Hersteller, die Solarzellen mit höchstem Wirkungsgrad produzieren möchten, müssen moderne Zellarchitekturen, leistungsstarke Produktionsmaschinen und Software zur Produktionssteuerung optimal ausnutzen. Die Qualität der Solarzellen kann jedoch erst am Ende des Herstellungsprozesses gemessen werden. Daher ist die Rückverfolgbarkeit von Abweichungen durch prozessbegleitend erfasste Daten von entscheidender Bedeutung für die Ursachenforschung und Qualitätsoptimierung. Hierbei spielt der Funktionsumfang des Manufacturing Execution Systems (MES) eine wichtige Rolle. Insbesondere das Single-Wafer-Tracking bringt als eine Erweiterung der Produktdatenerfassung messbare Vorteile. Diese spezialisierte Form der durchgehenden Prozesstransparenz ermöglicht Prozessingenieur*innen eine erhebliche Kostenreduzierung durch Verkürzung der Ramp-up-Phase. Anschließend werden die Produktdaten im MES zur kontinuierlichen Optimierung der Produktqualität und Prozessstabilität genutzt. In diesem Blogbeitrag erfahren Sie mehr über die Funktionsweise und den Nutzen von Single-Wafer-Tracking in der Photovoltaik-Industrie.
Single-Wafer-Tracking – Was ist das?
Single-Wafer-Tracking bezeichnet die prozessübergreifende Nachverfolgung und Überwachung des Herstellungsprozesses von Solarzellen auf Wafer-Ebene. Dabei werden einzelne Wafer auf ihrem Weg durch die Produktion verfolgt und mit Prozessdaten verknüpft. Während beim physischen Single-Wafer-Tracking Markierungen wir QR-Code auf den Wafern erforderlich sind, benötigt das virtuelle Single-Wafer-Tracking diese Markierungen nicht, da lediglich Transport- und Prozesscarrier eindeutig z.B. mittels RFID identifizierbar sein müssen.
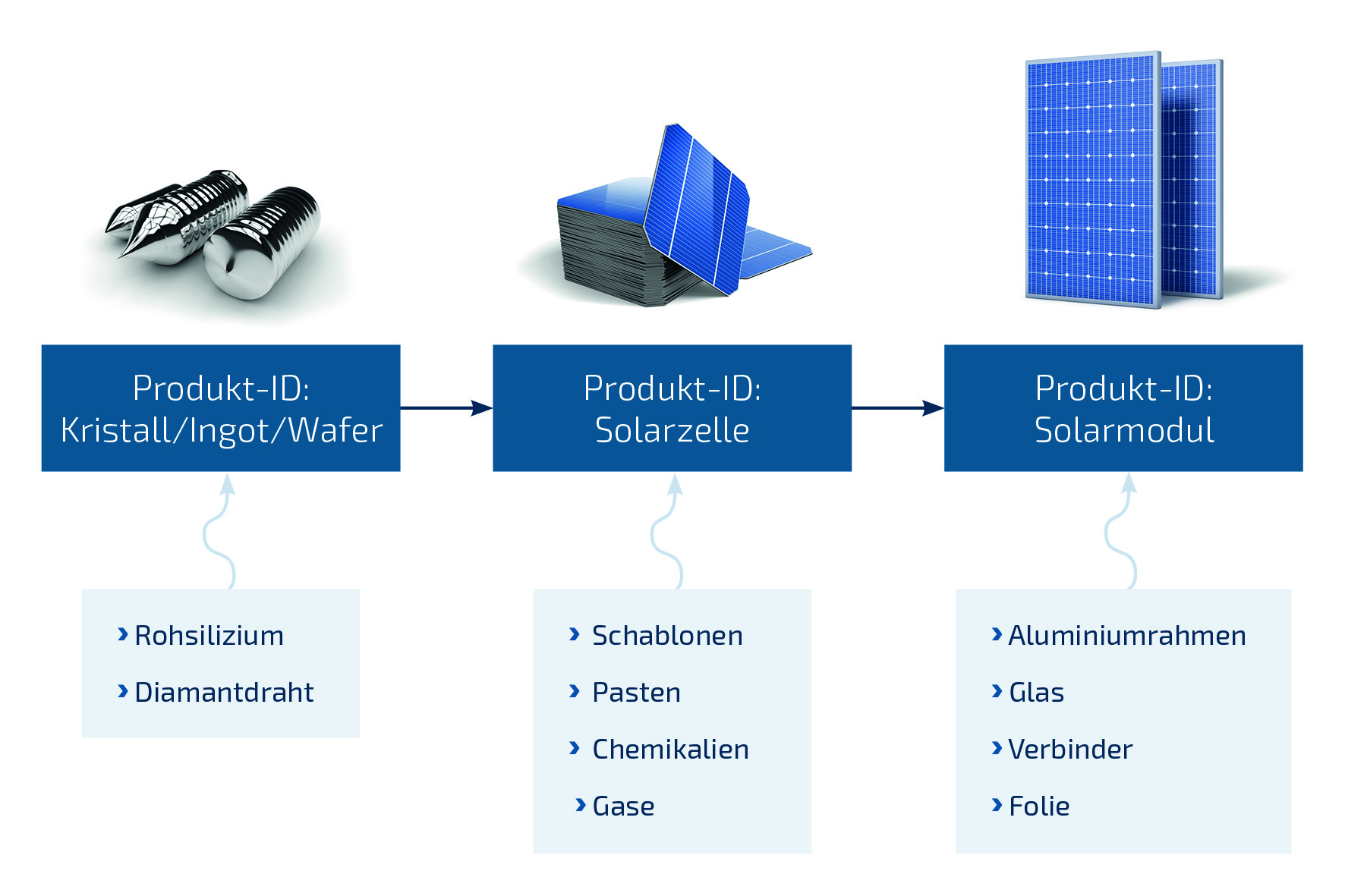
Vergleich zwischen virtuellem und physischem Tracking
Funktionsweise von physischem Tracking
Das physische Tracking von Materialien oder Produkten erfordert Markierungen, die eine eindeutige Identifikation ermöglichen. Diese Markierungen bestehen meist aus einer codierten Produkt-ID, die als QR-Code, Barcode oder als RFID-Chip zu Beginn des Produktionsprozesses aufgebracht wird. Diese Produkt-ID wird im MES-System als Identifikator dokumentiert und mit den Prozessdaten verknüpft. Innerhalb der Produktionslinie z.B. bei der Beladung einer Produktionsmaschine wird diese Markierung erfasst und zusammen mit neuen Prozessdaten an das MES übermittelt. Einfachere Formen des physischen Tracking fassen mehrere Produkte zu einer Charge zusammen, die über eine gemeinsame Chargen-ID identifiziert werden können.
Herausforderungen von physischem Tracking
- Markierungen auf Wafern können die Zellqualität beeinträchtigen, indem sie die aktive Oberfläche z.B. durch Laser bearbeiten.
- Die Lesbarkeit von Markierungen ist bei Prozessen zur Oberflächenbehandlung wie Ätzen oder Beschichten oft schwankend und kann die Trackingrate negativ beeinflussen.
- Physisches Tracking ist mit hohen Anschaffungskosten für Markierungslaser und Lesegeräten (z.B. Kameras) an jedem Prozessschritt verbunden.
- Der Detailgrad des physischen Trackings eines Wafers beschränkt sich auf den Eintritt und das Verlassen der Wafers in einem Prozess. Innerhalb der Prozesse erfolgt keine weitere Positionserfassung und Rückverfolgung durch die Prozessmaschine.
- Die Herstellung von Solarzellen erfolgt oft mit Carriern oder Trays, in denen mehrere Wafer gleichzeitig prozessiert werden. Da die Position eines Wafers in den Carriern und Trays einen Einfluss auf die Qualität hat, ist eine vollständige Nachverfolgung jedes Wafers für die Prozessoptimierung relevant.
Funktionsweise von virtuellem Single-Wafer-Tracking
Das virtuelle Tracking setzt auf ein Zusammenspiel von Carrier-Tracking, Tracking-Informationen von Prozessmaschinen und einer umfassenden Tracking-Historie im MES. Produkte werden anhand von Positions- oder Carrier-Wechsel durch die Produktionslinie verfolgt und mit Prozessdaten verknüpft. Das MES erfasst und orchestriert alle Carrier- und Produktbewegungen. Genau genommen ist es eine Erweiterung und Detaillierung des physischen Trackings, da die Carrier klassisch physisch z.B. mittels RFID identifiziert werden und erst durch die Tracking-Historie im MES vervollständigt wird. Eine erhöhte Trackingrate verbessert die Datenlage und Statistik, die als Grundlage für das Qualitätsmanagement dient und Ausgangsbasis für die Optimierung von Prozessstabilität und -qualität ist.
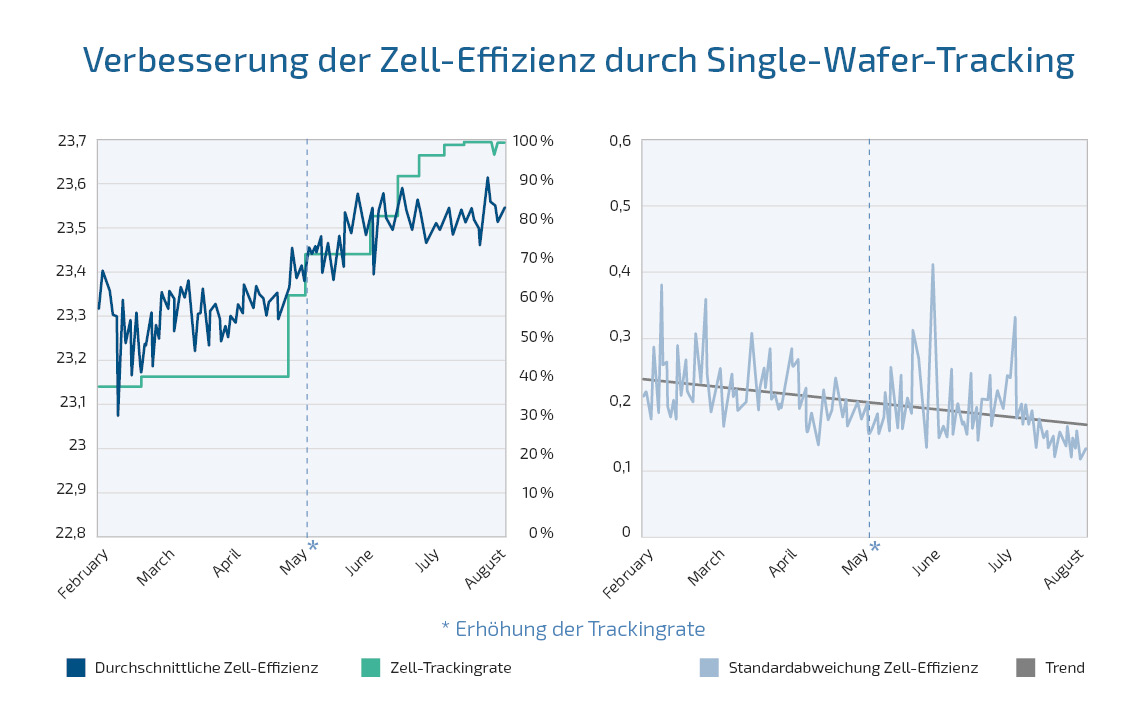
Herausforderungen von virtuellem Tracking
- Maschinensteuerungen müssen eine Schnittstelle für die Kommunikation der virtuellen Trackinginformationen zum MES bereitstellen.
- Positionswechsel der einzelnen Wafer durch die Prozesse müssen durch die Maschine verfolgt werden, was auch Carrier-Wechsel umfasst.
- Die Entnahme einzelner Wafer bzw. Waferbruch muss durch die Maschine erkannt werden, um Trackingverluste zu vermeiden.
Virtuelles und physisches Single-Wafer-Tracking im FabEagle®MES zur Datenkorrelation und -auswertung
Unser FabEagle®MES unterstützt sowohl physisches als auch virtuelles Single-Wafer-Tracking, um eine größtmögliche Datenbasis für Optimierungen zu bieten. Die Nachverfolgung und Auswertung dieser Daten im FabEagle®MES ermöglichen eine präzise Analyse und Optimierung der Fertigungsprozesse. Hierbei spielen vor allem die integrierten Funktionen zur Korrelation verschiedener Datensätze und das Reporting statistischer Größen eine entscheidende Rolle.
Eine wichtige Funktion unseres MES ist die Nachverfolgung und Bereitstellung der Wafer-Daten. Durch die Erfassung von Positionsdaten und Prozesswerten kann z.B. eine Heatmap generiert werden, die eine Visualisierung der Zelleffizienz in Abhängigkeit von der Lage der Wafer in den Carriern und Prozesskammern ermöglichen. Diese Heatmap bietet einen klaren Überblick über die Verteilung der Produktqualität innerhalb der Prozesskammer und hilft dabei, potenzielle Schwachstellen im Prozess zu identifizieren und zu optimieren. Durch die Erfassung von Positions- und Zeitinformationen für jeden Wafer ist es zudem möglich, den Einfluss unterschiedlicher Prozessrouten zu analysieren. Diese detaillierte Analyse ermöglicht es, den Einfluss von Prozessparametern über die gesamte Produktion zu verstehen und gezielt zu optimieren.

Die Korrelation von Daten ist eine weitere wichtige Aufgabe des MES. Durch die Verknüpfung von Daten aus dem Zelltester am Ende der Produktion mit Prozess-, Qualitäts- und Rezeptdaten können Zusammenhänge zwischen verschiedenen Parametern identifiziert werden. So wird eine gezielte Analyse und Optimierung der Fertigungsprozesse ermöglicht. Darüber hinaus können auch Bilddaten aus Electroluminescence Imaging (EL-Imaging) in die Analyse einbezogen werden, um eine optische und elektrische Qualitätskontrolle durchzuführen und mögliche Defekte frühzeitig zu erkennen.
Ein weiteres wichtiges Werkzeug im MES ist die statistische Prozesskontrolle (SPC). Diese ermöglicht eine kontinuierliche Überwachung der Prozessstabilität und -qualität, indem sie Abweichungen von den Sollwerten frühzeitig erkennt und entsprechende Maßnahmen einleitet. Durch die Analyse von Trenddaten können zudem langfristige Entwicklungen und Tendenzen identifiziert werden, die als Grundlage für zukünftige Entscheidungen und Optimierungen dienen.
Ausblick für die Datenerfassung und -auswertung
Machine Learning für automatische Datenauswertung: Die Anwendung von Machine Learning auf die Datenbasis des MES wird eine präzise Analyse großer Mengen an Datensätzen ermöglichen, um Abhängigkeiten und Trends in den Produktionsprozessen zu erkennen. Auf deren Grundlage kann dann die Optimierung von Prozessen erfolgen.
Effiziente Datenspeicherung und -verwaltung in einem Data-Lake: Die Implementierung von Data-Lakes erleichtert die zentralisierte Speicherung und den Zugriff auf Daten mit unterschiedlichem Format und auf Datenquellen außerhalb des MES über längere Zeiträume hinweg.
Hybride Trackinglösungen für präzise Prozessverfolgung: Die Kombination aus virtuellem und physischem Tracking ermöglicht eine präzise Überwachung der Produktionsprozesse unter Einsatz verschiedener Technologien.
Anwendung in anderen Branchen wie der Leiterplattenherstellung: Das Single-Wafer-Tracking im MES kann auch in anderen Branchen wie der Leiterplattenherstellung eingesetzt werden, um Prozesse zu optimieren und die Produktqualität zu verbessern.
Fazit: Optimierung der Solarzellproduktion durch Single-Wafer-Tracking
Ein Manufacturing Execution System mit der Spezialisierung für Single-Wafer-Tracking spielt eine entscheidende Rolle bei der Optimierung der Solarzellproduktion. Durch die präzise Verfolgung und Überwachung jedes einzelnen Wafers während des gesamten Herstellungsprozesses können Hersteller schnell und nachvollziehbar die Zelleffizienz und die Produktqualität verbessern. Die Vorteile dieser Technologie liegen
- in der Kostenreduzierung durch Verkürzung der Ramp-up-Phase,
- in der kontinuierlichen Überwachung und Optimierung von Prozessen sowie
- in der Verbesserung der Datenlage und Statistik für das Qualitätsmanagement.
Der Einsatz von Machine Learning zur automatischen Datenauswertung, effizienter Datenspeicherung und -verwaltung mit Data Lake Architekturen, hybriden Trackinglösungen und die Anwendung in anderen Branchen wie der Leiterplattenherstellung sind vielversprechende Entwicklungen für die Zukunft. Diese Technologien bieten weiteres Potenzial zur Steigerung der Effizienz und Qualität in der Fertigungsindustrie und unterstützen Hersteller dabei, den stetig steigenden Anforderungen gerecht zu werden.
Sie wollen mehr über Single-Wafer-Tracking erfahren? Ich helfe Ihnen gern weiter!
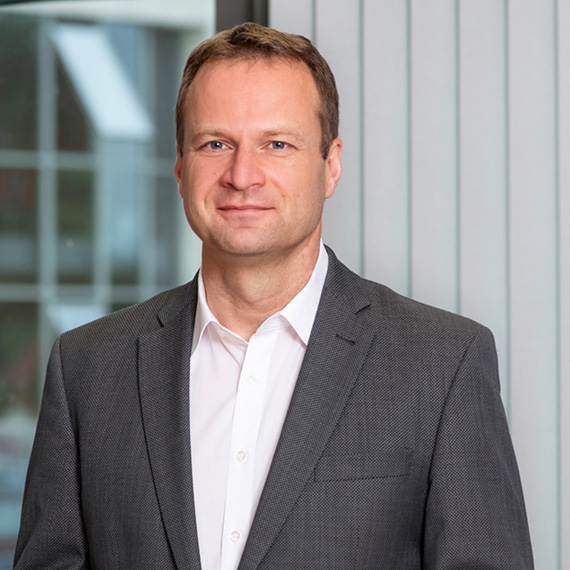