenen Kriterien gefiltert, sortiert und zusammengefasst werden.
Anhand der dargestellten Informationen können nun häufige Fehler erkannt und deren Ursachen abgestellt werden, was zu einer verbesserten Verfügbarkeit der Anlagen geführt hat. Produktfehler sind nun besser analysierbar und durch Prozessverbesserungen größtenteils zukünftig vermeidbar.
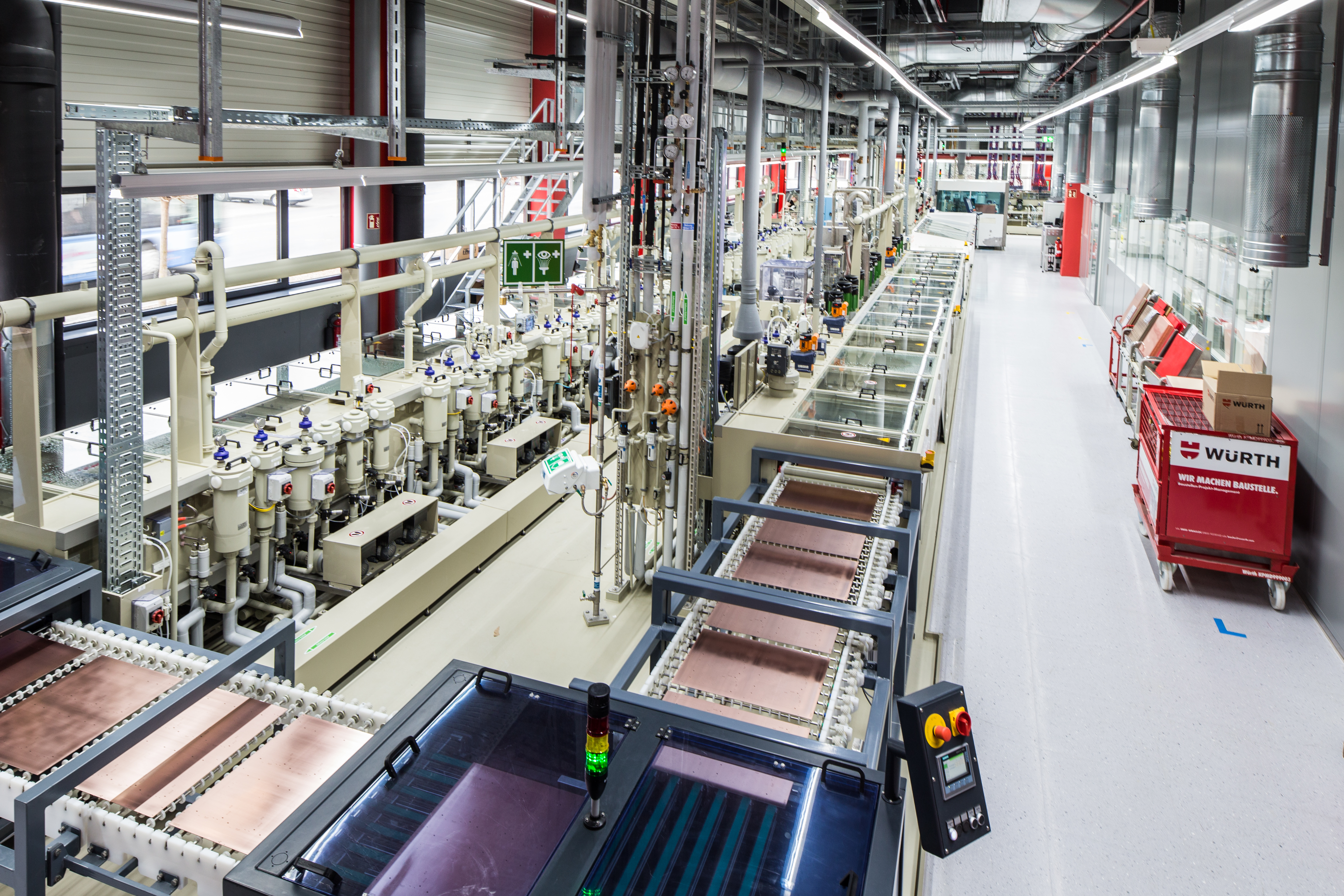
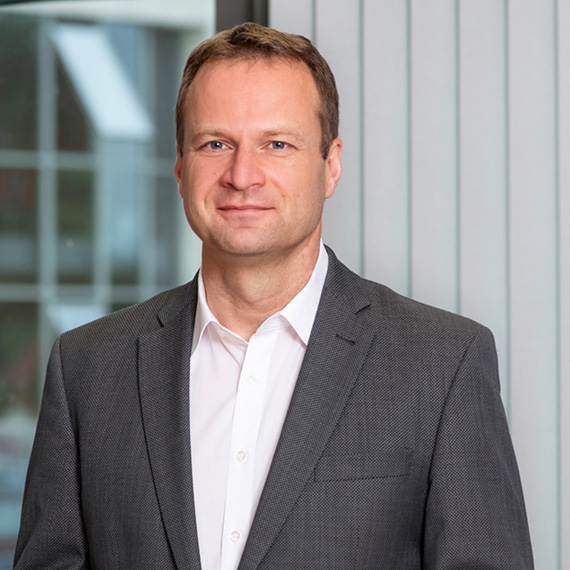