Highly demanding processes are carried out with complex process engineering systems. For equipment manufacturers, reliable system control is essential here. It is one of the main factors in the productivity of your machines and equipment. How do you find the right equipment control that best suits your processes, machinery, and requirements? Not many machine manufacturers are willing to concern themselves with the automation and programming of handling, so purchasing a ready-to-use control solution seems to be the answer. On the other hand, there is often a reluctance to hand over certain areas of control, such as the recipe system, to external partners. The core business of our customers is the extensive knowledge they have of their specialized processes, which must be protected as effectively as possible. This is why many machine manufacturers decide to develop the entire control system in-house. Both options have their pros and cons and, in many cases, neither one satisfactorily meets individual requirements. One solution is to use a software framework. This blog post reveals the 3 most important advantages and how you too can benefit from an open software framework for your machines.
How does using a framework benefit machine and equipment manufacturers?
Efficiency: existing basic structures save time
Especially when technologies and generations change, equipment controls not based on a framework are essentially written on a blank piece of paper and all the basics must first be defined. But with a software framework you benefit from existing basic structures. These do not only give you a head-start in programming, but implementation security, too. For example, templates for dialogs and basic functions such as logging, data management, event and alarm handling, and user administration already exist. Properties of certain components are pre-defined thanks to a declarative programming paradigm. In addition, a software framework already provides you with a component library from which you can transfer the required components directly into your project. The application model and API are configured for use in an equipment control. The aim is to achieve very high availability and provide data flows with low latency, consistent traceability and manipulation. Diagnostic capability is the essential feature that turns a software framework into a control framework.
Flexibility and independence: designing your own solutions
By implementing your system control yourself, all knowledge of your system stays with you. In addition, when resources are scarce, time is short, or expertise is lacking in individual tasks, an open software framework makes external programming of work packages possible and allows all modules to be seamlessly combined to form an overall project. This helps you to assign tasks to your employees that suit their strengths, to effectively protect know-how, and to meet deadlines when delivery dates are tight.
The modularity is designed differently, depending on the type of framework. An open framework gives users maximum freedom and provides application programming interfaces (APIs) for integrating their own solutions.- Safety: service, maintenance, sustainability
A software framework is constantly being improved. New features that have been tried and tested in other projects are regularly added. Bug fixes and compliance with new legal requirements are also part of ongoing development. New security requirements such as the Cyber Resilience Act and amendment of industry standards such as SEMI standards in the semiconductor industry are also important aspects that are considered. This benefits users of the framework, since they can implement new requirements more quickly and easily in projects.
Cybersecurity is more important than ever before, especially when it comes to new trends and innovative technologies. Because of their focused approach, framework providers are more able to manage the balancing act between using the latest technologies, long-term availability and providing security updates.
How do our customers work with the ToolCommander® software framework?
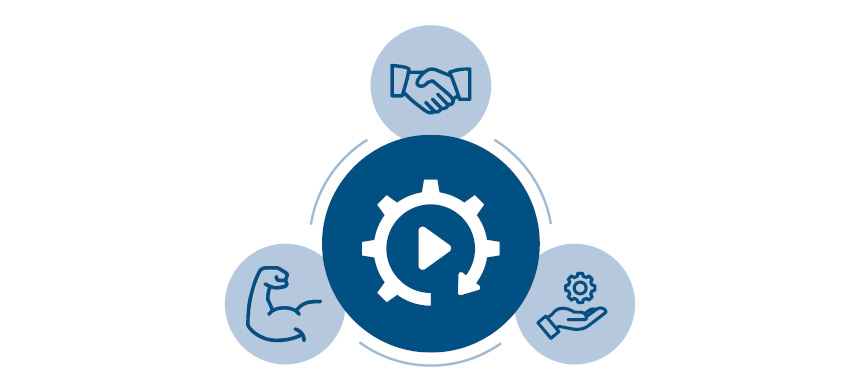
Openness, flexibility, and modularity are the pillars of the product philosophy and values that are put into practice in the field.
On your way to your equipment control, you decide for yourself how much of the programming work you do yourself. We offer you 3 ways to work together towards your goal:
Independent development
With the ToolCommander® software framework, you develop your equipment control entirely on your own and completely independent with C#/.NET. ToolCommander® is not only suitable for programmers with in-depth knowledge of C#, but also for software engineers and automation specialists for whom programming is just one of several tasks in their day-to-day business. You will be supported by a tutorial, comprehensive documentation, and special features in the framework itself. The terms used are based on the language in equipment manufacturing. For example, we talk about actual and target values, not about properties with getters (get) and setters (set), as would be usual in programming with modern high-level languages such as C#. We are always there if you need us and offer you training, consulting and support.
Joint development
Stay flexible and distribute your work packages as best fits your time capacities, experience, and efforts to protect your specialist knowledge and intellectual property, such as your process procedures. We take care of your partially outsourced development tasks and thus develop your equipment control together with you using ToolCommander®. If necessary, we are at your disposal with training, consulting and technical support.
Outsourced
If you have insufficient time and experience to implement it, feel free to call on our know-how and over 30 years of experience in control programming for systems. We will then develop your ToolCommander® equipment control precisely to your requirements.
Implementing your equipment control with ToolCommander®
There are many fundamental questions to be answered as part of project planning. Do you need a GUI as well as the control system and how should it be integrated? Should a PLC be combined with the PC-based control system? Should I/Os and components be addressed directly by ToolCommander® or communicate via a PLC? Is an industry-specific host connection required? The modular design of the ToolCommander® software framework allows you as a user to individually assemble the components of your equipment control. The individual project components are brought together as NuGet packages. Adjustments and extensions necessary due to new requirements or external regulations are possible even after completion of the equipment control.
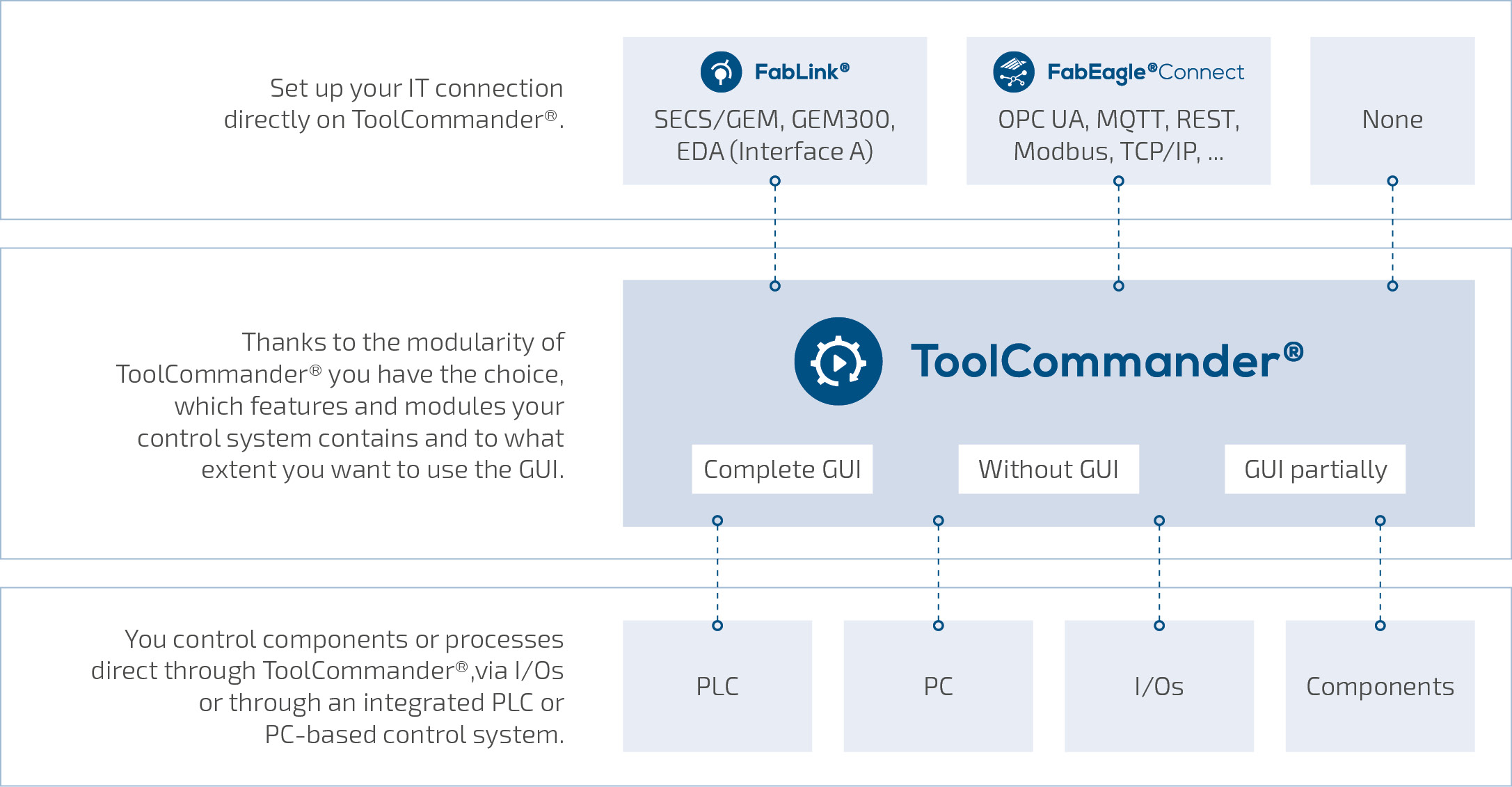
With more APIs than ever before, existing solutions and systems are easily integrated into the machine control, eliminating redundant programming tasks.
IPC control or PLC — the best of both worlds
The choice between software control on industrial personal computers (IPCs) or a pure programmable logic controller (PLC) is an essential aspect when implementing equipment control. IPCs offer flexibility and computing power for complex tasks, while PLCs are often preferred in simple to medium-complex applications due to their real-time capability and robustness. A software framework can combine both approaches. This allows you to profit from the benefits of both technologies.
ToolCommander® in semiconductor industry
A particular strength of the ToolCommander® framework is its suitability for the semiconductor industry, as it already supports compliance with the relevant SEMI standards. This helps developers and engineers tofaster and more safely implement equipment controls that are accepted in the semiconductor market. Read more about equipment control in the semiconductor market here. Visit the ToolCommander® product page to find out which specific SECS/GEM, GEM300 and EDA SEMI standards are supported by ToolCommander®. Learn more about SECS/GEM, GEM300 and EDA, their purpose and individual standards in our SEMI standards overview.
Conclusion
With a software framework for equipment control such as ToolCommander®, you can use your resources efficiently — when developing the system control, you build on basic components that are already available and, thanks to the reduced initial effort, you can focus on your core competences. The open approach allows you to flexibly distribute work packages, select relevant modules according to the project, and design and modify them in such a way that they perfectly meet your customers’ requirements. You receive expert assistance in the form of professional advice, support, and feature and security updates. With C#/.NET, you are also building on modern and future-proof technology and, thanks to its modularity and extensive documentation, can enable several people to work on your equipment control.
Would you like to find out more about the ToolCommander® software framework? Lets have a chat!
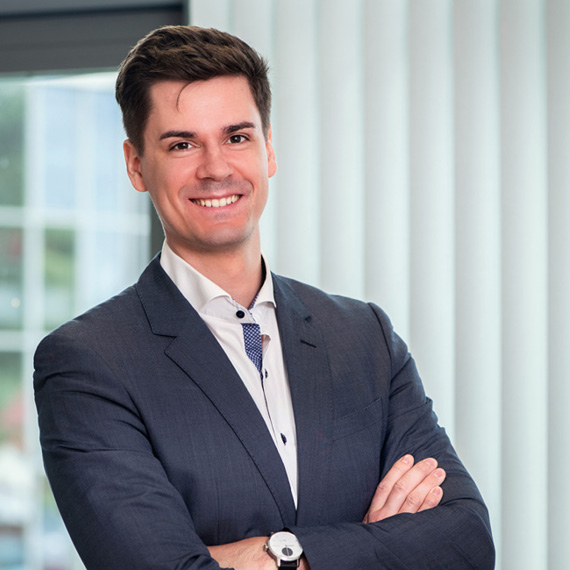