In the semiconductor industry, production systems are often used for many years – a service life of 20 to 25 years is not uncommon. This has many advantages: The equipment is firmly integrated into the production environment, the processes have been tested, and following depreciation, only operating costs are incurred. A clear advantage from a financial point of view.
But a long service life also comes with challenges. New trends and technical requirements arise, and older machines are often unable to keep up. In addition, support from the original manufacturer (OEM) often ends.
Retrofits are becoming increasingly relevant to secure the operation of production machines over the long term. This blog post explains how a retrofit not only extends the service life of machines, but also opens new innovation potential.
Challenges for existing machines in long-term operation
Challenges for existing machines in long-term operation
Owners of equipment with a long service life are faced with a number of challenges that become increasingly demanding as the machines get older:
- Spare parts availability and support
- Inadequate availability of development information such as circuit diagrams and descriptions of the equipment control interface
- Ever shorter innovation cycles and increasing functional changes
- Comprehensive training required due to outdated and non-transparent operating principles
These challenges mean that equipment availability decreases, and productivity suffers.
Current trends in semiconductor factories
The semiconductor industry is facing technological evolution that is permanently changing the production landscape. New trends are shaping the future of modern semiconductor factories and at the same time place demands on existing equipment. This includes a higher level of connectivity, which enables seamless integration of machines and processes. As connectivity increases, so does the risk of cyber attacks. Standards such as SEMI E187, E188 and E191 come into play here to protect your production machines and IT components from potential threats, data theft and operational disruptions.
Another central focus is on advanced data acquisition, data analysis and the use of big data and artificial intelligence (AI), which enable data-driven optimization of production processes. What is more, a higher level of automation means that less manual work is required, which increases efficiency and accuracy. The reliable combination of data usage, automation and connectivity enables the semiconductor industry to become even more stable and powerful.
A retrofit can bridge the gap between existing infrastructure and new requirements by bringing connectivity, automation and security standards up to date.
Higher level of connectivity – SECS/GEM and GEM300
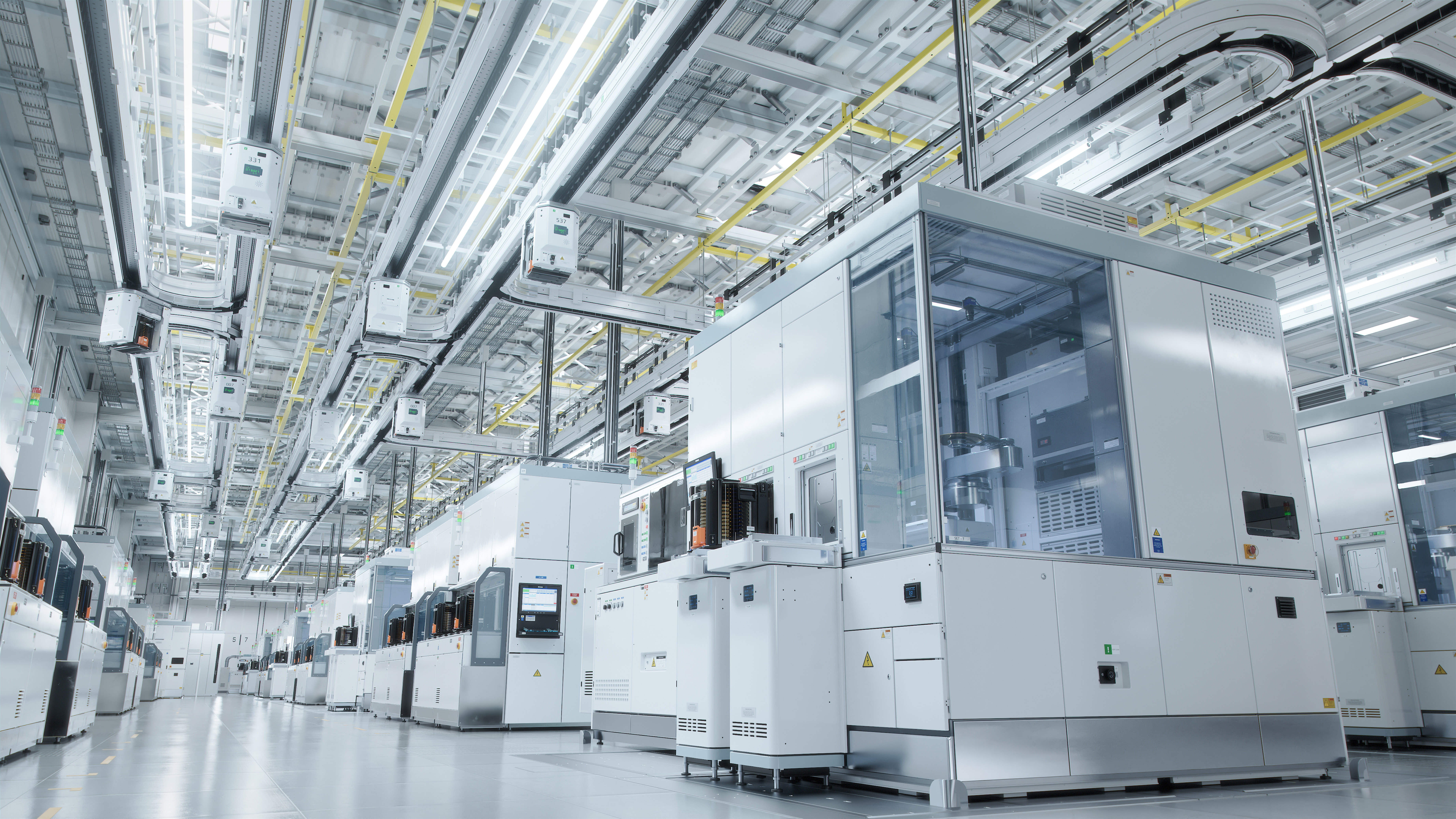
Objective | Transparent production and rapid integration of equipment into the fab IT environment. |
Strategy | Equip production systems with SEMS/GEM or GEM300 SEMI interfaces. |
Cybersecurity – SEMI E187, E188, E191
Objective | Protect against cyber attacks that disrupt production or bring production to a standstill, the theft of intellectual property such as recipes and other data, and industrial espionage. |
Strategy | Implement SEMI cybersecurity standards for secure production plants (SEMI E187), secure machine integration and maintenance in semiconductor factories (SEMI E188) and an overview of the current security situation of all IT components integrated into the factory network to quickly close security gaps (SEMI E191). |
Advanced data acquisition and analytics – EDA
Objective | Increased process security. |
Strategy | Integrate SEMI EDA interface for comprehensive data acquisition and data analysis for sustainable optimization of the production process. |
Higher level of automation – AGVs and OHTs
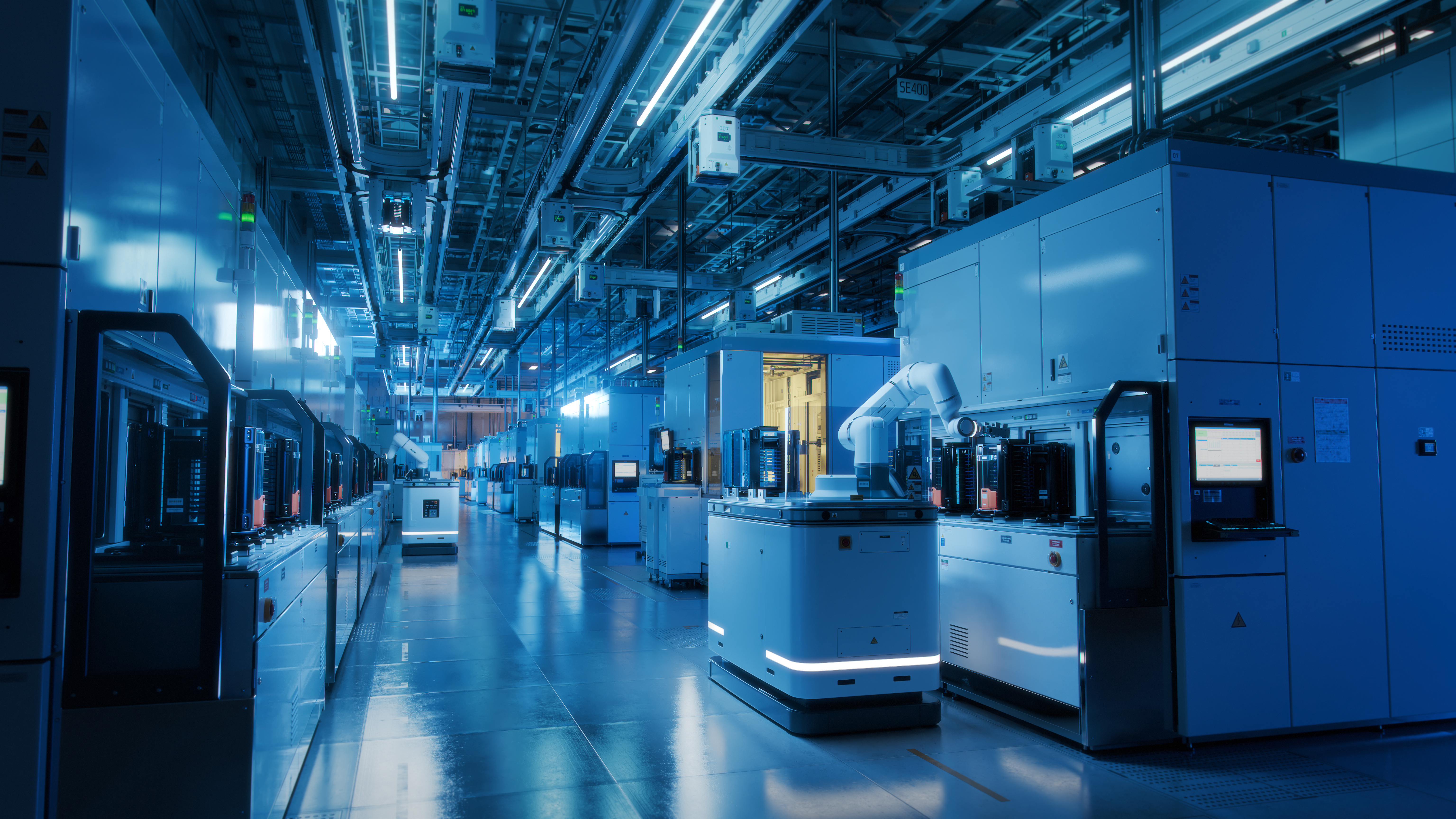
Objective | Save cost with production 24/7. |
Strategy | Implement automated transport systems such as AGVs and OHTs. |
Old vs. new – When is a retrofit the right choice?
Both the purchase of new equipment and the retrofit of an existing machine have advantages and disadvantages. When a new equipment is integrated into production, it is technologically up to date and support is ensured for many years. However, this entails very high acquisition and integration costs, because all the hardware is replaced.
By contrast, for a retrofit, the majority of existing hardware can continue to be used. Only some of the components or modules for which spare parts are no longer available need to be replaced.
If both the outdated hardware and the equipment control software are upgraded, not only does this increase productivity, it also ensures greater production process security. A retrofit meets current cybersecurity requirements in accordance with applicable rules and standards.
Another advantage is that support is available for the equipment again after it has been upgraded. This solution requires significantly less expense than a completely new installation. Starting the machine up again, training employees and qualifying the systems can also be implemented faster and easier with a retrofit.
Retrofit in semiconductor production
In the semiconductor industry there are three main aspects that are decisive for a retrofit:
1. SEMI-compliant connectivity
Depending on the interface – SECS/GEM, GEM300 or EDA – there are different advantages. For fabs who have so far not connected their machines to their IT environment in compliance with semiconductor industry standards, integration as per SECS/GEM offers a new level of transparency for the first time in addition to the rapid integration of additional systems: SECS/GEM provides direct insight into production data and offers information on the current status of production equipment.
More and more semiconductor fabs are switching from SECS/GEM to GEM300, as this interface offers more features and a higher level of integration. GEM300, for example, enables job management with control and process jobs, which makes it easier to integrate automated transport systems such as AGVs or OHTs. At the same time, the GEM300 interface ensures precise tracking of materials and production steps. This saves cost for 24/7 operation and optimizes production thanks to better scheduling. Here, too, integration can be implemented quickly thanks to standardized requirements.
EDA offers a new level of transparency as a parallel interface to SECS/GEM and GEM300. With EDA, large amounts of data are collected and transmitted so that a larger database is available for analyses using data science, forming a basis for AI applications. This is how the best measures for increased process efficiency can be derived.
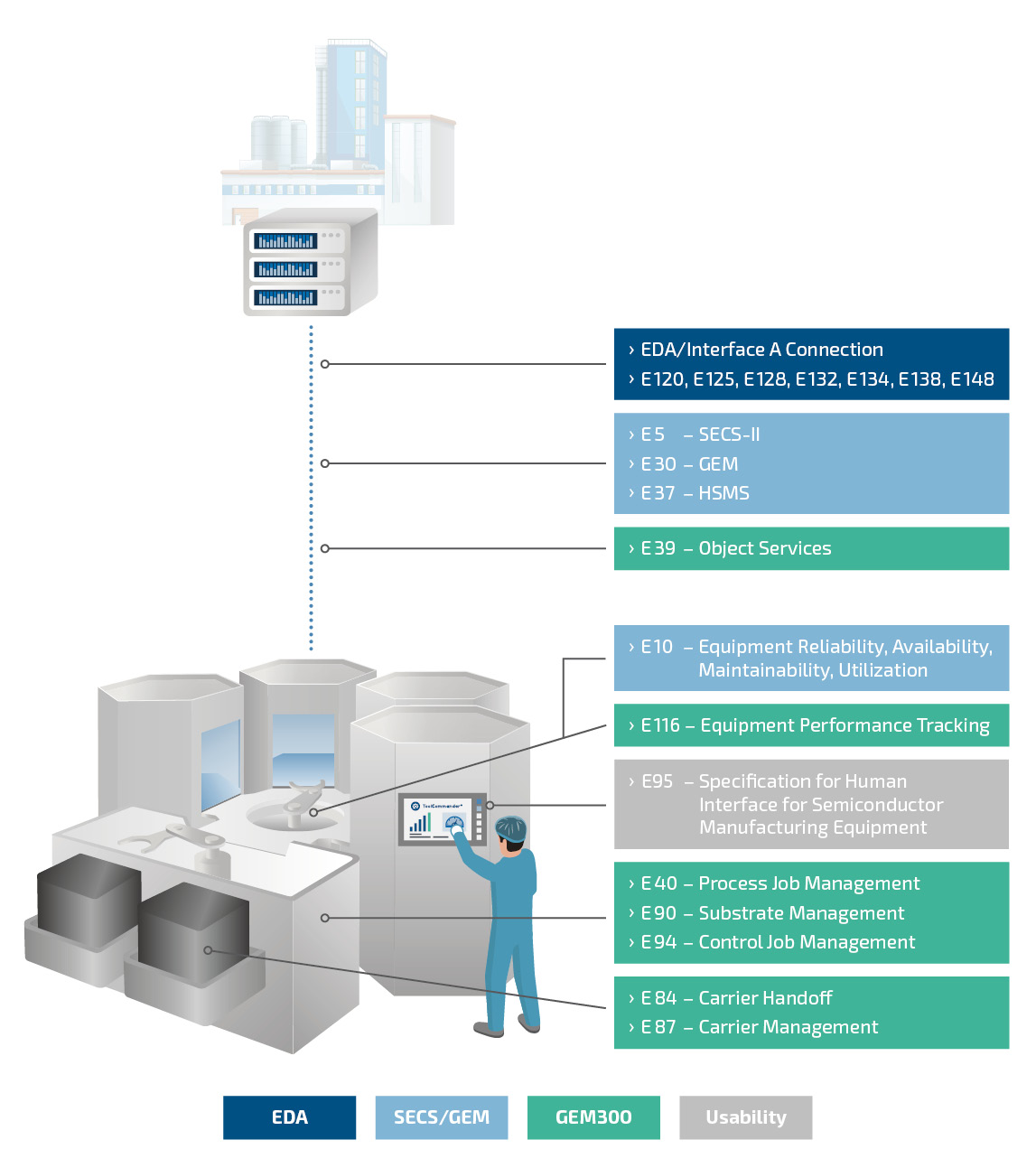
2. Update equipment control software
Nobody likes to change tried and trusted computer programs. The HMI of the existing system is familiar and operators know exactly where and how they need to interact and control the system using the GUI. Even with older machines, they can cleverly navigate to the view they need using various key combinations.
What is easy for long standing operators is a major challenge for new employees because it requires considerable background knowledge and a long learning phase on the equipment. In addition, complex operation with unclear user guidance poses a high risk of operating errors.
A modern GUI with intuitive user guidance enables short learning times, provides a clear overview at all times and ensures transparency for the operator. This also results in a high level of acceptance of the equipment control among new employees. Higher system availability is achieved thanks to a lower occurrence of errors during operation.
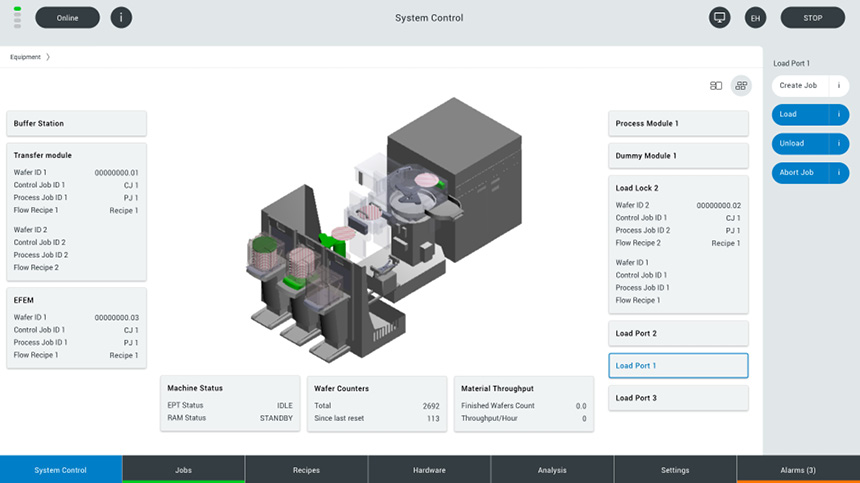
In addition to the GUI, all the control system software should be checked for the following factors:
- Are improvements and new features required that could be integrated with a retrofit?
- Are the current software and all basic systems future safe and secure?
- Are there any existing issues with available upgrades?
- Is there a partner for rapid maintenance and support?
3. Hardware component replacement and upgrade
The replacement of defective and discontinued components that have reached their end-of-life, such as pumps or slot cards, is key to hardware retrofitting. A retrofit can also be used to integrate new functions, for example by integrating additional sensors or replacing entire components such as a robot or motor. In addition, it is a good opportunity to replace outdated components that may be discontinued soon or are error prone. This ensures the long-term availability of these components, which in turn contributes to equipment availability.
Retrofit with Kontron AIS
Our end-to-end strategy includes not only software but also the replacement of hardware components. Together with you, we develop a concept, take into account your specific requirements and, if you are interested, involve you directly in the realization process. A retrofit project with Kontron AIS is carried out as follows:
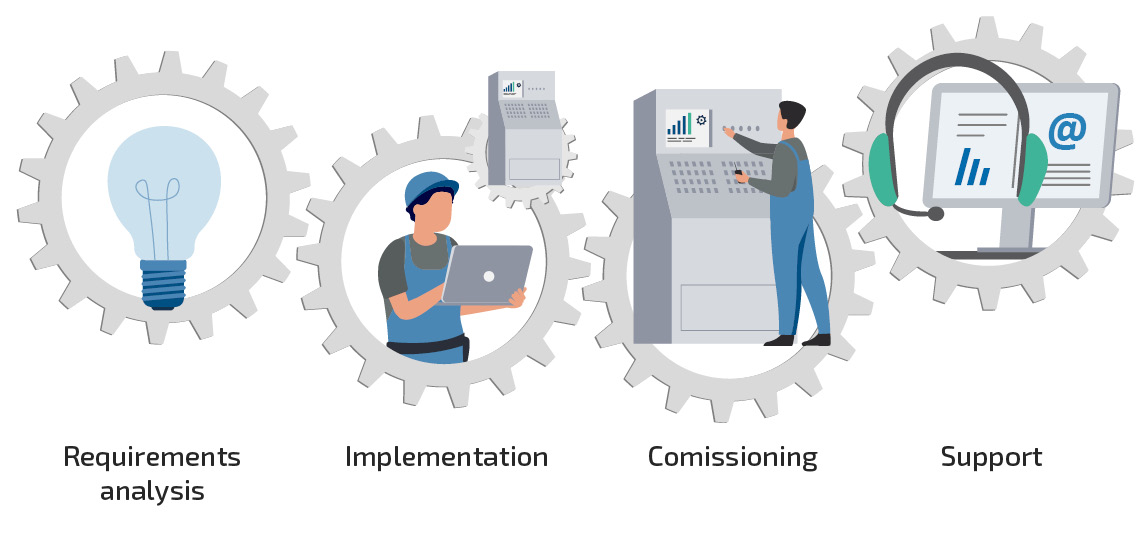
Requirements analysis:
Together with you, we assess the current situation, collect information about the equipment and define objectives and features that are to be achieved with the retrofit. Here, also the components will be defined – hardware as well as software – that should continue to be used and be part of the new solution.
Implementation:
We will carry out the retrofit on a schedule agreed with you. We use our software built for and accepted in the semiconductor industry: ToolCommander® framework for equipment control and our FabLink® software solution for SEMI-compliant integration using SECS/GEM, GEM300 and EDA.
Commissioning:
Following realization of the project, it is commissioned in the fab with our team on site. We do this in several stages. First, the individual components are started up, then the entire system is put into operation and, finally there is the test and handover together with the customer.
Support:
Once commissioning has been completed, Kontron AIS will provide ongoing support. At Kontron AIS, retrofits are always carried out in consultation with the equipment manufacturer (OEM) and are offered exclusively for systems that are no longer supported.
Conclusion
Production equipment in the semiconductor industry represents a valuable and future orientated investment aimed at long-term competitiveness. A retrofit helps to extend the service life of production equipment and to maintain system availability. It is also possible to include new trends such as increasing automation, connectivity, and the optimization of production by implementing data acquisition and analysis on a large scale. This reduces cost, increases productivity and enhances process security. New specifications and legislative requirements, such as compliance with SEMI Cybersecurity Standards and the Cyber Resilience Act (CRA), can also be implemented efficiently during a retrofit. With more than 30 years of expertise in control system programming and integration in the semiconductor industry, Kontron AIS is the ideal partner for your retrofit project.
Profit from a retrofit and extend the service life of your semiconductor production systems. Contact us and we will advise you on how to make your production equipment fit for the future.
Your contact person
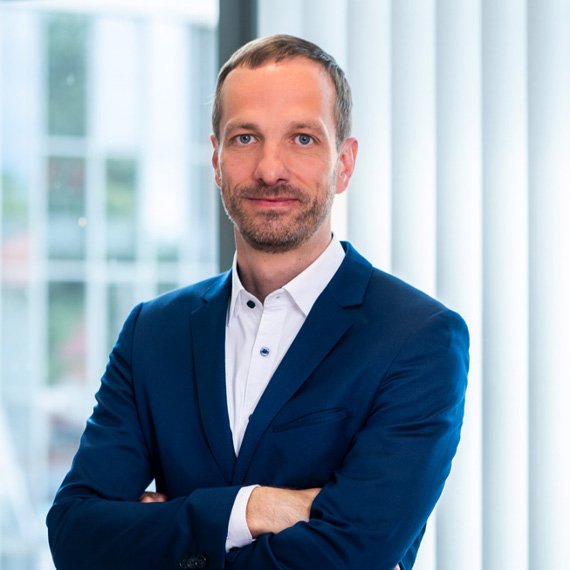