The new version of the manufacturing execution system FabEagle®MES offers three important new features that are specifically designed to meet the requirements of dynamically growing solar cell and solar module manufacturing with production capacities of at least 1 GW. The MES supports the most important steps in production with traceability and process monitoring and as a result helps with quality assurance, process optimization and cost reduction.
The new version provides active transport control for configurable material deployment of complex material flow systems in solar module factories. Production routing and process machines are controlled based on product type, quality and status information. In addition to standard processes, this also includes bypass and unloading requirements. This level of flexibility allows rapid alignment with changing production requirements while optimizing production processes.
The new module defect report is a robust standardized reporting tool that enables the evaluation of product defects from inspection and rework stations at cell and string level. A heat map overview allows the data to be visualized according to location, defect code and frequency. That is how real-time monitoring can be implemented to quickly identify problem areas in production and initiate improvement measures.
Long-term data storage is indispensable for the production of solar cells and solar modules. Using the advanced data history for mass production based on data lake technology, data formats have been optimized for easy evaluation using standardized toolsets. Combined with machine data pertaining to quality, tracking and performance, this provides the ideal basis for comprehensive data analysis and process control. As a result, not only can expanded analysis functions be used, but also full compliance with quality and regulatory specifications is ensured.
Want to know more about FabEagle®MES? I would be happy to help you.
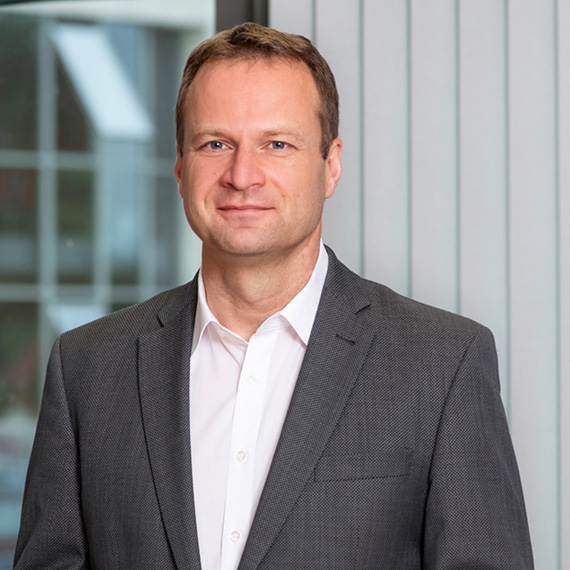