The first ALD (Atomic Layer Deposition) equipment from Beneq Oy with the Kontron AIS software framework ToolCommander® for equipment control was put into operation at the end customer. It was pre-tested in the Beneq Headquarter, in Espoo (Finland). The coating system is now used in China in a cluster for OLED microdisplay production. The Beneq Oy system consists of a heater, loadlock, transfer module and a process module, which is controlled by Beneq.
A special feature is that single-wafer processes and batch processes can run in the system. In addition to the equipment control solution using the ToolCommander®, Kontron AIS also realized a custom host integration protocol.
- Control of the ALD equipment with ToolCommander®
- High software quality and easy commissioning
- Support of single wafer batch and batch processing
- Custom horizontal and vertical interface
- Creation of a solution for future equipments
- Delivery of the control software ToolCommander® in time and budget
Seamless Integration of Beckhoff PLC for Advanced ALD Process
The ToolCommander® software framework from Kontron AIS GmbH is an universal equipment control framework supporting the control of batch, cluster and inline systems. In this project, Kontron AIS utilized the existing functionality of the ToolCommander® as the scheduler functionality and the user interface. In a custom project, the integration of the Beneq Oy Beckhoff PLC controlling the ALD process was realized. The Beckhoff TwinCAT protocol is used for the communication between ToolComander® and the Beckhoff PLC, allowing an easy integration. In addition to the integration of the Beckhoff PLC, ToolCommander® controls several components, e.g. the load lock or the pumping system of the transfer module directly. Direct control is achieved by using a distributed I/O station and by control via TCP/IP interfaces, for example.
The end customer in China defined for the vertical host integration a custom interface protocol. The protocol is generally similar to the SECS/GEM standard, but the streams and functions are custom. Therefore, the Kontron AIS integration team developed a customized message adapter.
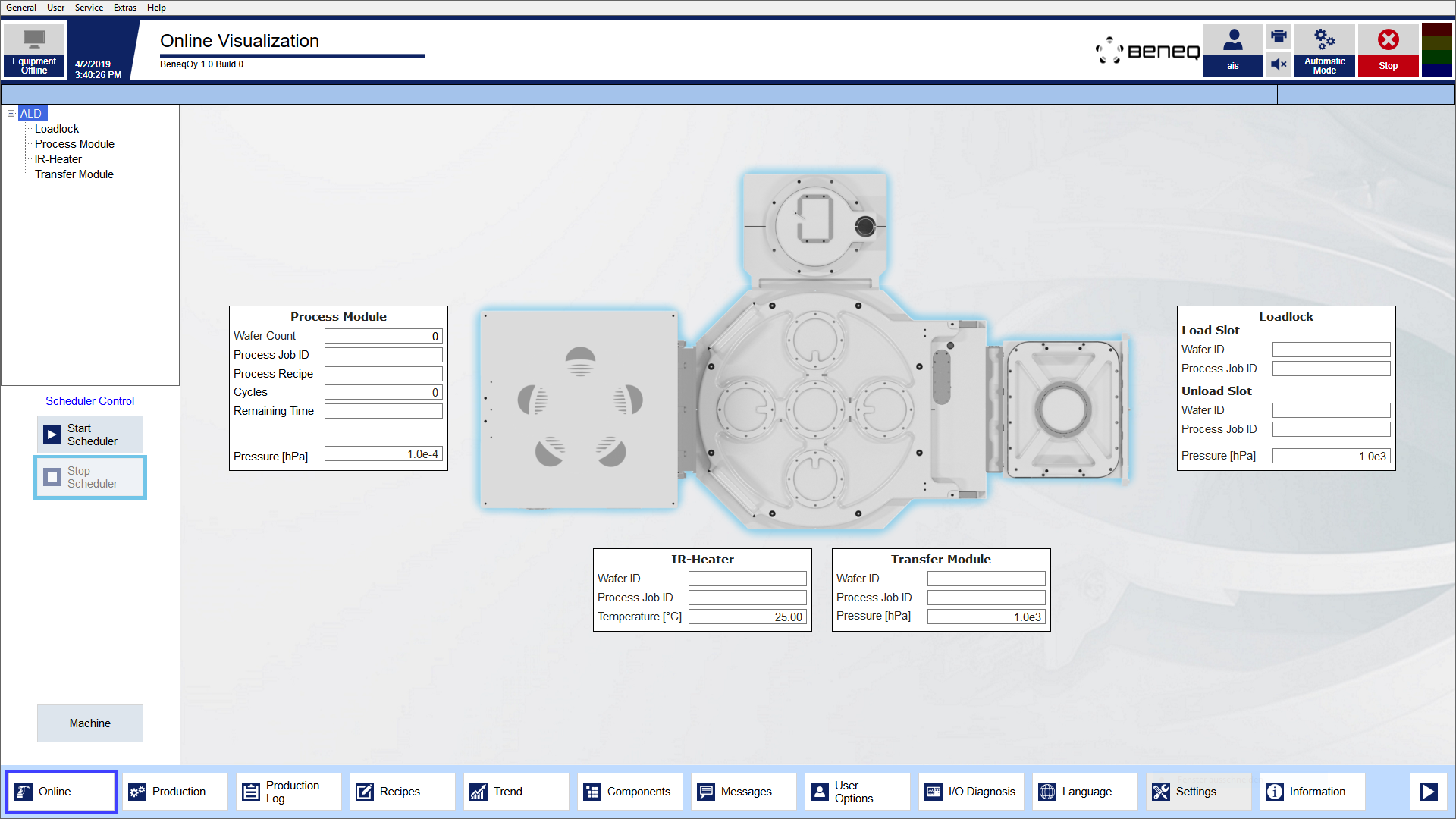
The horizontal integration into the main cluster was realized by CC-Link. The CC interface was also developed by Kontron AIS.
Project kick-off was at the end of the year, and the first step was a solid specification written by Kontron AIS in close collaboration with Beneq Oy. Part of this specification process was also the specification of the test scenarios. Due to the tight schedule, agreed parts of the specification were already developed by Kontron AIS before the specification was finalized. The next step was the in-house testing by the Kontron AIS test department, using the ToolCommander® simulation capabilities. After passing the in-house test, commissioning and pre-test were executed at Beneq Oy.
During this project phase, Kontron AIS was in a very close cooperation with the developers from Beneq Oy. About six months after the kick-off, the system was shipped to China and were it was finally commissioned by Beneq Oy and Kontron AIS.
If you would like to learn more about ToolCommander® system control and FabLink®, we look forward to hearing from you.
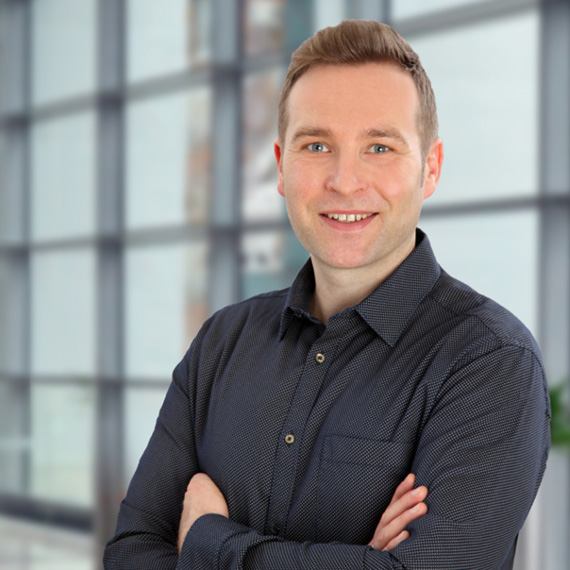
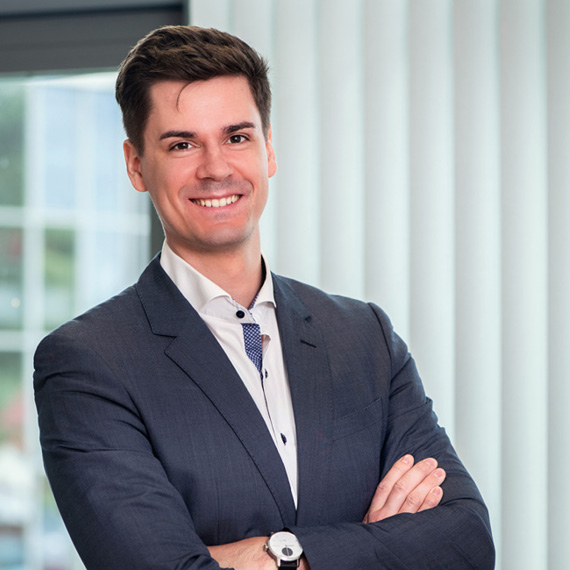