FabEagle®MES for solar cell and solar module production
In the transition to green energy, the photovoltaic (PV) industry is making a significant contribution to achieving the goal of 100 % renewable energy in the near future by providing high-efficiency solar modules for residential and utility-scale PV installations.
Solar cell manufacturing is one of the most crucial steps in the photovoltaics value chain for high efficiency solar modules. It relies heavily on the monitoring and control of manufacturing operations to ensure quality, improve processes and save costs. A Manufacturing Execution System (MES) is typically used to collect the necessary data and control production.
Meyer Burger has been in the process of transforming itself from an equipment vendor to a solar module supplier and was looking for an MES to support its production needs. Due to the proven track record in the PV industry and the functionalities offered, the FabEagle®MES from Kontron AIS was chosen to monitor and control manufacturing at Meyer Burger’s heterojunction technology (HJT) solar cell factory in Thalheim and the SmartWire solar module production facilities in Freiberg.
- Integration of several 100 machines of different types
- Collect track and trace data at single solar cell level
- Sharing data between the two MESs for solar cell and solar module production
- Introducing a tailored ACM process
- Implementation of virtual single wafer tracking
- Using a database to exchange data between production sites
- Reliable equipment interfaces
- Complete genealogy for solar modules
- Data availability for quality monitoring and ERP across multiple sites
This is what Meyer Burger's Fab Engineering Manager says about the collaboration
"The professional and seamless cooperation with Kontron AIS enabled us to quickly integrate the FabEagle®MES. In terms of efficiency and transparency, our new PV factories are operating at the next level.”
André Rolle, Manager Fab Engineering, Meyer Burger
Follow best practices to get projects off the ground
A challenging task in this project was to deliver an MES for the new production facilities within the given time frame to meet the agreed milestone for the start of production. Based on the already successfully completed automation projects, Meyer Burger and Kontron AIS were able to start immediately with the MES implementation, applying best practices learned from over 20 years of working in the PV industry.
The first two months were spent defining the functional requirements of the MES as well as the interfaces to the production equipment. While most pieces of the equipment in the solar cell production is fitted out with standard interfaces (SECS/GEM, PV02), some of the older, reused equipment in module production had to be connected via legacy proprietary interfaces.
Following the specification phase, a development team at Kontron AIS began configuring several hundred equipment interfaces and testing them with the tool vendors prior to delivery to ensure a smooth integration on site after delivery.
The task of equipment integration followed an adapted Automation Capability Management (ACM) process to ensure that the equipment interfaces worked to the agreed specifications from all equipment vendors.
Getting the project up and running
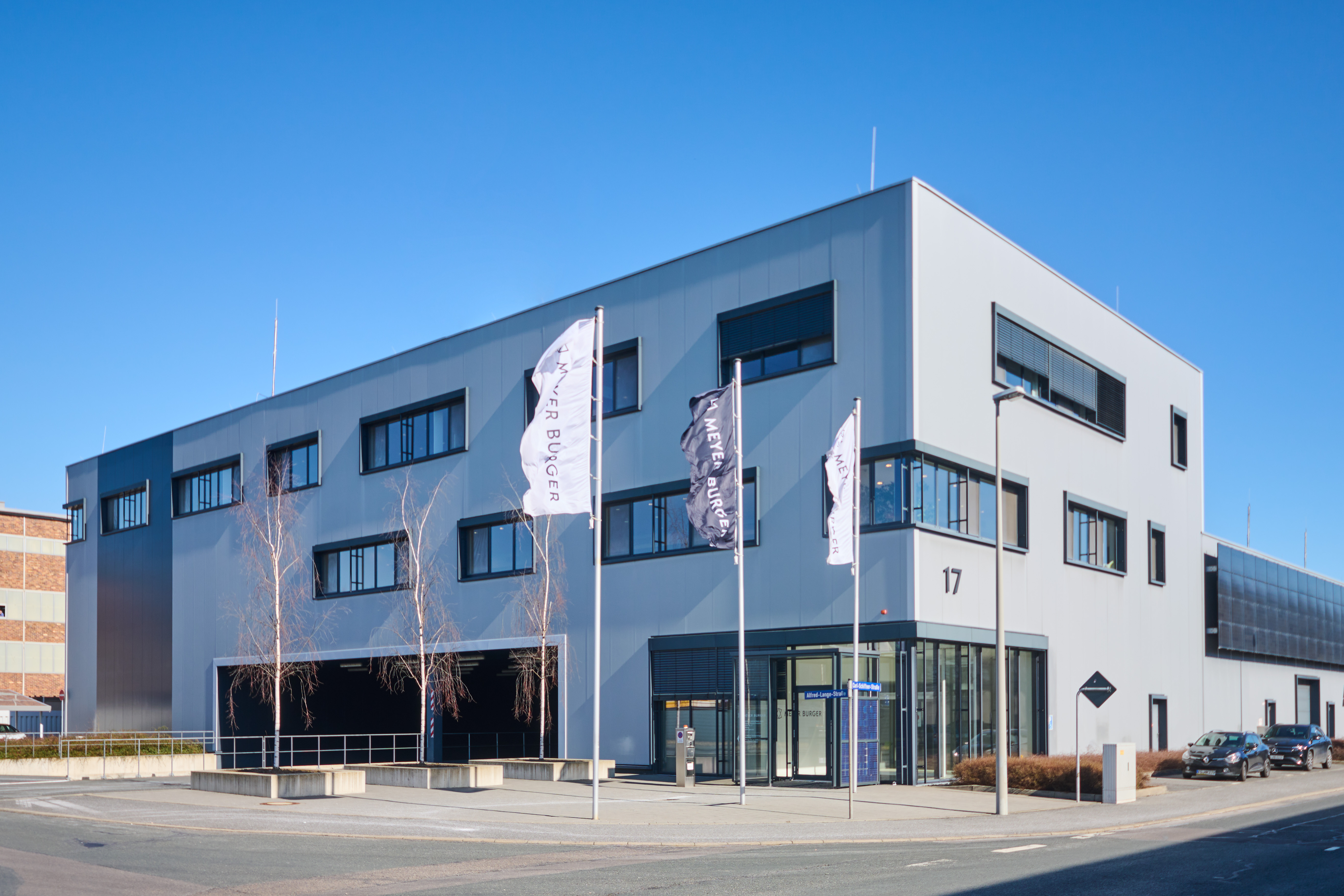
The close collaboration between the project managers from Meyer Burger and Kontron AIS was a major incentive right from the start. The required transparency regarding project progress and the tracking of obstacles was achieved through cyclical status and management meetings to make sure the necessary focus was applied to the crucial parts of the project. In particular, tracking the progress of the implementation and test of equipment interfaces from the various machine vendors was important in order to meet all the commissioning milestones.
For the operation of the MES, Meyer Burger provided the necessary virtualized IT infrastructure according to the required performance level and expandability for the future scaling of the production sites. In addition to the required IT server infrastructure, Meyer Burger also prepared the MES shop floor operator workstations. In close collaboration with the machine vendors and Meyer Burger, most of the work could be carried out remotely, which not only saved travel time, but also allowed an agile and flexible manner of working to complete the MES installations at the two production sites.
At the same time this helped to re-adjust the focus on a daily basis. Once the MES implementation phase was completed, the functional acceptance test (FAT) and extended material tracking tests were carried out. During this part of the project the training of the shop floor operators to support a smooth ramp-up phase of solar cell and module production also completed.
Solar cell production monitoring and control
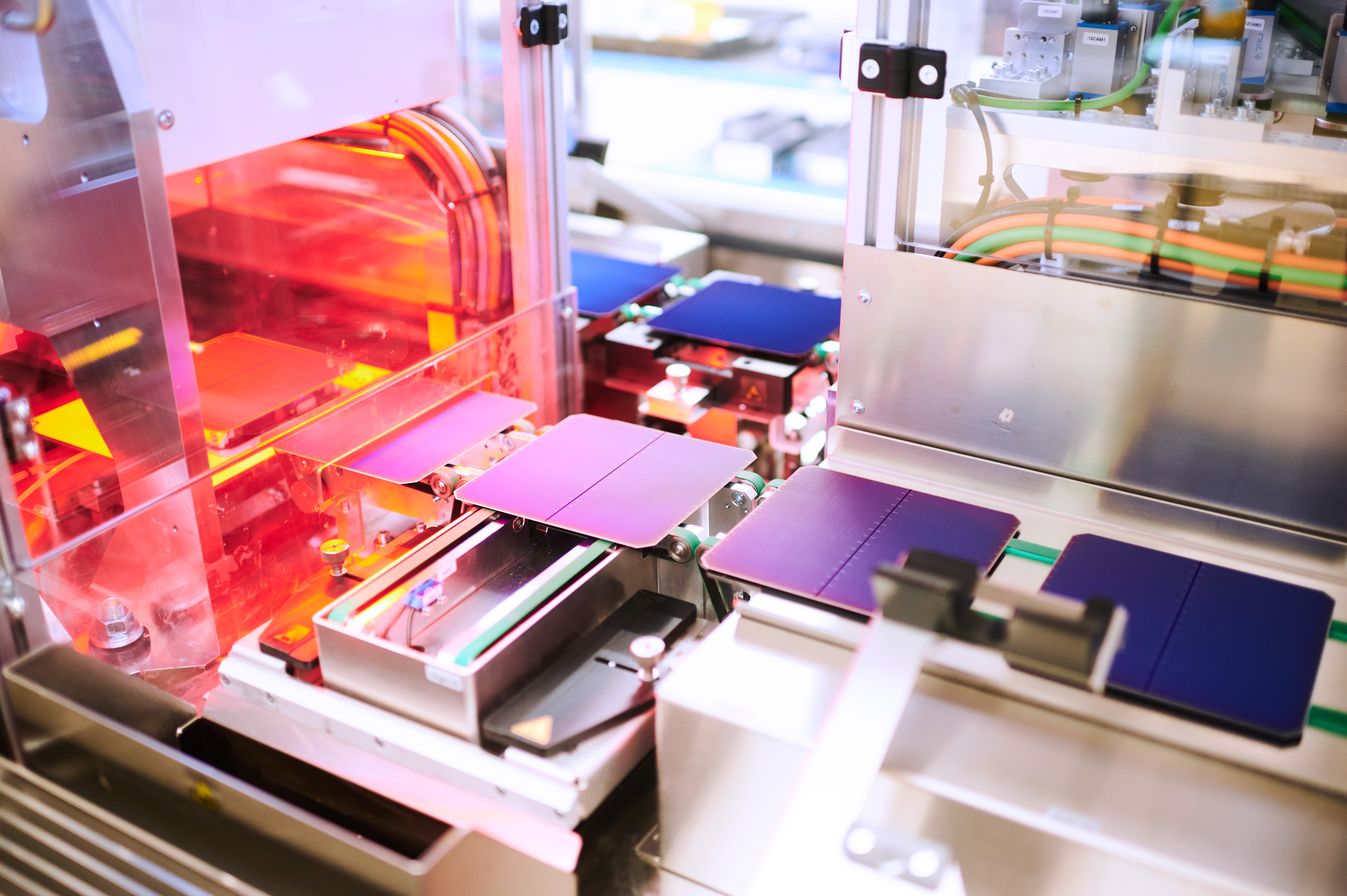
In order to closely monitor and control the production of high-efficiency solar cells, it is necessary to track every single wafer through all process steps within the manufacturing at the Thalheim site. Meyer Burger has chosen the approach of virtual wafer tracking instead of physical tracking by marking the wafers. By using the FabEagle®MES, process and quality data from equipment and measurement devices can be linked to individual wafers. Additional timestamps, such as process start and end times, as well as location change information, even within an equipment, can be collected and used to monitor and control production quality.
This achieved the goal to implement virtual tracking through all processes, beginning from incoming wafer inspection up to the classification and test equipment for final solar cells. At the shop floor level, generic operator workstations are used to monitor production and collect additional information for consumable tracking and manual data entry.
Besides the generic workstations, specialized stations for wafer commissioning and solar cell packaging have also been implemented. Via a transfer database material tracking is even extended to the module production line in Freiberg, so that data can be correlated from the raw material of the cells through all production steps to the finished solar module.
Monitor and control solar module production
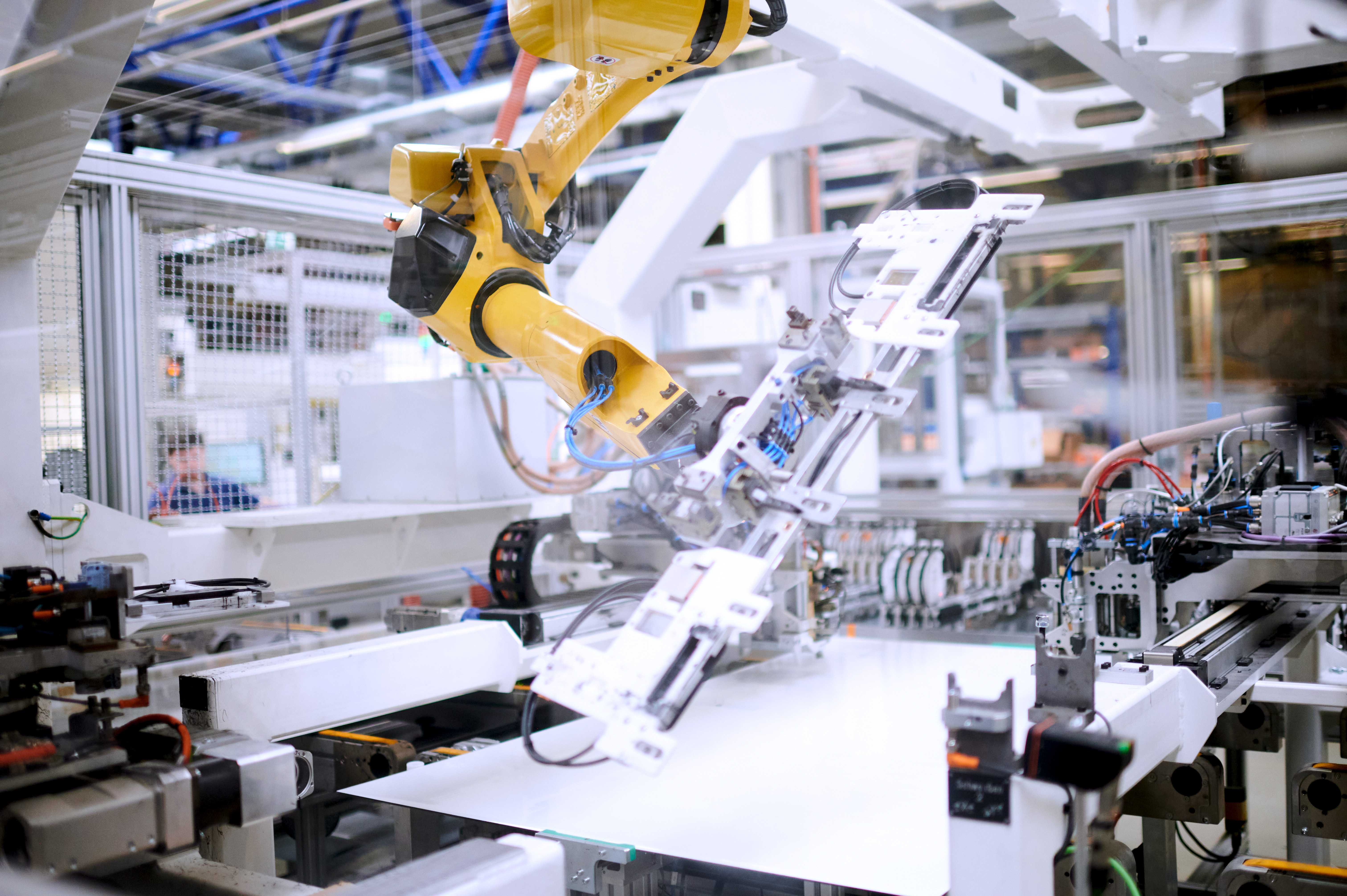
Graphical user interfaces (GUI) have been implemented and standardized for solar module manufacturing, e.g. for module inspection and rework as well as for the configuration and monitoring of automated palettizing of finished solar modules. These GUIs, operated via touch screen, are specifically designed to provide quick and efficient input options, allowing workers to keep up with the line cycle and still collect accurate data for quality management.
Each machine is integrated into the MES, starting with glass loading, stringers for solar cells, matrix layup, laminators, framing, etc. This enables Meyer Burger to collect all necessary quality and metrology data to monitor production and improve processes. In addition, the tracking of all consumables makes it possible to create a complete genealogy of each solar module.
Tracking raw materials to finished products
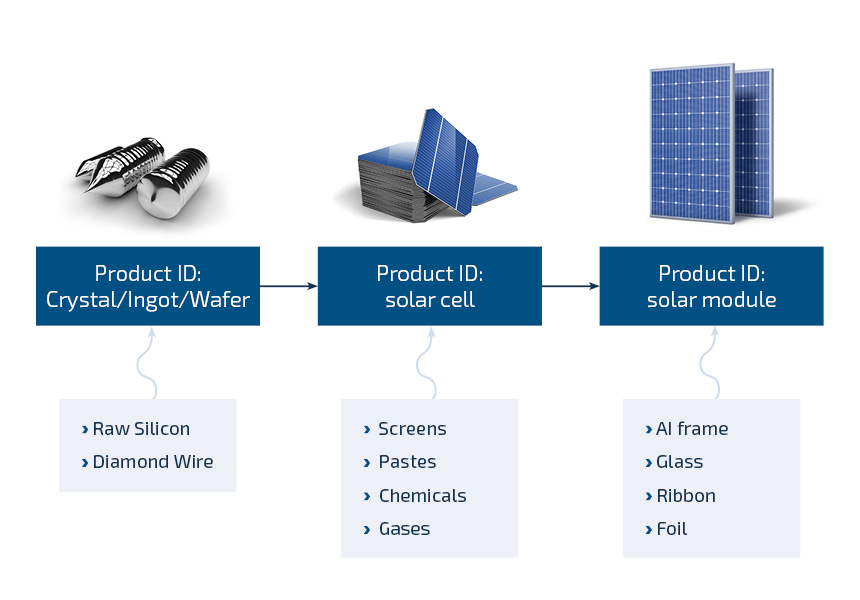
FabEagle®MES tracks every single solar cell through the production process and collects single material data, which is supplemented with process and equipment data. This complete tracking ensures that any defects or quality problems can be immediately identified and tracked down to be resolved as quickly as possible. The tracking up to the finished solar module is also the basis for the integration to ERP.
Summary and prospects
Kontron AIS took up the challenge and successfully delivered the FabEagle®MES on time and on budget. All of Meyer Burger’s production facilities – the solar cell factory in Thalheim and the solar module factory in Freiberg – are now operating with FabEagle®MES on a gigawatt production scale. Kontron AIS will continue to be a reliable partner for Meyer Burger on this exciting journey.
This project‘s exciting key figures
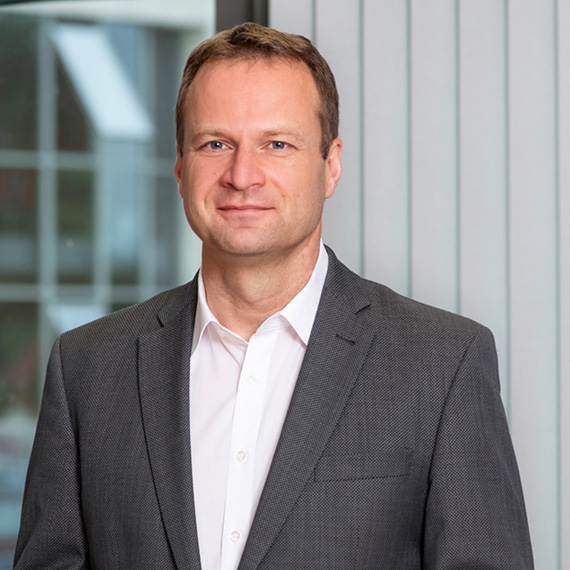