Renewing of the communication between the ZF IT systems and the ECS control system
The existing electric monorail system (EMS) of ZF Friedrichshafen AG at the Passau plant 2 was modernized in several stages. In addition to the structural conversion work, this also entailed changes in the IT landscape and data communication. The communication between the ZF IT systems and the EMS control system had to be renewed as the existing control system was replaced. In the course of this conversion, the historically grown IT applications were also updated to the ZF standard IT architecture.
“With the successful implementation of construction stage 1 – Renewal and optimization of ECS – the foundation stone has been laid for all further construction stages.”
Michael Habereder, Team Leader Maintenance and CIP, ZF Friedrichshafen AG
- Connection of ZF control system after replacement of the ECS control system
- Replacement of old visualizations by up-to-date Web GUIs
- Use of ZF IT standards
- Very tight schedule
- Final commissioning during two-week operating break
- Coordination of the physical construction work with the IT changeover
- Timely completion of visualizations and services
- Improved reliability through the use of high-availability servers and current technologies
Successful completion phase 1
The existing application structure in the EMS environment was gradually be replaced by ZF standard structures. The replacement takes place in several steps, parallel to the physical construction phases. The focus here is on guaranteeing the functionality of the individual applications so that production is not impaired.
In Phase 1, which has already been implemented, the connection to the EMS-PLC was implemented on the basis of the ZF standard connector. The ZF standard connector is an application that allows messages to be exchanged between pieces of equipment and IT systems using Apache ActiveMQ. The data required for the exchange with the ZF IT world was defined together with the supplier of the EMS PLC (Siemens AG) and the necessary messages were implemented. In addition, web-based visualizations were implemented using Angular 5.0. They instruct the operator, for example, which paint color is to be used for an aggregate or display packaging instructions. Services monitor the arrival and departure of the aggregates at certain positions and fill existing displays for capacity planning at the end of the conveyor system. The commissioning of the changes could be carried out successfully in the narrow time window of the summer production break and thus without obstructions of the production.
The next expansion stages will require further changes in the IT landscape. Other outdated applications will be replaced by standard technologies. ZF, Siemens and Kontron AIS will jointly define the new use cases and implement them again successfully, on schedule and with minimal impact on the production.
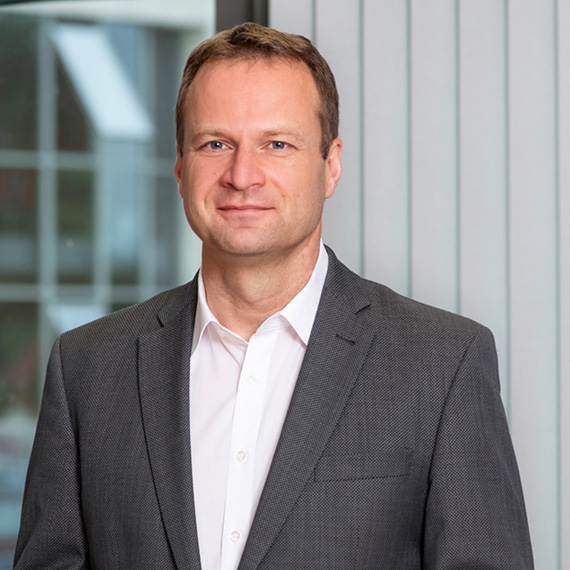