In industrial production, standards and low-code configurations are often the key to efficient integration of machines and systems. Nevertheless, practice shows that every integration project involves challenges that cannot be solved without in-depth expert knowledge. In this interview I talk to Michael Bauer, our Team Leader for Integration and Monitoring, about everything that goes into successful integration projects.
Michael leads an experienced team of nine colleagues who implement sophisticated integration projects in manufacturing for our customers every day. Together, we will explore why expertise remains essential, why connectivity is much more than plug and play, and how the right approach can make your production fit for the future.
We support our customers with software solutions in many different areas. In which applications do you implement integration projects?
Michael: Basically, our projects are always about data interface integration, particularly for complex manufacturing systems. We are currently working on machines with an SECS/GEM interface, which needs to be connected to an existing MES. With this industry-specific interface, we support production environments in the semiconductor sector, and in industries that use processes and machines from this sector.
But we have also worked on completely different projects. For example, we implemented horizontal communication between machines for a customer based on the TCP/IP standard with PLC function modules for the entire production process. One of our most frequent tasks is to integrate machines into ERP systems such as SAP, MES, databases or cloud solutions. This primarily involves the transfer of process parameters, measured values, status information and recipe parameters.
Talking about more complex integration projects, OPC UA has set out to standardize connectivity across industries. How have you seen this work in practice?
Michael: As an interface standard, OPC UA is an asset for industry due to its universal application, but each OPC UA interface has its own characteristics. The standard defines the transfer mechanism itself and the data formats that are supported. This makes the standard suitable for the transfer of complex data structures, which are different for every machine manufacturer. A compromise designed to solve these cases is the companion specifications, which define the respective structures more precisely for specific applications and specific types of machines. In practice, however, these are not yet widely used, making coordinating the data structure between machine PLC and target system a frequent task in our projects. In principle, OPC UA is a significant step forward in standardizing connectivity, but simple plug & play is currently unthinkable because every application is different.
Okay, so with more complex interface protocols, we get a bit of standardization, but also a lot of complexity. How do you help our customers find the right path?
Michael: OPC UA and comparable complex standards such as SECS/GEM enable the transfer of various data types, structures and models. That is why for our customer projects we start by analyzing existing data interfaces. We then implement the required logic, which transforms the type, structure, and data model into the right format for the target system. While the standard defines the method of transfer, our logic in between ensures the compatibility of different data structures and types.
However, it is not always simply a matter of connecting existing interfaces. We also often provide support in choosing the appropriate interface standard, because not every application requires complex and versatile standards. It is about finding the easiest solution for the specific application, also in terms of price and performance.
When recommending the right path, the factors of time and know-how also need to be taken into consideration. With our experienced team, we can usually select the best solution and implement the logic faster and more cost-effectively than the customer’s production IT can do on top of its day-to-day business.
You've already talked about specific processes. Can you talk us through the phases of a typical integration project?
Michael: Usually we support our sales team in providing individual advice to the customer during the inquiry phase. This includes a rough analysis of documents and recommendations for suitable solutions. In cases where FabEagle®Connect could be implemented, we give customers a demo to give them a first insight.
The actual project then starts with the specification phase after the order has been placed. To kick off, we analyze the existing machine documentation. If the manufacturer does not have a specification for the machine interface, we speak directly with the machine manufacturer or the MES provider to define the technical details of the interface and data transmission. This includes the details described above, such as data structure and formats, and the specific choice of which interface is used for the application, if there are various options available.
Once everything is specified, we start implementing the defined functions such as data transformation and aggregation, the logics and the data interface configuration in terms of properties and parameters. For this, we use our FabEagle®Connect interface integration software. Here, the modular component design allows us to separate specific logics and interface standards. In a simple application, the configuration consists of a component for the machine's interface standard, one for the logic that is applied to the data to be transmitted, and one for the interface standard of the target system, such as an MES.
Before a project solution is delivered to the customer, we test everything in a virtual test environment. This allows us to simulate data sources and carry out data transfer manually in unit tests. Once these tests have been completed, we are ready to arrange a date with the customer or with the machine supplier for commissioning.
The start-up itself is usually carried out remotely and begins with installing the software and setting up the prepared configurations. Interface testing is then performed with the customer’s production IT or with the machine manufacturer, and upon successful completion, the project is accepted. Parallel to commissioning, we also offer trainings so that production IT is optimally prepared to make changes on its own later on.
You use FabEagle®Connect in your projects. Which task does the integration software handle for you and for our customers?
Michael: FabEagle®Connect handles everything defined by standards and provides a framework for components that can be combined with each other. This means that the software adopts the transfer mechanisms in compliance with the applied interface standards to provide users with an interface for easy configuration of parameters and settings. The modular architecture lets the framework be extended with specific components, e.g. for edge logic.
To implement project-specific logic, either the code component can be used, or a completely new component can be created. The second one requires a certain level of know-how and understanding at code level in C#. Compared to other solutions, FabEagle®Connect offers a high level of openness to implement even very specific and complex solutions.
After commissioning, we are often still involved. What are the typical services that you provide as part of maintenance and support?
Michael: Support and maintenance requirements can vary significantly depending on the customer and the project. Normally, it involves expanding existing projects, carrying out updates and providing support in the event of an error. Typical projects include, for example, the connection of new third-party systems such as ERP, cloud or QM databases, and changes that are necessary as a result of modifications to the system. Then there is carrying out updates. Our product development team regularly provides new features and security updates. We also recommend every customer takes out an active maintenance and support contract if they are using software on production systems. This helps our support team to work faster and more efficiently when the customer’s production IT needs our support.
Once installed, software should run reliably for years. What needs to be taken into particular consideration to operate integration solutions securely over many years?
Michael: Software is only secure if it is also regularly maintained, i.e. if updates are installed regularly. This also applies to the platform itself, such as the machine PC, the server or the IoT boxes implemented. Here, too, the operating system, drivers and, if applicable, security tools need to be updated. We recommend carrying out regular minor updates as well, although larger jumps are also possible. However, these could be more complicated, because the migration path is often not linear.
Is there anything else you would like to share with our customers?
Michael: The most important thing is to not underestimate connectivity in production, because what sounds straightforward due to the standards can suddenly become very complex in certain scenarios. Especially when it comes to in-house developments, topics such as test coverage, special cases, data security and maintainability are sometimes severely underestimated.
Software such as FabEagle®Connect is an important part of any automated manufacturing scenario because of its central role in data transmission. Appropriate maintenance and standardization across multiple machines can significantly simplify work for the customer’s production IT. Connectivity is not only a question of efficiency, but also an investment in data security and machine uptime.
Would you like to find out more about how we can also support your integration process? We would be pleased to help you!
Your contact person
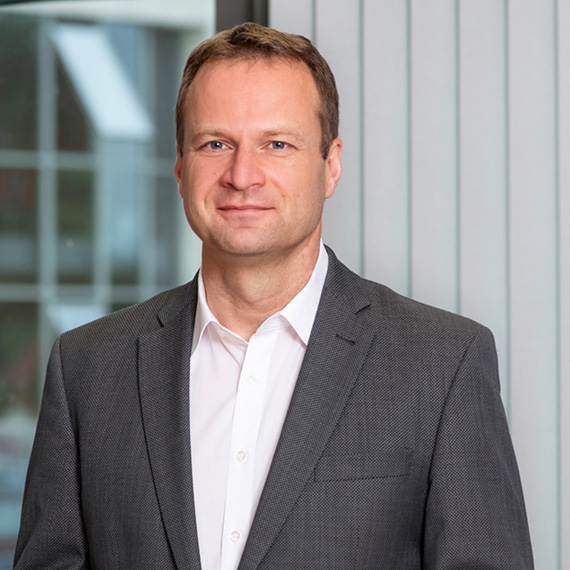