In der industriellen Produktion sind im Bereich der Konnektivität Standards und Low-Code-Konfigurationen oft der Schlüssel zur effizienten Integration von Maschinen und Anlagen. Trotzdem zeigt die Praxis: Jedes Integrationsprojekt bringt individuelle Herausforderungen mit sich, die nicht ohne fundiertes Expertenwissen zu bewältigen sind. In diesem Interview spreche ich mit Michael Bauer, unserem Teamleiter für Integration und Monitoring darüber, was alles zu erfolgreichen Integrationsprojekten gehört.
Michael leitet ein eingespieltes Team von neun Kolleginnen und Kollegen, das für unsere Kunden tagtäglich anspruchsvolle Integrationsprojekte in der Produktion umsetzt. Gemeinsam beleuchten wir, warum Expertise unverzichtbar bleibt, warum Konnektivität weit mehr ist als Plug-and-Play und wie mit der richtigen Herangehensweise auch Ihre Produktion fit für die Zukunft wird.
Wir unterstützen unsere Kunden mit Softwarelösungen in ganz unterschiedlichen Bereichen. Für welche Anwendungen setzt ihr Integrationsprojekte um?
Michael: Grundsätzlich geht es in unseren Projekten immer um Datenschnittstellenintegration, besonders für komplexe Produktionsanlagen. Aktuell beschäftigen uns vor allem Anlagen mit SECS/GEM-Schnittstelle, die an bereits bestehende MES-Systeme angebunden werden müssen. Mit dieser branchenspezifischen Schnittstelle unterstützen wir Produktionsumgebungen im Halbleiterbereich und in Industrien, die Prozesse und Anlagen aus diesem Bereich einsetzen.
Aber auch schon ganz andere Projekte standen auf unserer Agenda. So haben wir für einen Kunden die horizontale Kommunikation zwischen Anlagen auf Basis des TCP/IP-Standards mit SPS-Funktionsbausteinen für die gesamte Produktion realisiert. Am häufigsten integrieren wir übrigens Maschinen in ERP-Systeme wie SAP, MES, Datenbanken oder Cloud-Lösungen. Dabei geht es vor allem um die Übertragung von Prozessparametern, Messwerten, Statusinformationen oder Rezeptparametern.
Stichwort komplexere Integrationsprojekte: OPC UA ist angetreten, die Konnektivität branchenübergreifend zu standardisieren. Wie nimmst du das in Praxis wahr?
Michael: OPC UA ist als Schnittstellenstandard durch seine universelle Anwendung eine Bereicherung für die Industrie, aber es gibt nicht die eine OPC UA Schnittstelle. Definiert wird in erster Linie der Übertragungsmechanismus selbst und unterstützte Datenformate. Damit eignet sich der Standard für die Übertragung komplexer Datenstrukturen und genau diese sehen bei jedem Maschinenhersteller unterschiedlich aus. Ein Kompromiss, der diese Fälle lösen soll, sind die Companion-Specifications, die für bestimmte Anwendungen oder Maschinentypen die jeweiligen Strukturen genauer definieren. In der Praxis sind diese aber noch nicht weit verbreitet, womit die Abstimmung der Datenstruktur zwischen Maschinensteuerung und Zielsystem eine häufige Aufgabe in unseren Projekten ist. Grundsätzlich ist OPC UA ein deutlicher Fortschritt bei der Vereinheitlichung der Konnektivität, aber aktuell ist ein einfaches Plug & Play aufgrund der unterschiedlichen Anwendungen nicht denkbar.
Im Grunde bekommen wir mit komplexeren Schnittstellenprotokollen also ein Stück Standardisierung, aber eben auch viel Komplexität. Wie helft ihr unseren Kunden dabei, den richtigen Weg zu finden?
Michael: OPC UA und vergleichbare komplexe Standards wie SECS/GEM ermöglichen die Übertragung unterschiedlicher Datentypen, -strukturen und -modelle. In unseren Kundenprojekten beginnen wir daher mit der Analyse eventuell vorhandener Datenschnittstellen. Danach implementieren wir die erforderliche Logik, die den Typ, die Struktur oder das Datenmodell in das Zielsystems umwandelt. Der Standard definiert also die Art und Weise der Übertragung, unsere Logik dazwischen stellt die Kompatibilität unterschiedlicher Datenstrukturen oder -typen her.
Es geht aber nicht immer nur darum, bestehende Schnittstellen zu verbinden. Häufig helfen wir auch bei der Auswahl des passenden Schnittstellenstandards, denn nicht jeder Anwendungsfall erfordert komplexe und vielseitig einsetzbare Standards. Es geht darum, die einfachste Lösung für die konkrete Anwendung zu finden, auch im Hinblick auf Preis und Leistung.
Bei der Frage nach dem richtigen Weg dürfen auch die Themen Zeit und Know-how nicht vergessen werden. Die Auswahl der besten Lösung und die Umsetzung der Logik können wir mit unserem eingespielten Team meist schneller und kostengünstiger umsetzen, als es eine Produktions-IT parallel zum Tagesgeschäft kann.
Du hast jetzt schon von gewissen Abläufen gesprochen. Kannst du uns mal gedanklich durch alle Phasen eines klassischen Integrationsprojektes bei euch führen?
Michael: In der Regel unterstützen wir in der Anfragephase unseren Vertrieb bei der individuellen Beratung des Kunden. Dazu gehören die grobe Analyse von Unterlagen und Empfehlungen zu passenden Lösungsoptionen. Wenn es erforderlich ist, geben wir auch mit der FabEagle®Connect Demo einen ersten Einblick in eine mögliche Umsetzung.
Das eigentliche Projekt beginnt dann nach der Auftragserteilung mit der Spezifikationsphase. Wir analysieren die vorhandenen Maschinendokumente. Falls herstellerseitig keine Spezifikation der Maschinenschnittstelle vorliegt, sprechen wir direkt mit dem Maschinenbauer oder dem MES-Anbieter, um die technischen Details der Schnittstelle und Datenübertragung zu definieren. Dazu gehören die bereits beschriebenen Details wie Datenstruktur und -formate oder auch die konkrete Auswahl, welche Schnittstelle für die Anwendung verwendet wird, falls sich verschiedene Optionen anbieten.
Ist alles spezifiziert, beginnen wir mit der Implementierung der definierten Funktionen wie Datentransformation und -aggregation, der Logiken und der Datenschnittstellenkonfiguration hinsichtlich Eigenschaften und Parametern. Dafür verwenden wir unsere Schnittstellenintegrationssoftware FabEagle®Connect. Dort haben wir durch den modularen Komponentenaufbau die Möglichkeit, spezifische Logiken und Schnittstellenstandards zu trennen. In einer einfachen Anwendung besteht die Konfiguration aus einer Komponente für den Schnittstellenstandard der Maschine, einer für die Logik, die auf die zu übertragenden Nachrichten angewendet wird und einer für den Schnittstellenstandard des Zielsystems wie eines MES.
Bevor eine entwickelte Integrationslösung an den Kunde geht, testen wir alles in einer virtuellen Testumgebung. Dabei werden Datenquellen simuliert oder die Datenübertragung in Unittests manuell ausgeführt. Sind diese Tests abgeschlossen, steht dem Termin zur Inbetriebnahme beim Kunden oder beim Maschinenlieferanten nichts mehr im Wege.
Die Inbetriebnahme selbst erfolgt in der Regel Remote und beginnt mit der Installation der Software und der Einrichtung der vorbereiteten Konfigurationen. Im Anschluss wird mit der Produktions-IT oder mit dem Maschinenbauer der Schnittstellentest durchgeführt, der nach erfolgreichem Abschluss mit der Abnahme endet. Parallel zur Inbetriebnahme bieten wir auch Schulungen an, damit die Produktions-IT optimal vorbereitet ist, um später auch selbst Änderungen vorzunehmen.
Ihr setzt FabEagle®Connect in euren Projekten ein. Welche Aufgabe übernimmt die Integrationssoftware für euch bzw. für unsere Kunden?
Michael: FabEagle®Connect übernimmt alles, was durch Standards definiert ist und bietet ein Framework für Komponenten, die miteinander kombiniert werden können. Das bedeutet, die Software übernimmt die Übertragungsmechanismen entsprechend den eingesetzten Schnittstellenstandards und bietet Nutzerinnen und Nutzern eine Oberfläche zur einfachen Konfiguration von Parametern und Einstellungen. Die modulare Architektur erlaubt die Erweiterung des Frameworks um spezifische Komponenten z.B. für Edge-Logik.
Für die Umsetzung projektspezifischer Logiken kann entweder die Code-Komponente genutzt oder eine komplett neue Komponente erstellt werden. Wobei letzteres ein gewisses Know-how und Verständnis auf Code-Ebene in C# voraussetzt. Im Vergleich zu anderen Lösungen bietet FabEagle®Connect eine hohe Offenheit, um auch sehr individuelle und komplexe Lösungen zu realisieren.
Nach der Inbetriebnahme ist für uns oft noch nicht Schluss. Was sind die klassischen Leistungen, die ihr im Rahmen von Wartung und Support erbringt?
Michael: Support und Wartung können je nach Kunde und Projekt sehr unterschiedlich sein. Grundsätzlich geht es um Erweiterungen bestehender Projekte, Updates und Unterstützung im Fehlerfall. Klassiker sind dabei z.B. die Anbindung von neuen Drittsystemen wie ERP, Cloud oder QM-Datenbanken oder auch Änderungen, die durch Umbauten an der Anlage notwendig werden. Nicht zu vergessen ist die Durchführung von Updates. Unsere Produktentwicklung stellt auf diesem Weg regelmäßig neue Funktionen und Sicherheitsupdates bereit. Dabei empfehlen wir auch jedem Kunden, der Software auf Produktionsanlagen einsetzt, einen aktiven Wartungs- und Supportvertrag. So kann unser Supportteam schneller und effizienter arbeiten, wenn die Produktions-IT unsere Hilfe benötigt.
Software, die einmal installiert ist, soll über Jahre hinweg zuverlässig laufen. Was ist zu beachten, um insbesondere Integrationslösungen über Jahre hinweg sicher zu betreiben?
Michael: Sicher ist Software nur dann, wenn sie auch regelmäßig gepflegt wird, also wenn regelmäßig Updates installiert werden. Das gilt auch für die Plattform selbst, wie den Anlagen-PC, den Server oder verwendete IoT-Boxen. Auch hier müssen Betriebssystem, Treiber und ggf. Sicherheitstools aktualisiert werden. Empfehlenswert sind außerdem regelmäßige kleine Updates, wobei auch größere Sprünge möglich sind. Diese könnten aber aufwendiger sein, da der Migrationsweg oft nicht geradlinig verläuft
Was möchtest du unseren Kunden noch mit auf den Weg geben?
Michael: Das Wichtigste ist, das Thema Konnektivität in der Produktion nicht zu unterschätzen, denn was aufgrund der Standards einfach klingt, kann in bestimmten Szenarien plötzlich sehr komplex werden. Gerade bei Eigenentwicklungen werden Themen wie Testabdeckung, Sonderfälle, Datensicherheit und Wartbarkeit stark unterschätzt.
Software wie FabEagle®Connect ist wegen ihrer zentralen Rolle in der Datenübertragung ein wichtiger Bestandteil jeder automatisierten Fertigung. Eine angemessene Pflege und Standardisierung über mehrere Anlagen hinweg kann die Arbeit in der Produktions-IT erheblich vereinfachen. Konnektivität ist nicht nur eine Frage der Zweckmäßigkeit, sondern auch eine Investition in die Datensicherheit und Verfügbarkeit.
Sie wollen mehr darüber erfahren, wie wir auch Ihre Integration unterstützen können? Wir helfen Ihnen gern weiter!
Ihr Ansprechpartner
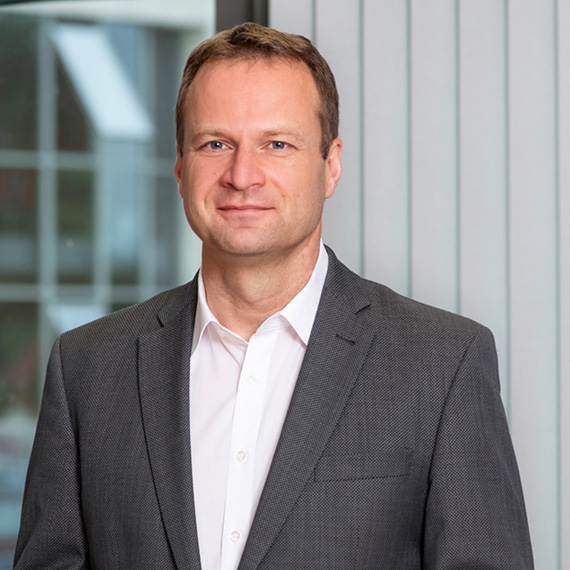