Paperless Manufacturing: FabEagle®LC Line Controller for Pharmaceutical Primary Packaging Production
They are an essential part of everyday medical life: pharmaceutical primary packaging such as syringes, vials and ampoules. The packaging has to fulfill high quality standards and their manufacture is subject to the strict GAMP regulations. At the same time, pharmaceutical manufacturers have to maintain a very high level of documentation, including the recording of batch-related data. The higher the degree of digitization in production, the easier this step is, and the less paper is required.
With this in mind, and with the goal of organizing its production completely without paper, the customer decided to use the robust and customizable FabEagle®LC line controller solution from Kontron AIS. In accordance with GAMP, the pilot line consisting of four large modules with a total of 50 stations, 7 robots and four optical inspections was made ready for fully automated series production. Meantime, there are now four fully automatic production lines at the manufacturer’s site.
“The high level of customer acceptance after four completed lines makes our line controller solution the standard for all future lines and locations.”
Frank Tannhäuser, Senior Sales Manager Factory Automation, Kontron AIS GmbH
- Paperless manufacturing
- Traceability and error analysis
- Increase transparency for downtimes and reasons for downtimes
- Save costs with digitization and automation Challenge
- Clarify all requirements for a fully integrated system
- Project management to support many stakeholders and suppliers
- Qualification and standardization of the interfaces to the line components
- Electronic batch recording in accordance with pharmaceutical requirements
- Digitization of the pre- and post-processing of the batches
- Track and trace from individual product to the packaging unit
- Automated reports for process suppor
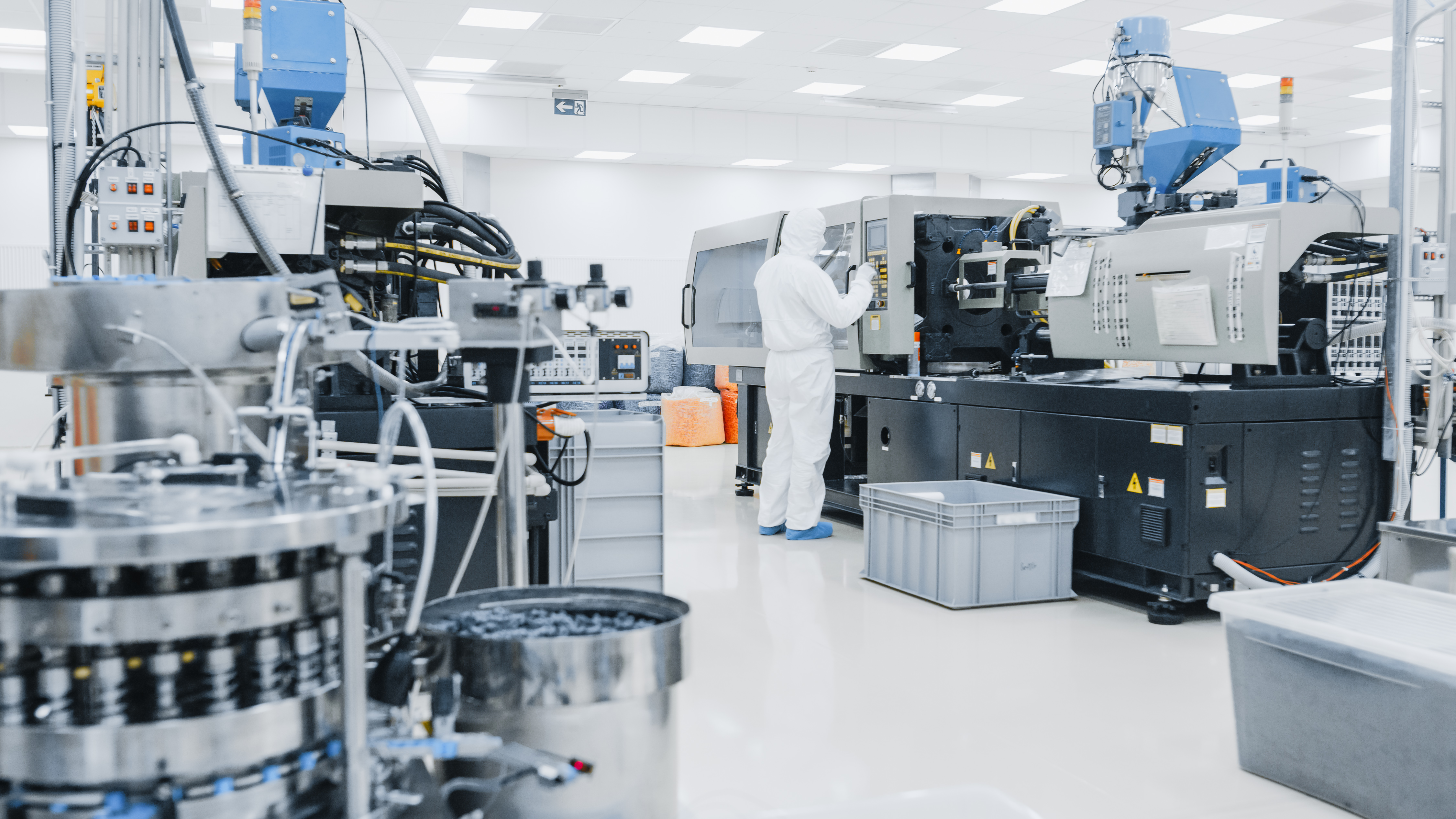
Objective: paperless manufacturing and complete digital batch recording
In the specifications for the system, the classic functions of a line controller such as order and recipe management, product tracking and recording of machine data were taken as given. The machine and operating data recorded digitally during production optimize line availability and enable a rapid response in the event of process deviations.
The main objective of the line controller was to introduce digital batch reporting and replace paper on the production line, while avoiding sources of error in data entry. The task for Kontron AIS was therefore to gather all the data required for electronic batch recording from the individual production line components using appropriate interfaces, while at the same time ensuring their correct and complete transmission. EUROMAP as well as connections to PLC controls, SCADA systems and databases were used as interfaces.
The operator is then provided with a line controller that supports and automatically summarizes batch reporting with an Electronic Batch Record (EBR). Any interventions in the process are automatically recorded and saved in the audit trail. The system is also designed to support the operator with check lists for batch preparation and post-processing. This includes checking the recipes and parameters set on the line components. If necessary, any incorrect settings are indicated to the operator before production can be started. Automated workflows support the operator during production with cyclical tasks.
At the operational level, the biggest challenge was project management. A multitude of specifications and ongoing development of the process had to be brought together on the pilot line during the project. In addition, a large number of different people and decision-makers from the customer’s company as well as from the suppliers needed to be involved in the process. However, close cooperation between Kontron AIS and all project teams enabled a well-coordinated process and smooth implementation of the project.
Result: End-to-end highly automated production
Following an intensive concept and development phase, the line controller systems were successfully put into operation. The FabEagle®LC line controller communicates with the machine controls, the MES and a PIMS, enabling end-to-end highly automated production.
Your contact person
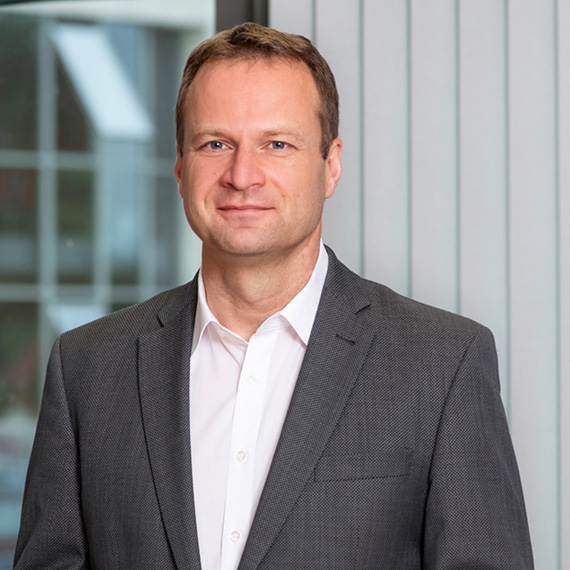