Eine der ersten Fragen, die sich Produktionsbetreiber und -planer bei der Digitalisierung Ihrer Fertigung stellen, ist die Frage, welche Steuerungsarchitektur bzw. Leitsystemkategorie passend ist. In der Produktionsleitebene der diskreten Produktion kommen vor allem zwei Konzepte zur Produktionssteuerung zum Einsatz: Die Liniensteuerung durch einzelne Leitrechner oder die zentrale Steuerung der ganzen Fabrik bzw. Produktion durch ein Manufacturing Execution System (MES). Welchem System sie den Vorrang geben sollten, ist für viele Fabrikbetreiber wie ein Kampf zwischen David und Goliath. Doch wie sieht die Konkurrenz genau aus und wer geht als möglicher Sieger hervor? Dieser Blogartikel hilft Ihnen bei der Einordnung anhand der sachlichen Schwerpunkte Dauer, Aufgaben und Kosten der Einführung.
Dauer und Meilensteine der Einführung eines Produktionsleitsystems
1. Lastenheft und Spezifikation
Die erfolgreiche Einführung eines Leitsystems beginnt mit der Zusammenstellung eines Lastenheftes. Dieses sollte nicht nur die Anforderungen an das neue Leitsystem definieren, sondern auch erste Schwerpunkte im Konzept der Datenerfassung und Anlagensteuerung dokumentieren. Die Dauer der Lastenhefterstellung hängt u.a. von der Größe des Bereichs ab, der digitalisiert werden soll und reicht für eine einzelne Liniensteuerung von wenigen Wochen bis zu mehreren Monaten für eine komplette Fabriksteuerung. Auf Basis der Anforderungen aus
- dem Lastenheft,
- der Maschinenspezifikationen,
- möglicher Workshop-Absprachen und
- der Anwendung seines Produktstandards,
erarbeitet der Systemlieferant die Spezifikation des Projektes und der Lösung. Der Zeitbedarf dafür ergibt sich aus der Anzahl der beteiligten Abteilungen, der Maschinen und der technologischen Komplexität (Logik im Prozessablauf). Da die Anzahl anzubindender Systeme mit verschiedenen Schnittstellen und Prozessen bei einem MES um ein Vielfaches höher sind, nimmt dessen Spezifikationen unter Einbezug aller Vernetzungen und Abhängigkeiten erheblich mehr Zeit in Anspruch als die eine Leitrechners, der den Fokus auf eine einzelne Produktionslinie legt.
2. Implementierung von Produkterweiterungen
Je nachdem wie weit das MES oder der Leitrechner von den spezifischen Anforderungen der Anlagen entfernt ist, findet in dieser Phase die Anpassung und Erweiterung der Softwarelösung statt. Die Lieferzeit wird dabei durch die Anzahl der zu konfigurierenden Prozesse, Datenquellen und spezifischen Ablauflogiken maßgeblich beeinflusst. Wurden schon Leitrechnersysteme eingesetzt, kann sich diese Phase aufgrund des Wiederholungscharakters verkürzen. Bereits realisierte Schnittstellen, Ablauflogiken oder Erweiterungen laufender Systeme können hier genutzt werden.
3. Inbetriebnahme
Die Inbetriebnahme ist immer ein Zusammenspiel verschiedener Abteilungen und Lieferanten. Die größte Aufgabe besteht darin, alle Datenschnittstellen einzurichten und zu testen. Darunter fallen Schnittstellen zu Maschinensteuerungen, Messgeräten und IT-Systemen wie ERP. Dies erfordert nicht nur eine Konfiguration auf der Seite des Leitsystems, sondern auch bei dem jeweiligen Ziel- oder Quellsystem. Der größte Faktor hinsichtlich der Inbetriebnahmedauer liegt in der Anzahl der einzubindenden Schnittstellen und Zusammenarbeit zwischen dem Softwarelieferanten und zuständigem Maschinenbauer bei ihrer Einrichtung und beim Test. Während bei einem Leitrechner nur ein Fertigungsbereich beteiligt ist, sind bei einem MES verschiedene Abteilungen im Rahmen der Inbetriebnahme involviert.
4. Einführung und Ramp-up
Nach der erfolgreichen Inbetriebnahme sind die Anlagenbediener*innen und Prozessingenieur*innen gefordert mit dem neuen System zu arbeiten. Das bedeutet Training für alle Nutzer*innen bezüglich der Eingabe von Rezepten, Stücklisten und Prozessparametern. Ramp-up bedeutet in diesem Sinne nicht nur den Testlauf für das System selbst, sondern auch für alle Bediener*innen, die mit dem neuen System neue Arbeitsabläufe erhalten haben. Eine MES-Lösung bedeutet somit ein Kraftakt für alle Produktionsbeteiligten, wo hingegen die Einführung von mehreren Leitrechnen gestaffelt durchgeführt werden kann.
Welche Unterschiede es bei den Kosten von Produktionsleitsystemen gibt
Die Einführung eines Produktionsleitsystems ist für die Betreiber nicht nur mit Zeitaufwand, sondern auch mit Kosten verbunden. Obwohl sich diese unabhängig von der eingesetzten Softwarelösung sehr schnell amortisieren, gibt es zwischen MES und Leitrechner wirtschaftliche Unterschiede. Bei beiden Lösungen teilen sich die Positionen in interne Kosten durch Personaleinsatz und externe Kosten wie die der Lösung selbst auf.
1. Kosten eines Leitrechners
Ein Leitrechner zeichnet sich besonders durch seine technische und kommerzielle Skalierung aus. Wird mit nur einem Teilbereich der Produktion gestartet, wird auch nur eine kleinere Software-Lösung benötigt. Spannend wird die Rechnung über mehrere Produktionslinien. Die sukzessive Einführung mehrerer Leitrechner erscheint auf den ersten Blick aufwendiger, rechnet sich aber, wenn ein hoher Wiederholungscharakter vorliegt und Verbesserungen direkt auf Folgelinien anwendbar sind.
2. Kosten einer MES-Lösung
Die initialen Kosten einer MES-Lösung sind deutlich höher als die eines Leitrechners, verkörpern aber einen fundamentalen Wechsel in der Arbeitsweise der gesamten Produktion. Ein MES kann vielleicht nicht den Vorteil der Wiederholbarkeit nutzen, ist aber dafür besser in der Lage, verschiedene Bereiche miteinander zu vernetzen und Abweichungen von der klassischen Linienbauweise zu steuern. Interne als auch externe Kosten fallen hier nur einmalig an, können aber durch die neu gewonnene Effizienz in der Automatisierung der Produktion umso schneller amortisiert werden.
David gegen Goliath – gibt es einen Gewinner?
Bei der Einführung eines Produktionsleitsystems gibt es bedeutende Unterschiede in Bezug auf Dauer, Aufgaben und Kosten. Während das MES eine ganzheitliche Integration aller Abteilungen ermöglicht, konzentriert sich der Leitrechner auf einzelne Produktionslinien. Dessen Inbetriebnahme erfordert eine sorgfältige Einrichtung von Schnittstellen, die Implementierung Zeit für Anpassungen und Erweiterungen, wobei der Wiederholungscharakter des Leitrechners von Vorteil ist. Die Kosten können variieren, wie auch beim MES, dessen Effizienz- und Automatisierungsvorteile eine wertschöpfende neue Arbeitsweise für die gesamte Produktion bieten. Der angestrebte Vergleich von David und Goliath mag bei den Themen der Flexibilität und Schnelligkeit zutreffen, aber ein eindeutiger Sieger lässt sich bei MES und Leitrechner nicht finden. Welches System besser abschneidet entscheidet am Ende die Duellarena, denn beide Systeme verfolgen das gleiche Ziel: Unternehmen durch eine verbesserte Vernetzung und Steuerung eine schnellere und effektivere Arbeit ermöglichen. Egal für welches System Sie sich also entscheiden – die Investition in ein modernes Produktionsleitsystem amortisiert sich in kürzester Zeit und treibt den Erfolg Ihres Unternehmens voran.
Ich berate Sie gern bei der Auswahl des richtigen Systems für die Digitalisierung Ihrer Fertigung.
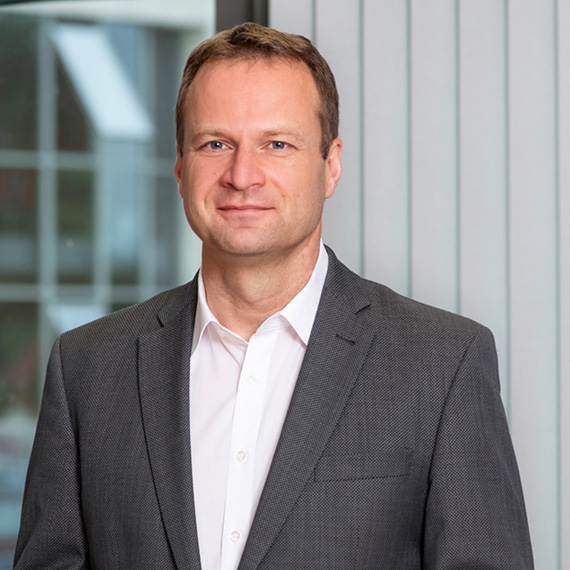