Im Maschinenbau sind Leistungsdaten von unschätzbarem Wert. Sie geben wertvolle Einblicke in die Prozesseffizienz und Funktionsweise von Maschinen und Anlagen. Während Alarme und Störungsmeldungen erste Hinweise auf den Maschinenzustand oder wichtige Anhaltspunkte für die Fehlersuche nach Schweregrad und Typ geben, geht die Datenanalyse von Prozesswerten einen Schritt weiter. Sie bietet eine vertiefende Datenanalyse von Ursachen und modulübergreifenden Zusammenhängen, die den Shopfloor sowie den gesamten Maschinen- und Anlagenpark betreffen.
Es wird zwischen verschiedenen Prozesswerttypen unterschieden:
- Numerische Prozesswerte: Hierbei handelt es sich um ganze Zahlen oder Gleitkommazahlen. Es können die Notation als auch die Grenzen konfiguriert werden. Dieser Prozesswerttyp ist eine typische Regelgröße.
- Textuelle Prozesswerte: Dieser Prozesswerttyp kann alle alphanumerischen Zeichen enthalten.
- Boolesche Prozesswerte: Diese Daten sind binär und zeigen beispielsweise an, ob ein Schalter an oder aus ist.
So werden Prozesswerte erfasst und konfiguriert
Im Maschinen- und Anlagenbau werden Prozesswerte produktionsnah über Sensoren und Aktoren erfasst und bei automatisierten Anlagen in der Regel über eine Steuerung oder in einer Datenbank gebündelt. Vor der Visualisierung der Prozessdaten erfolgt in der Regel eine Vorverarbeitung der anfallenden Daten über ein lokales Edge-Device, dass sowohl als Puffer dient als auch Daten für die Weitergabe an On-Premise- oder Cloud-Lösungen vorfiltert. An dieser Stelle wird die Datenverarbeitung je nach Programmieroberfläche programmiert oder lediglich konfiguriert. So werden die Prozesswerte von einer industriellen Schnittstelle der Anlage (z.B. MQTT, S7, HTML-Datenbanken) einfach in die Zielschnittstelle wie z.B. den Webstandard REST übersetzt. Neben der Konfiguration über REST können die Prozesswerte auch manuell oder mittels CSV-Import in der Ziellösung konfiguriert werden.
Exkurs: Transparenter Umgang mit sensitiven Maschinendaten
Ein datengesteuertes, digitales Shopfloor Management gewinnt für Anlagenbetreiber zunehmend an Bedeutung – auch im Mittelstand werden die Anforderungen an den Automatisierungs- und Digitalisierungsgrad immer höher. Die Investitionen in umfassende IT-Lösungen für Echtzeitauswertungen des meist sehr heterogenen Maschinenparks sind jedoch sehr hoch. Maschinenbauer kennen die Herausforderungen der Anlagenbetreiber und haben selbst ein großes Interesse daran, die Gesamtanlageneffektivität zu verbessern und die eigenen Maschinen über die Inbetriebnahme hinaus unter Last besser zu verstehen, um den Service und Support proaktiver und vorausschauender auszurichten. Immer mehr Maschinenbauer ergreifen daher selbst die Initiative und bieten den Anlagenbetreibern Echtzeitauswertungen als digitalen Service im Rahmen eines Wartungs- oder Servicevertrags mit Zugang zu einem Kundenportal an.
Das Teilen von Leistungsdaten einzelner oder mehrerer Maschinen auf Prozessebene mit dem Maschinenhersteller fällt dabei nicht allen Anlagenbetreibern leicht. Sie sind sich zwar der Vorteile bewusst, betrachten die Prozesswerte aber als geistiges Eigentum, dessen Preisgabe Rückschlüsse auf den eigenen Produktionsprozess zulässt und dessen Verlust zu Wettbewerbsnachteilen führen kann.
Ein transparenter Umgang mit den für die Maschinenbetreiber sensiblen Maschinendaten kann hier Brücken bauen. Das beginnt bereits bei der Kommunikation des Servicepakets und der Nutzungsbedingungen, um beiden Seiten klar aufzuzeigen, zu welchem Zweck die einzelnen Maschinendaten erfasst werden und welche Mehrwerte sich daraus für den Produktionsprozess ergeben. Dies setzt sich fort in der gemeinsamen Auswahl des gewünschten Datenumfangs im Zuge der Maschinenanbindung und der Option zukünftiger Erweiterungen durch entsprechende Konfiguration. Den Abschluss bildet die transparente Visualisierung der Maschinendaten für Hersteller und Betreiber in einer zentralen Plattform – On-Premise oder in der Cloud.
Prozesswerte visualisieren und auswerten
Die Vorteile einer vertiefenden Auswertung von Prozesswerten liegen für den Maschinenbauer auf der Hand:
- Überregionale und typbezogene Vergleiche
- Proaktiver Service durch frühzeitige Benachrichtigung bei Über- oder Unterschreitungen von Grenzwerten
- Wichtige Rückschlüsse auf Funktion, Betrieb und Wartungsfrequenz für die Produktentwicklung
Mit den genannten Vorteilen ist es offensichtlich, dass Maschinenbauer davon profitieren, wenn sie eine datenbasierte Strategie einsetzen. Die Frage ist jedoch: Wie können diese Daten effektiv genutzt werden, um die Effizienz zu steigern? Hier kommt die Digitalisierungslösung EquipmentCloud® ins Spiel. Die Kontron AIS hat für den Service und After Sales im Maschinen- und Anlagenbau die passenden Auswertungstools geschaffen, um diese auch dem Anlagenbetreiber als Kundenportal zur Verfügung zu stellen.
Im Monitoring-Modul der EquipmentCloud® können einfache Ad-hoc-Auswertungen für einzelne Maschinen oder bestimmte Maschinentypen durchgeführt werden, indem verschiedene Prozesswerte in Einzeldiagrammen korreliert und implizit gespeichert werden. So lassen sich unvorhersehbare oder dringende Analysen schnell und einfach realisieren.
Sind jedoch komplexere und regelmäßige Auswertungen von Prozesswerten über einen längeren Zeitraum geplant, bietet es sich an, stattdessen mit sogenannten Profilen zu arbeiten. Im Gegensatz zur Ad-hoc-Auswertung kann jedes Profil mehrere Diagramme enthalten und die Diagramme sind hinsichtlich dynamischer Zeitfilter (Alternative: Zoom In und Out) miteinander synchronisiert.
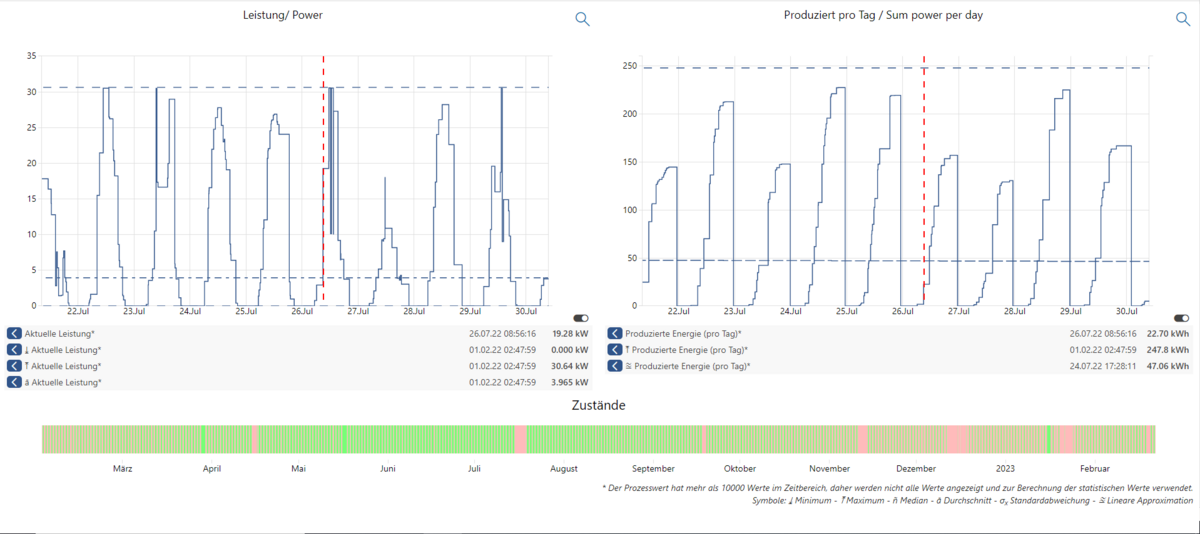
Darüber hinaus kann jedes Diagramm in einem eigenen Browser-Tab oder im Vollbildmodus geöffnet werden. Der große Vorteil von Profilen ist, dass einmal privat angelegte Profile auch später noch an Kolleg*innen, Kund*innen oder Partner*innen freigeben werden und auch Sichtbarkeitslevel definiert werden können. Voraussetzung ist, dass Nutzer*inen Zugriff auf die Equipment Hierarchie erhalten. Die Profile dienen auch als Navigationsmenü, d.h. einzelne Hierarchien können mehrere thematisch gruppierte Profile haben.
Dies bietet dem Maschinenbauer den Vorteil, dass er nach der Anbindung der Kundenanlage je nach gewähltem Servicepaket entweder eine Auswahl an Standardprofilen durch eine praktische Kopierfunktion in wenigen Klicks zur Verfügung stellen kann. Alternativ bespricht er mit dem Anlagenbetreiber im Detail, welche Prozesswerte relevant sind und erstellt diese in individuellen Profilen.
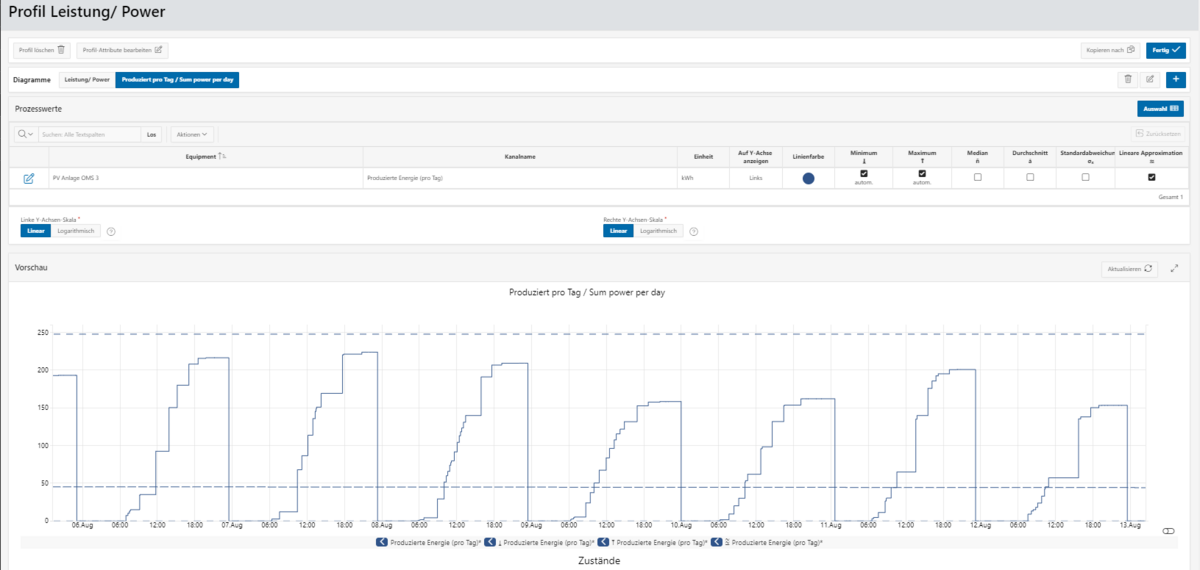
Die Auswertung selbst wird mit zahlreiche Attributen unterstützt, die pro Diagramm innerhalb eines Profils festgelegt werden können, z.B.:
- individuelle Farbwahl der Kanäle,
- ausblendbare Y-Achsen und Legenden,
- definierbare Maßeinheiten und Tooltips für die Diagramme
- statistische Mittel wie Maximum und Minimum, Median, Durchschnitt, Standardabweichung und lineare Approximation.
Damit steht Prozessingenieur*innen oder auch serviceorientierten Applikationsingenieur*innen ein umfangreiches Toolset zur Verfügung, um:
- Leistungsdaten einzelner Maschinen zu analysieren
- Energie- und Ressourcenverbräuche zu quantifizieren und
- Prozessbedingte Service- und Qualitätsanalysen unabhängig vom Standort anlagenübergreifend durchzuführen.
- Prozesswerte weiterverarbeiten
Neben der vertiefenden Datenanalyse spielen Prozesswerte auch für die Wartung und Instandhaltung eine wesentliche Rolle. Sie können als Auslöser (Trigger) in Form von wechselnden Schaltzuständen, Inkrementalzählern oder Grenzwerten für akute Reparaturen, geplante Wartungen oder Instandhaltungen dienen. Aus diesem Grund ist das Zusammenspiel kontinuierlicher Datenanalyse auf Prozessebene und der Historie tatsächlich durchgeführter Wartungen in der EquipmentCloud® integraler Bestandteil der Digitalisierungslösung. Die Integration von Monitoring und Maintenance-Modul ermöglicht wichtige Rückschlüsse auf Ursachen und trägt gleichzeitig dazu bei Wartungszyklen zuverlässiger zu prognostizieren.
Doch damit nicht genug: Die Bündelung der Maschinendaten an einem Ort wie der EquipmentCloud® bietet gute Voraussetzung, die Daten in Drittsystemen weiterzuverarbeiten und mit weiteren Informationen anzureichern und zu verdichten. Dem Maschinenbauer wie auch dem Anlagenbetreiber stehen hierfür eine umfangreiche Monitoring REST-API zur Verfügung. Eine Abfrage der konsolidierten Daten (dies sind insbesondere Prozessdaten, die je nach Datenfrequenz und Anzahl der Werten schnell ein hohes Datenaufkommen erzeugen) ist mittels mehrstufiger Authentifizierung über GET-Requests möglich. Für die Weiterverarbeitung in gängigen KI-Tools mit Python als Programmiersprache wurden ein sogenannter REST-API Wrapper als Python Modul geschaffen. Dies wurde als Projekt im Python Package Index veröffentlicht und kann mittels MIT-Lizenz als Open Source in Python Umgebungen installiert und genutzt werden. Die Monitoring REST-API und das darauf abgestimmte Python-Modul bieten vor allem Data Scientists ein unkompliziertes Datenstreaming über einen Zeitraum von mehreren Monaten und eine erleichterte Durchführung statistischer und Korrelationsanalysen auf Basis von Echtzeitdaten. Dadurch können KI-Lernmodelle entwickelt werden, die zukünftig als Trigger für Wartungs- und Instandhaltungsarbeiten an der Live-Anlage eingesetzt werden können.
Buchen Sie jetzt eine Live-Demo und entdecken Sie den Funktionsumfang der Datenanalyse auf Prozessebene in der EquipmentCloud® für Ihre Maschinen und Anlagen.